Iron & steel industry decarbonization
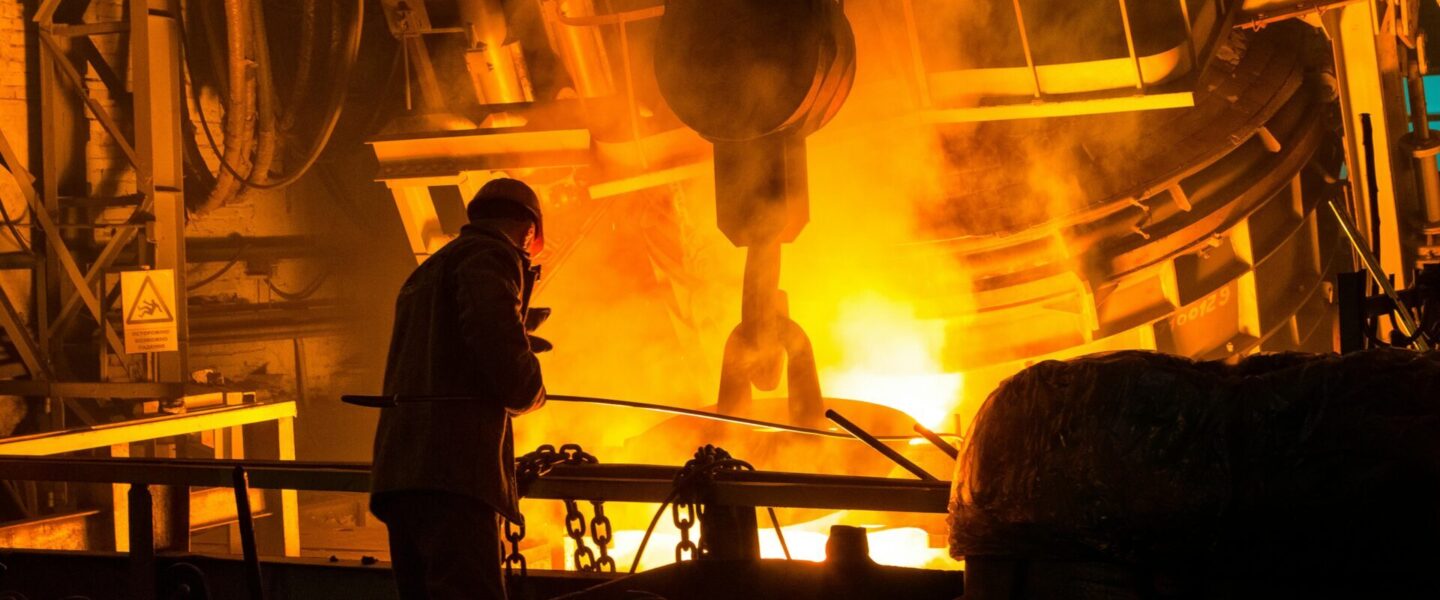
Electrification and decarbonization of iron and steel industry
The iron and steel industry is responsible for approximately 7-9% of global CO2 emissions, making it one of the largest contributors to industrial greenhouse gases. Historically labeled as challenging to decarbonize due to the reliance on fossil fuels in high-temperature processes like blast furnaces and reliance on carbon in the reduction process of iron, the sector faces significant hurdles in decarbonization and transitioning to a low-carbon future.
However, as steel producers strive to meet their net-zero goals, industrial electrification offers a powerful solution. By replacing traditional fossil-fuel-powered processes with innovative electric technologies, the steel industry has the potential to dramatically reduce emissions and contribute meaningfully to global climate goals.
Coolbrook’s RotoDynamic HeaterTM (RDH) is the only heat electrification technology capable of decarbonizing industrial heating processes up to 1700°C without burning fossil fuels. In addition to generating high temperatures, RDH can enable significant reduction in coal consumption in the blast furnace and higher energy efficient in hydrogen-based DRI-process. The technology can cut over 1,000 million tonnes of fossil fuel-derived CO2 in steel production per year globally through electric-powered heaters, eliminating the need to burn fossil fuels for process heat generation.
Optimal use cases for early adoption of RotoDynamic Heater
- Blast Furnace – combustion air and fuel gas heating in hot stoves:
significant reduction in gas consumption in hot stoves, 10% higher energy efficiency and reduced coke consumption, leading to significant decarbonization and cost benefits in the blast furnace process - Scrap preheating before EAF:
increase process throughput by up to 10% by reducing tap-to-tap time and improve process efficiency by ~2% due to improved energy efficiency - Preheating of raw materials for DRI:
significant reduction of (fossil) fuel consumption in DRI process by covering the heating duty with RDHTM technology - Indirect heating of hydrogen for DRI:
significant improvement in energy efficiency in hydrogen-based DRI process by covering significant part of the heating duty with RDHTM technology - Partial electrification of reheating furnaces:
significant reduction of fossil fuel consumption in reheating furnaces by covering part of the heating duty with RDHTM technology
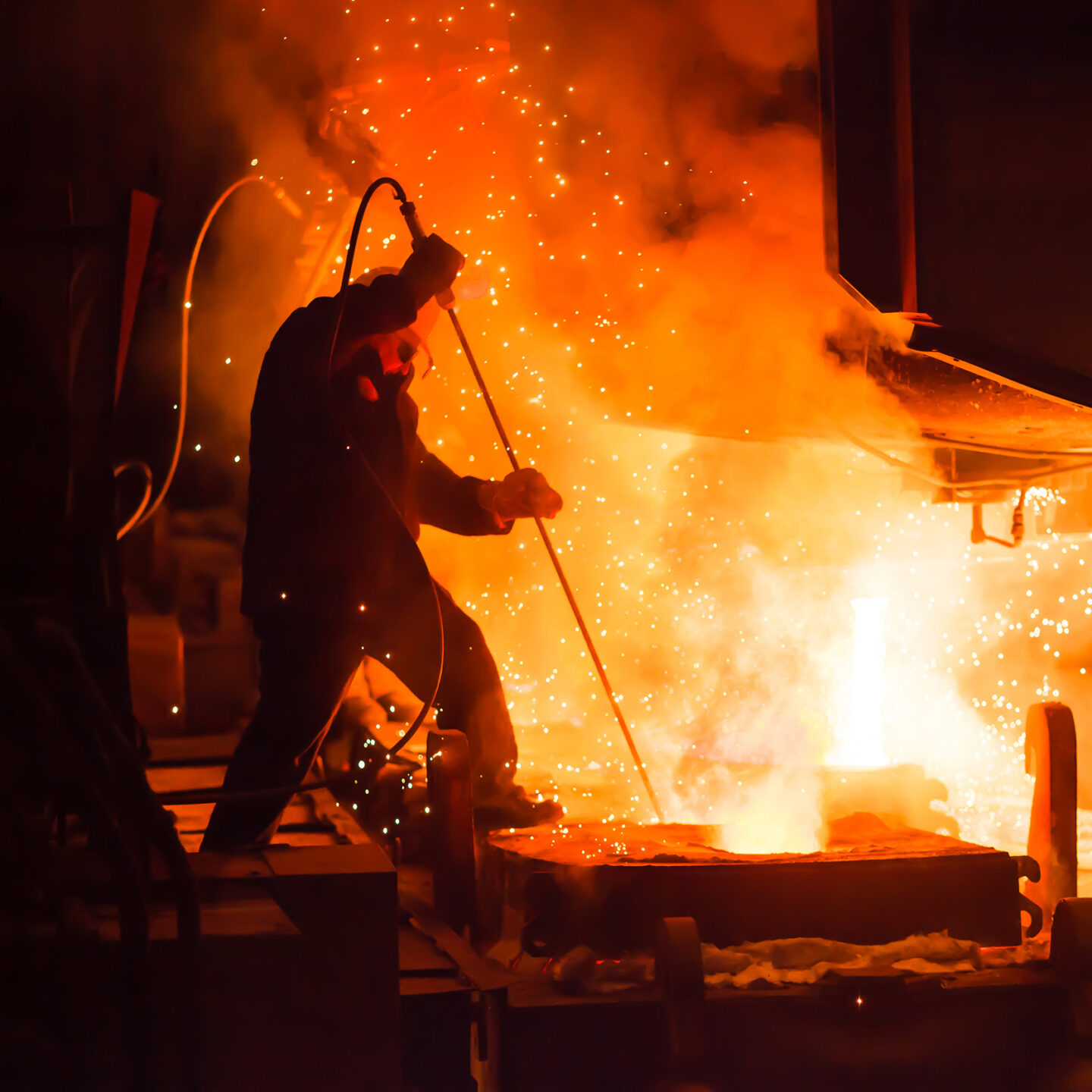
Discover
RotoDynamic Heater in iron and steel industry
RotoDynamic Heater heats gas, such as air, nitrogen, steam, carbon dioxide, and process gases, with electricity to required high process temperatures, and the heated gas is used outside the heater to replace the burning of fossil fuels in process heating.
There are multiple use cases in iron and steel production where the RotoDynamic Heater is an optimal solution for process heating and replacing the burning of fossil fuels. It can be used for example in blast furnaces, reheating furnaces or heat treatment to cover major part of the heating duty, leading to significant decarbonization and additional benefits, such as improved energy efficiency.
Key benefits of the technology:
- Scalability to high temperatures (up to 1700 ˚C degrees) and to size categories (50+ MW equipment size)
- Elimination of fossil fuel derived CO2, NOx and SOx emissions by replacing fossil fuels with electrification
- High energy efficiency of 90 – 95% for the conversion of electricity to heat
- Compact equipment size and possibility to retrofit into existing industrial facilities
- Improved process energy efficiency
- Improved process control, quality and yield
- Competitive CAPEX and OPEX
Contact us
Roadmap and process
Path to decarbonizing iron and steel processes
2025-26
First Applications
Blast Furnace:
- Preheating of hot stove air or fuel gas
- Preheating injection gas for tuyeres or shaft
- Partial electrification of coking oven
- Preheating O2 and scrap for BOF
- Preheating raw materials
DRI:
- Preheating raw materials
- Indirect preheating of reduction gas (incl. hydrogen)
EAF (scrap route):
- Preheating scrap for EAF
All routes:
- Partial electrification of reheating furnaces
- Full or partial electrification of heat treatment furnaces
- Preheating ladles and tundishes
2027-28
Full electrification of high temp. heat
Blast Furnace:
- Full replacement of hot stoves in BF
- Full electrification of pellet induration & sintering
- Full electrification of coking oven
DRI:
- Full electrification of pellet induration
EAF (scrap route):
- EAF boosting / replacing natural gas firing with RDH
All routes:
- Full electrification of reheating furnace
- Full electrification of heat treatment furnaces
2030+
Full decarbonization
Blast Furnace:
- CCS to capture process emissions from Blast Furnace and sintering processes to reach fully decarbonized operation
DRI:
- Direct pre-heating of reduction gas (incl. hydrogen)
Example use cases for decarbonizing iron and steel process
The RotoDynamic Heater can be fitted to new or existing industrial processes with multiple use cases in the iron and steel production chain to replace the burning of fossil fuels in the generation of process heat.
Ironmaking
1. Preheating (and drying) of raw materials
Use case and Coolbrook solution in brief
Pre-heating raw materials (e.g., iron pellets) before the ironmaking step in steel production to reduce the heating duty required Direct Reduction or Blast Furnaces
- Heating medium: Air or exhaust gas
- Temperature out: Up to 900˚C
Customer benefits
- Reduction CO2 emissions by replacing part of the fossil fuel-based heating duty with renewable electricity (Blast Furnace route)
- Decreased coke consumption in Blast Furnace
- Significant reduction in hydrogen consumption as part of the heating duty is covered by the RDHTM (H2 DRI route)
- Cost savings from reduced carbon emission costs as existing fossil fuel solution (natural gas, LPG, diesel, etc.) are replaced
- Ability to accurately control the temperature in the process to eliminate unwanted sintering before the furnace
- Improved process stability and elimination of disturbances caused by cold/wet/moist/icy raw materials
- Possibility to increase production capacity if top gas temperature is limiting oxygen enrichment (Blast Furnace route)
- Utilization of exhaust gas heat energy resulting in improved energy efficiency and reduced operating costs
2. Preheating fuel gas and/or combustion air for hot stoves (Blast Furnace process)
Use case and Coolbrook solution in brief
Preheating fuel gas and/or combustion air with RDHTM for the hot stoves before the Blast Furnace:
- Heating medium: Air, Blast Furnace Gas, Coke oven gas
- Temperature out: 900˚C
Customer benefits
- Significant reduction in CO2 emissions in Blast Furnace by replacing fossil fuels with renewable electricity
- Cost savings from reduced carbon emission costs as existing fossil fuel solution (natural gas, LPG, diesel, etc.) are replaced
- Up to 2+% reduction in coke consumption through increased temperature of hot stove (and hot blast)
- Potential to utilize low-priced renewable energy, further decreasing OPEX
3. Providing hot blast for Blast Furnace
Use case and Coolbrook solution in brief
Generating high temperature heat to the Blast Furnace process with RDHTM with possibility to fully eliminate the need for hot stoves:
- Heating medium: Air (+ Oxygen)
- Temperature out: 1,200˚C
- Elevated pressure for hot blast
Customer benefits
- Significant reduction in CO2 emissions in Blast Furnace by replacing fossil fuels with renewable electricity
- Cost savings from reduced carbon emission costs as existing fossil fuel solution (natural gas, LPG, diesel, etc.) are replaced
- Up to 2+% reduction in coke consumption through increased temperature of hot blast
- Significant CAPEX reduction as hot stoves are not needed anymore (in case of full replacement)
- Potential to utilize low-priced renewable energy, further decreasing OPEX
- Utilization of exhaust gas heat energy resulting in up to 10% higher energy efficiency and clearly reduced operating costs
4. Preheating injection gas to Blast Furnace Shaft and/or Tuyeres (Blast Furnace route)
Use case and Coolbrook solution in brief
Boosting the Blast Furnace efficiency by injecting high temperature heat generated by the RotoDynamic Heater to the Blast Furnace tuyeres and/or shaft:
- Heating medium: Natural gas or process gases (COG / treated BFG)
- Temperature out: 900-1,000˚C
Customer benefits
- Significant reduction in CO2 emissions generated in the Blast Furnace by replacing fossil fuels with renewable electricity
- Significant reduction in coke consumption through increased efficiency in the Blast Furnace
- Cost savings from reduced carbon emission costs as existing fossil fuel (natural gas, LPG, diesel, etc.) heating duty is replaced
- Potential to utilize low-priced renewable energy, further decreasing OPEX
- Utilization of exhaust gas heat energy resulting in improved energy efficiency and reduced operating costs
5. Heat generation for DRI process (DRI route)
Use case and Coolbrook solution in brief
Direct or indirect heating of reduction gas in the DRI route with high temperature heat generated RotoDynamic Heater:
- Heating medium: H2, natural gas, syngas, N2/CO2 (indirect)
- Temperature out: 900-1,200˚C
Customer benefits
Natural gas DRI route:
- Significant reduction in CO2 emissions by replacing fossil fuel burners with electrical solution
- Significant cost savings from reduced carbon emission costs as existing fossil fuel solution (natural gas, LPG, diesel, etc.) are replaced
Hydrogen DRI route:
- Significant reduction of H2 consumption as large part of the heating duty is done electrically, instead of burning H2 or other (fossil) fuels
- Fully fossil-free iron production with higher energy efficiency compared to alternatives
Both routes:
- Possibility to start with partial replacement of burners, already yielding significant benefits
- Potential to utilize low-priced renewable energy, further decreasing OPEX
- Utilization of exhaust gas heat energy resulting in improved energy efficiency and reduced operating costs
Steelmaking
6. Scrap preheating
Use case and Coolbrook solution in brief
Preheating scrap (for EAF or BOF) with heat generated electrically by the RotoDynamic Heater:
- Heating medium: Air
- Temperature out: Up to 800˚C
Customer benefits
- Increased process throughput by up to ~10%, enabled by RDHTM covering major part of the heating duty prior to EAF
- Improved process energy efficiency by ~2%, enabled by higher efficiency of preheating vs. EAF
- Lower CO2 emissions and cost through reduction in nominal consumption of electrodes and carbon for foaming
- Preheating can remove moisture (and melt the ice in selected locations) in the scrap, enhancing safety and avoiding downtime
Post-processing
7. Electrification of reheating furnace
Use case and Coolbrook solution in brief
Replacing burners in existing reheating furnaces with high temperature heat generated by the RotoDynamic Heater:
- Heating medium: Air, exhaust gas, CO2, N2, Argon
- Temperature out: 1,200-1,500˚C
Customer benefits
- Significant reduction in CO2 emissions or fully CO2 emission free reheating process by replacing fossil fuels with renewable electricity
- Possibility to start with partial replacement of burners, already yielding significant CO2 reduction
- Cost savings from reduced carbon emission costs as existing fossil fuel solution (natural gas, LPG, diesel, etc.) are replaced
- Utilization of exhaust gas heat energy resulting in significantly improved energy efficiency (20%) and reduced operating costs
- Improved yield (of 1-3%) as RDH enables using inert gases as heating medium that eliminates mill scale formation (i.e., oxidation of products)
- Potential to utilize low-priced renewable energy, further decreasing OPEX
8. Electrification of cold rolling mill equipment (heat treatment furnaces, burners in surface treatment)
Use case and Coolbrook solution in brief
Replacing burners at cold rolling mill in heat treatment furnaces (quenching, tempering, normalizing, annealing, etc.) and surface treatment lines (coating drying, galvanizing, etc.) by providing high temperature heat with the RotoDynamic Heater:
- Heating medium: Air, exhaust gas, CO2, N2
- Temperature out: 500-1,400˚C (very case dependent)
Customer benefits
- Significant reduction in CO2 emissions or fully CO2 emission free cold rolling mill operations by replacing fossil fuel with renewable electricity
- Possibility to start with partial replacement of burners, already yielding significant CO2 reduction
- Cost savings from reduced carbon emission costs as existing fossil fuel solution (natural gas, LPG, diesel, etc.) are replaced
- Utilization of exhaust gas heat energy resulting in significantly improved energy efficiency (20%) and reduced operating costs
- Higher yield / product quality, enabled by RDH’s ability to use inert gases as heating medium and the ability to control temperature more accurately
- Potential to utilize low-priced renewable energy, further decreasing OPEX
Hear from Coolbrook iron and steel customers and partners
JSW Group has set ambitious sustainability targets of reducing its specific CO2 emissions, aligning with the Sustainable Development Scenario of the International Energy Agency and India’s Nationally Determined Contributions. Deployment of RDH™ Technology is expected to have a sizeable impact on the decarbonization of the Group’s manufacturing process. We are happy to onboard Coolbrook as a partner on our journey to reduce CO2 emissions and achieve our climate targets.
PK Murugan, President
JSW Steel Vijayanagar & Salem Works