RotoDynamic Electrification Solutions to decarbonize industrial processes
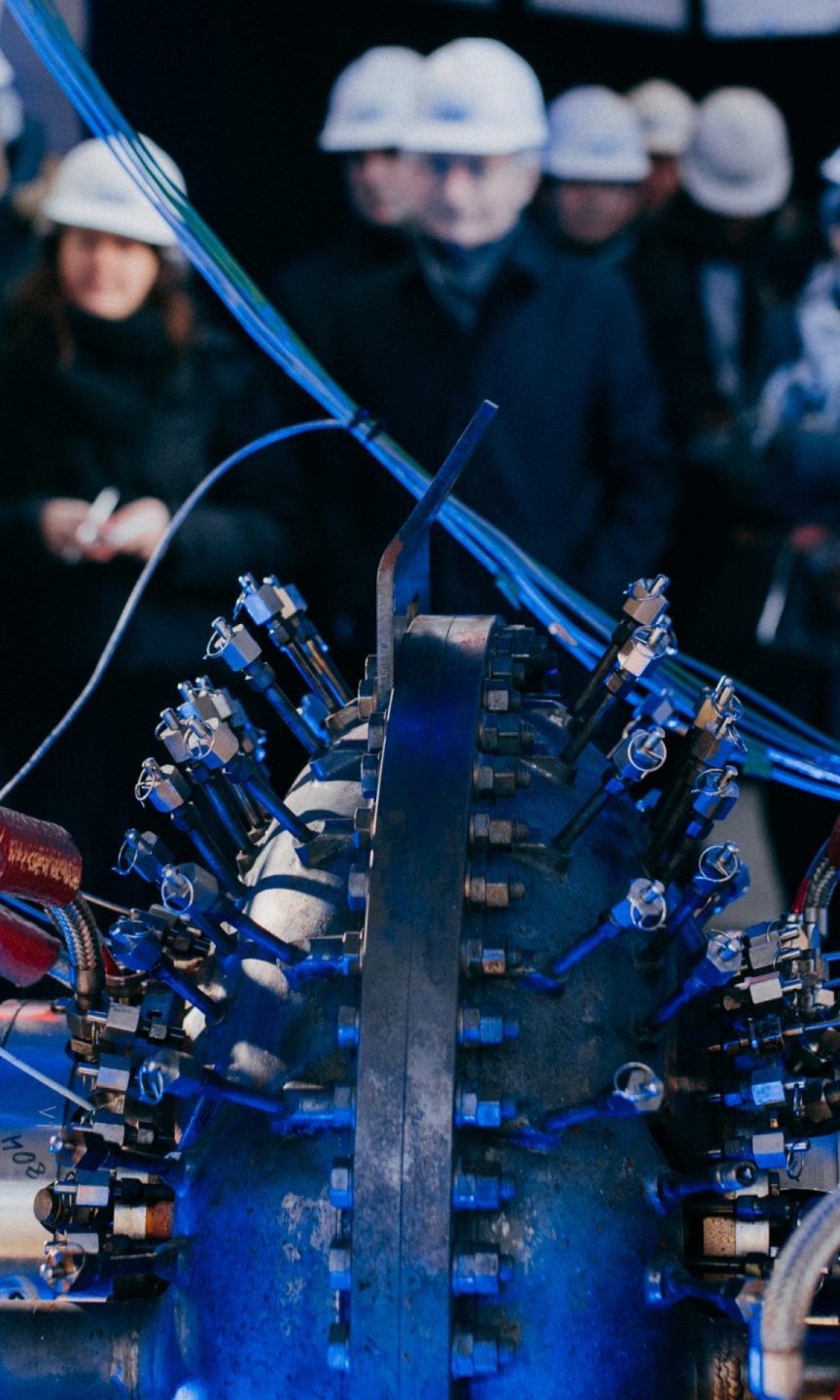
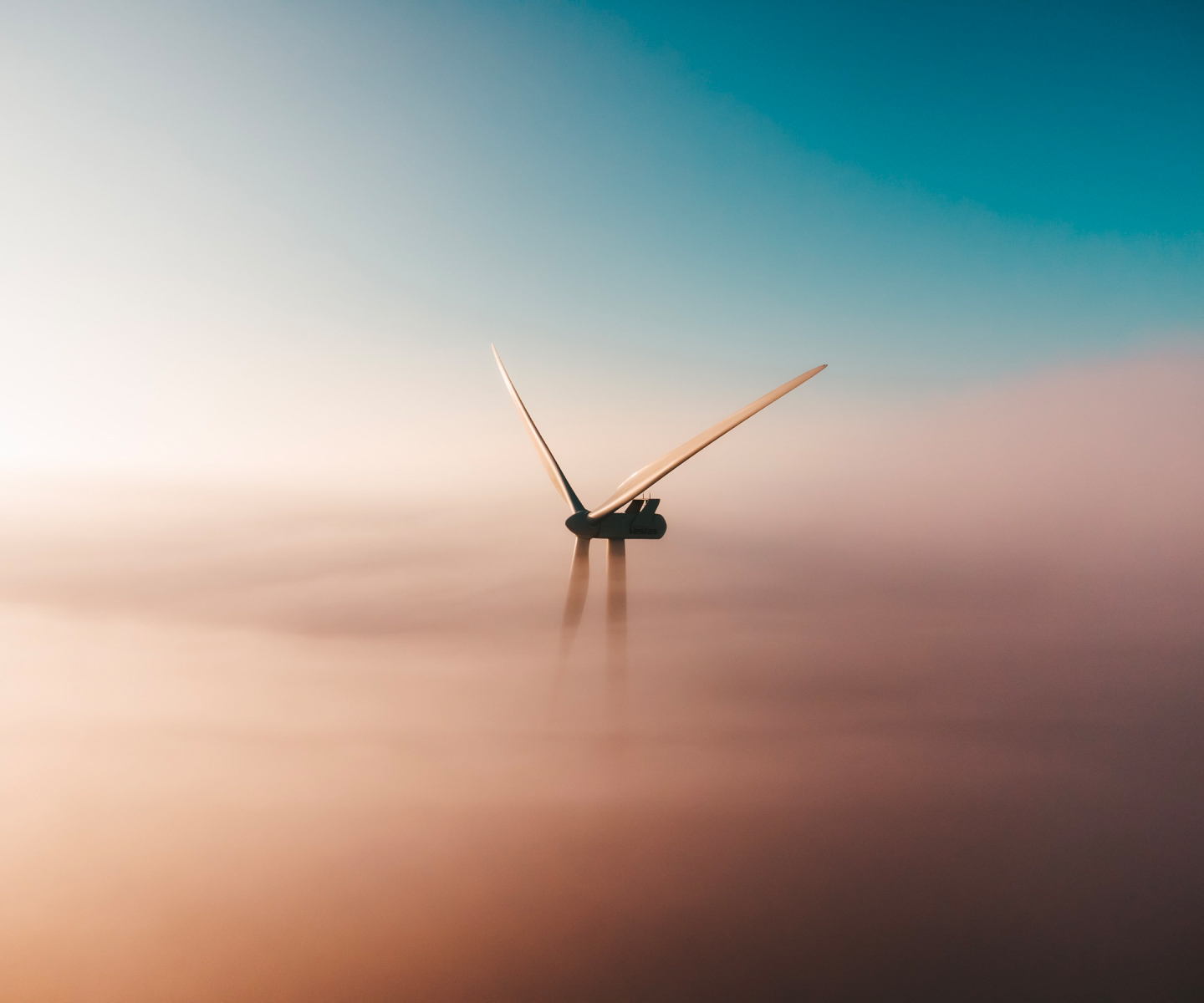
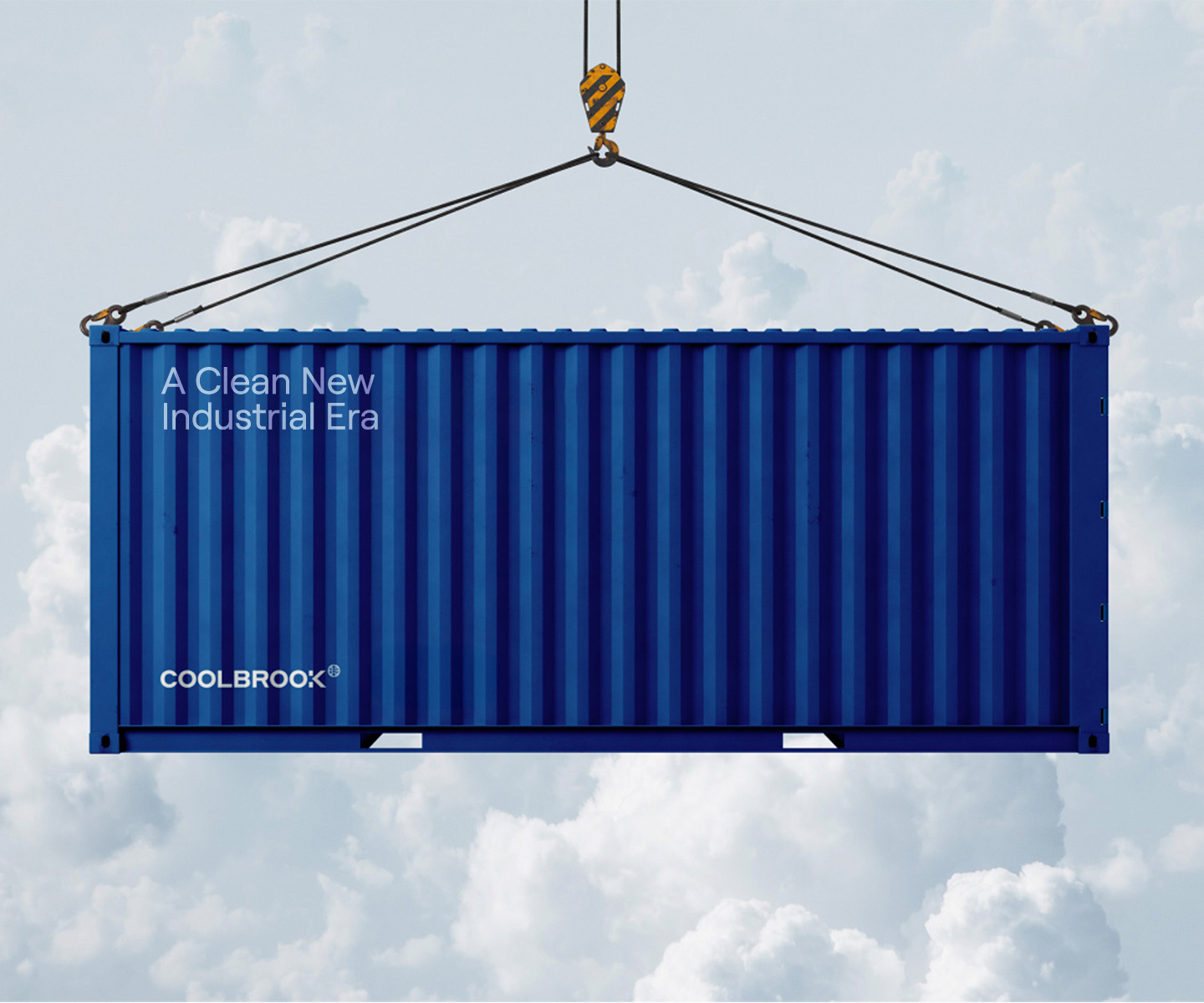
Our Technology
Rocket science and turbomachinery meet chemical engineering
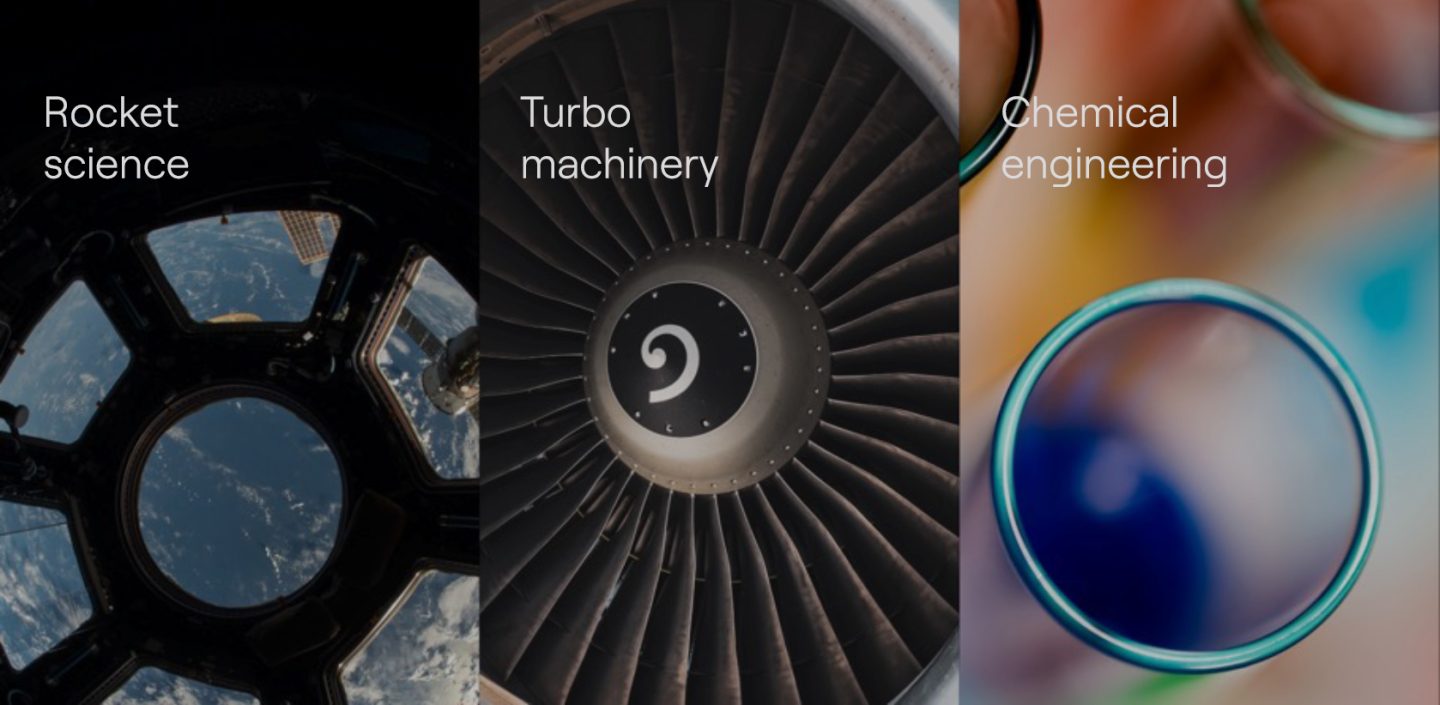
Coolbrook’s game-changing RotoDynamic Technology, a forefront electrification solution, combines the principles of rocket science, turbomachinery and chemical engineering. This revolutionary technology has the potential to reach temperatures of 1700 C degrees and it enables the electrification and decarbonization of high-temperature industrial processes which have been traditionally considered hard-to-abate. This marks a significant advancement in the field of industrial electrification technology.
The technology has two main applications: RotoDynamic HeaterTM (RDH) and RotoDynamic ReactorTM (RDR) which, once deployed at scale, have the potential to cut global industrial CO2 emissions by up to 2.4 Gt or 30%. This accounts for 7% of annual global CO2 emissions.
Coolbrook technology has the potential to be the most significant single technology to reduce industrial CO2 emissions globally.
RotoDynamic TEchnology in Figures
100%
CO2 free olefin production in petrochemical industry
2.4gt
industrial CO2 emission reduction potential annually
30%
reduction in global industrial CO2 emissions
Industrial electrification and decarbonization
Our electrification solutions to decarbonize key industrial processes and reduce CO2 emissions
Coolbrook’s pioneering technologies RotoDynamic Heater™ (RDH) and RotoDynamic Reactor™ (RDR) are at the forefront of the electrification of high-temperature industrial processes. By replacing traditional fossil fuel-based methods with our cutting-edge electrification solutions, we aim to pave the way for a carbon-neutral future in industries that have been historically challenging to decarbonize.
Learn more about our innovative approaches to decarbonize hard-to-abate industries.
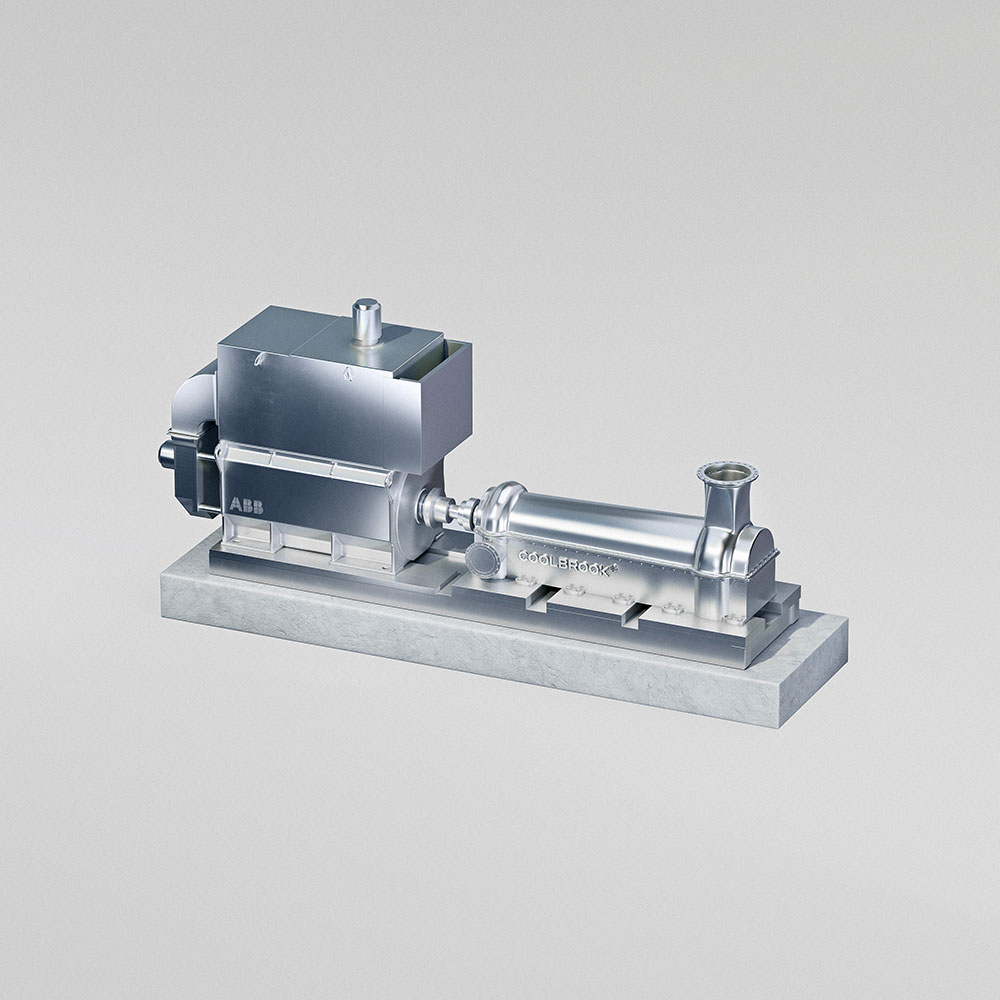
RotoDynamic Heater to replace burning fossil fuels in process heating
RotoDynamic HeaterTM (RDH) to electrify industrial process with potential to heat up to 1,700 °C in all major industry sectors, such as cement, iron, steel, pulp and paper, and chemicals.
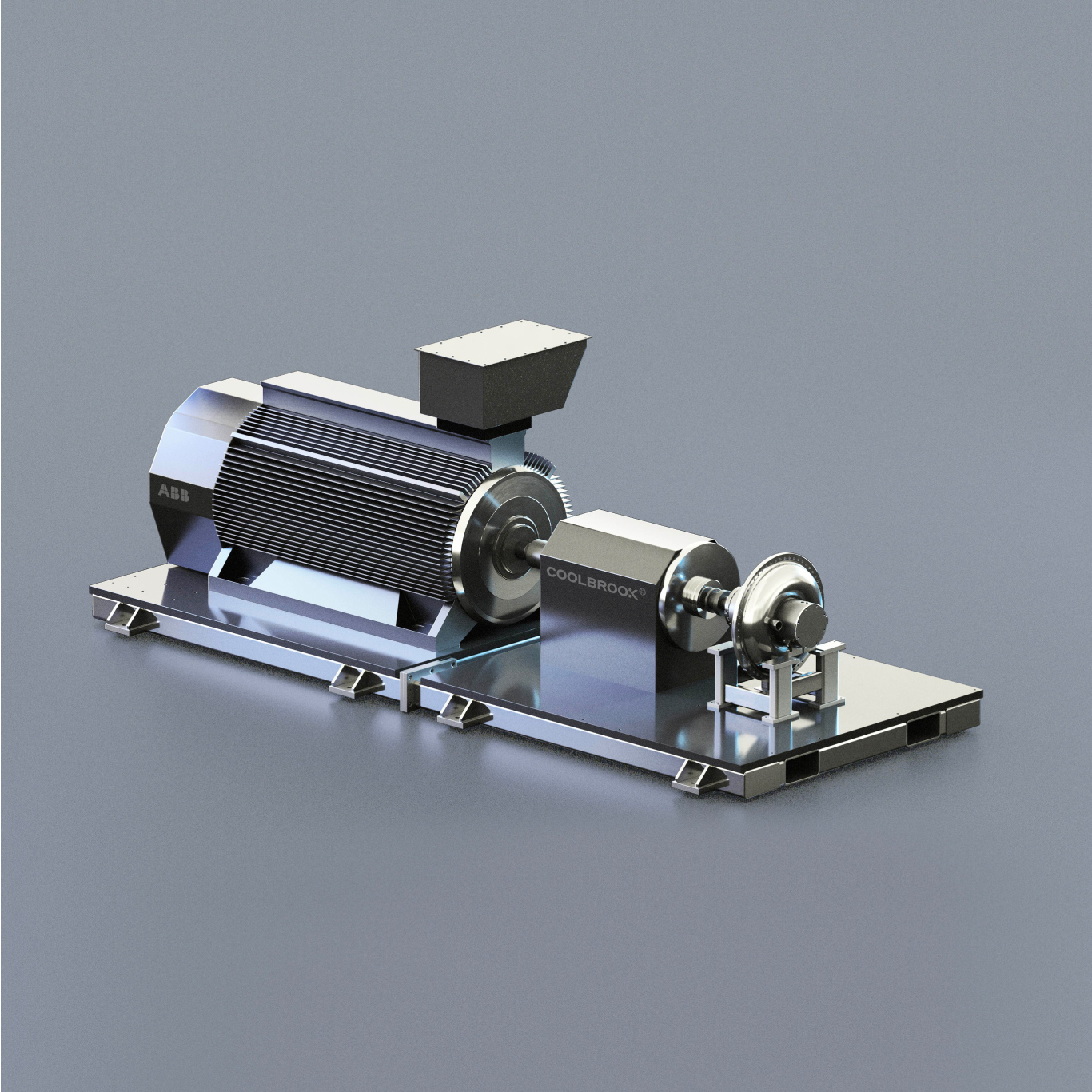
RotoDynamic Reactor cuts 100% of CO2 in steam cracking
RotoDynamic ReactorTM (RDR) to replace fossil-fired steam crackers to reach 100% CO2 free olefin production in petrochemical industry.
RotoDynamic technology is the only electrification technology that can eliminate CO2 emissions from high-temperature industrial processes.
RotoDynamic Technology is in large-scale pilot testing
2021 – 2023
- Demonstrate technology and engage customers in petrochemicals and other key industrial sectors
- Partnering with industrial actors, EPC partners and universities for successful piloting
- Ramp-up of organization
2023 – 2025
- Commercial scale units installed at customer sites:
- RDR connected to ethylene plant
- RDH in selected applications (e.g. steel industry and cement industry)
- Engage technology suppliers to include RDR and RDH in their offering
- Network of partners to secure successful commercial launch
- Strengthen organization and prepare for commercial launch
2025 →
- Commercial deliveries to customers
- RDR and RDH part of electrification technology offering of key suppliers and EPC companies
- World class organization and capabilities to deliver value for all stakeholders
- Continued value-adding partnerships within network of globally leading industry players and decarbonization actors in different sectors
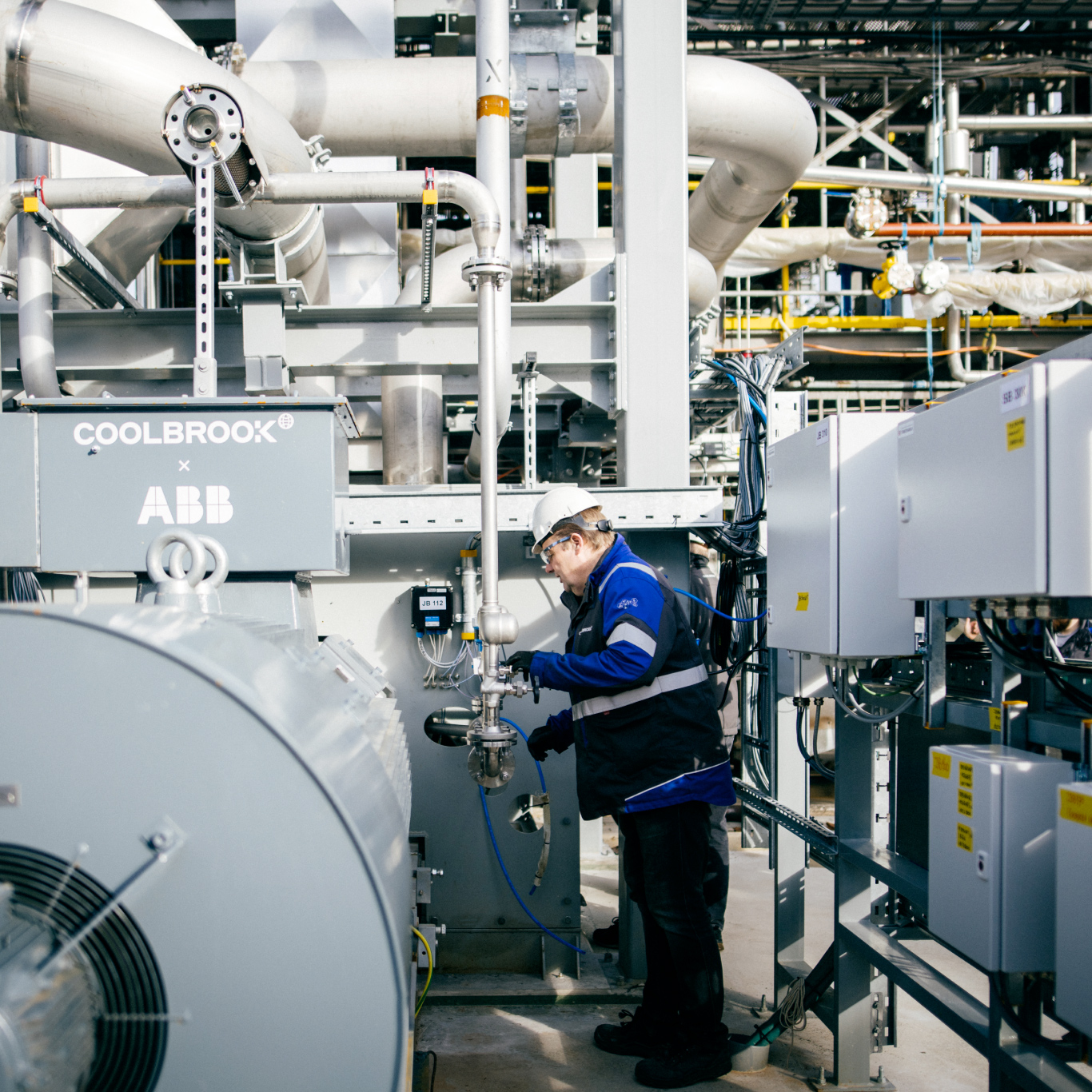
RotoDynamic Technology is pilot tested at large-scale testing unit at Brightlands Chemelot Campus in Geleen, the Netherlands
The main targets of the pilot testing:
- Demonstrate the use of RotoDynamic HeaterTM (RDH) technology for high-temperature industrial process heating with inert gases, such as: air, nitrogen, methane, steam, CO2
- Demonstrate the RotoDynamic ReactorTM (RDR) technology and its reliability for hydrocarbon cracking to stakeholders in the petrochemical industry
- Validate modelling (fluid dynamics) and design parameters and to establish basis for first customer projects
The first phase of the pilot tests was successfully completed in September 2023. The test phase demonstrated RDH technology’s capabilities for industrial use in high-temperature process heating, enabling the technology to move forward to industrial scale projects at customer sites.
In late 2023, Coolbrook has successfully cracked naphtha with the RotoDynamic Reactor, demonstrating electric steam cracking of naphtha and validating the potential of Coolbrook’s RDR Technology to replace traditional fossil fuel-based cracker furnaces with electric RDR units in the petrochemical industry.
Learn more about the end-results that demonstrate this electrification solution’s potential to reduce global industrial CO2 emissions in gigaton scale.
Coolbrook has built a comprehensive partnership ecosystem consisting of leading technology and industrial partners, as well as academic institutions, to develop and launch the technology. Read more about the decarbonization partnerships and how you can participate.
Direct electrification is the superior technology for decarbonizing
Everything that can be electrified, must be electrified
Electrification of industrial processes across industry sectors – including the ones hardest-to-abate – is key to achieving the required emission reductions and to speed up the transition to carbon-zero.
Clean electricity provides a clear pathway towards zero carbon industrial production in an energy and cost-efficient manner. Direct electrification is clearly the superior alternative in all applicable cases due to higher energy efficiency and lower cost.
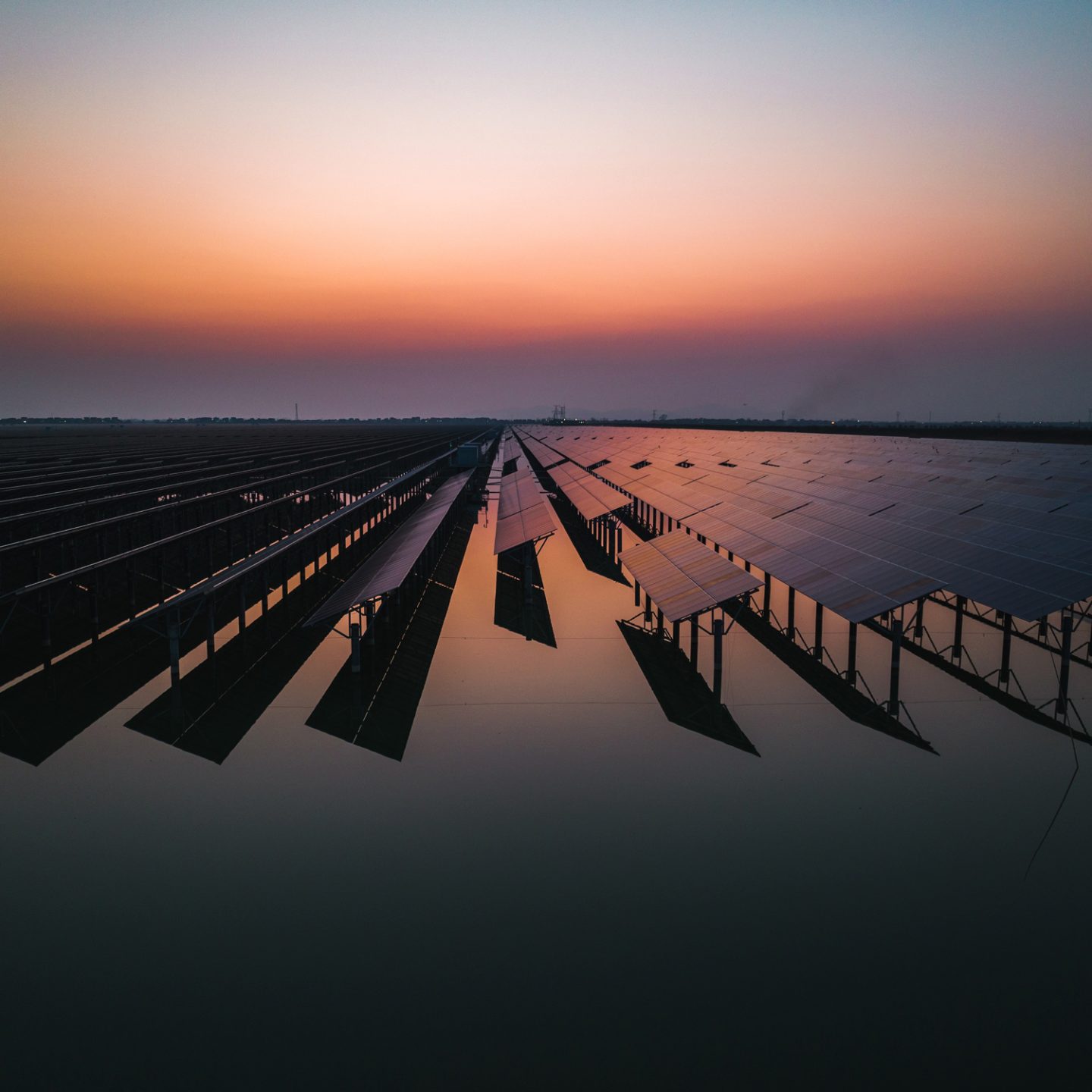
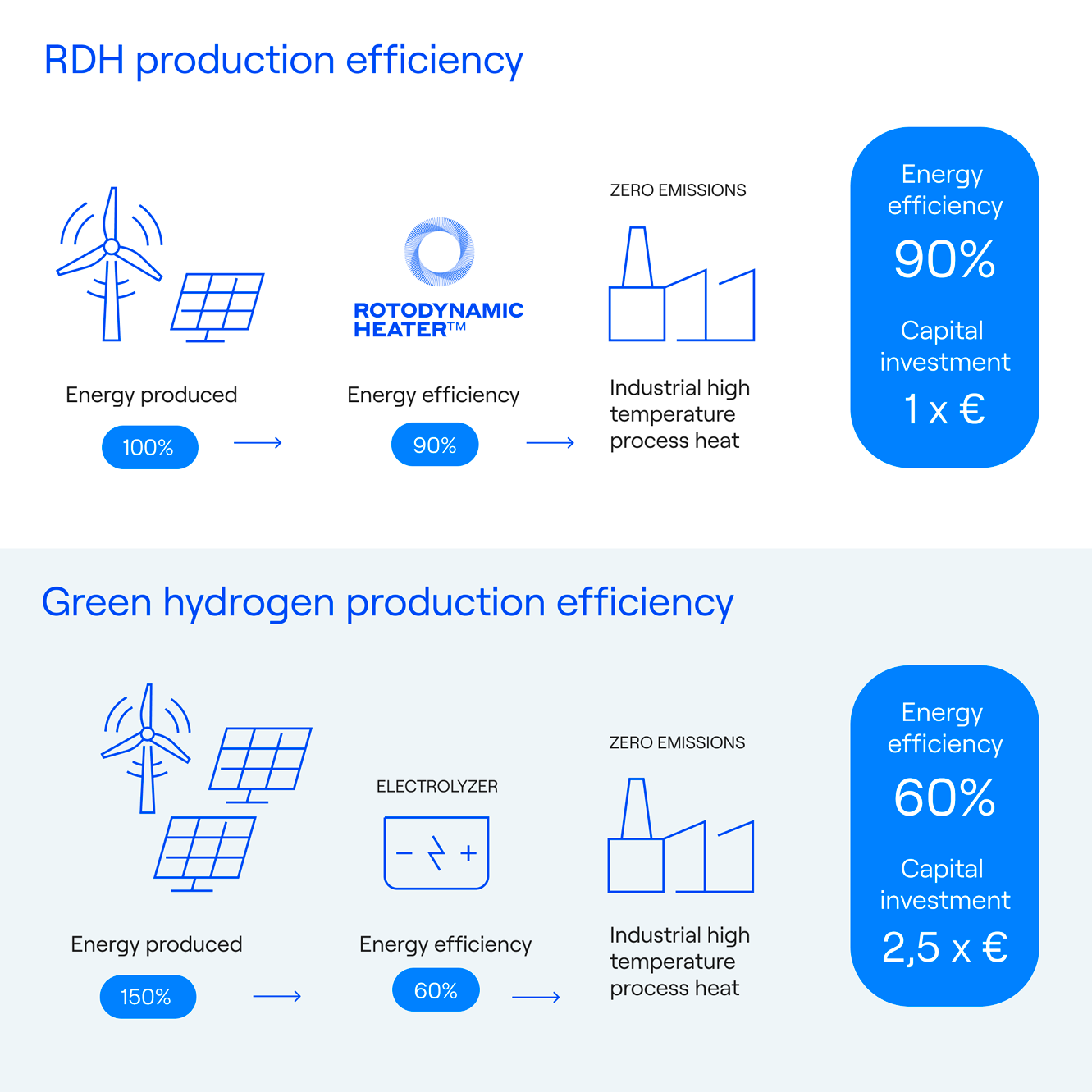
Use case comparison to green hydrogen
Direct electrification is superior for decarbonizing heavy industries.
Cost: approximately 30-60% lower operating costs when using RotoDynamic Heater for process heating over green hydrogen in 20301.
Required infrastructure: widespread use of green hydrogen requires massive investments to H2 infrastructure and electricity networks.
Efficiency: 90% of electricity produced can be used for process heating vs 40-60% in burning of hydrogen.
1 With estimated green hydrogen cost of 2,700 USD / ton in 2030, electricity price 40 USD/MWh and direct electrification pays 10-30% premium for electricity compared to electrolysers