Piloting RotoDynamic Technology: Shaping the Future of Electrification
To develop our technology and broaden our partner network, we are operating a RotoDynamic Technology pilot plant at the Brightlands Chemelot Campus in Geleen, the Netherlands, in the heart of the petrochemical industry.
Coolbrook pilot demonstrates the massive potential of the revolutionary new electrification technology to heavy industries, technology providers and policy makers.
RDH – RotoDynamic Heater – Electrification of high-temperature process heat in the production of cement, steel, iron and chemicals
RotoDynamic HeaterTM (RDHTM) is the only technology in the world able to reach high-temperature heat, up to 1700°C, powered by electricity and without burning fossil fuels. This enables it to replace fossil-fired furnaces and kilns with electrification of industrial processes. Learn more about our innovative approaches to decarbonize the hard-to-abate industries, like steel industry and cement industry.
In 2023, the successfully completed RotoDynamic Technology pilot’s first phase demonstrated RDH technology’s capabilities for industrial use in high-temperature process heating, enabling the technology to move forward to industrial scale projects at customer sites.
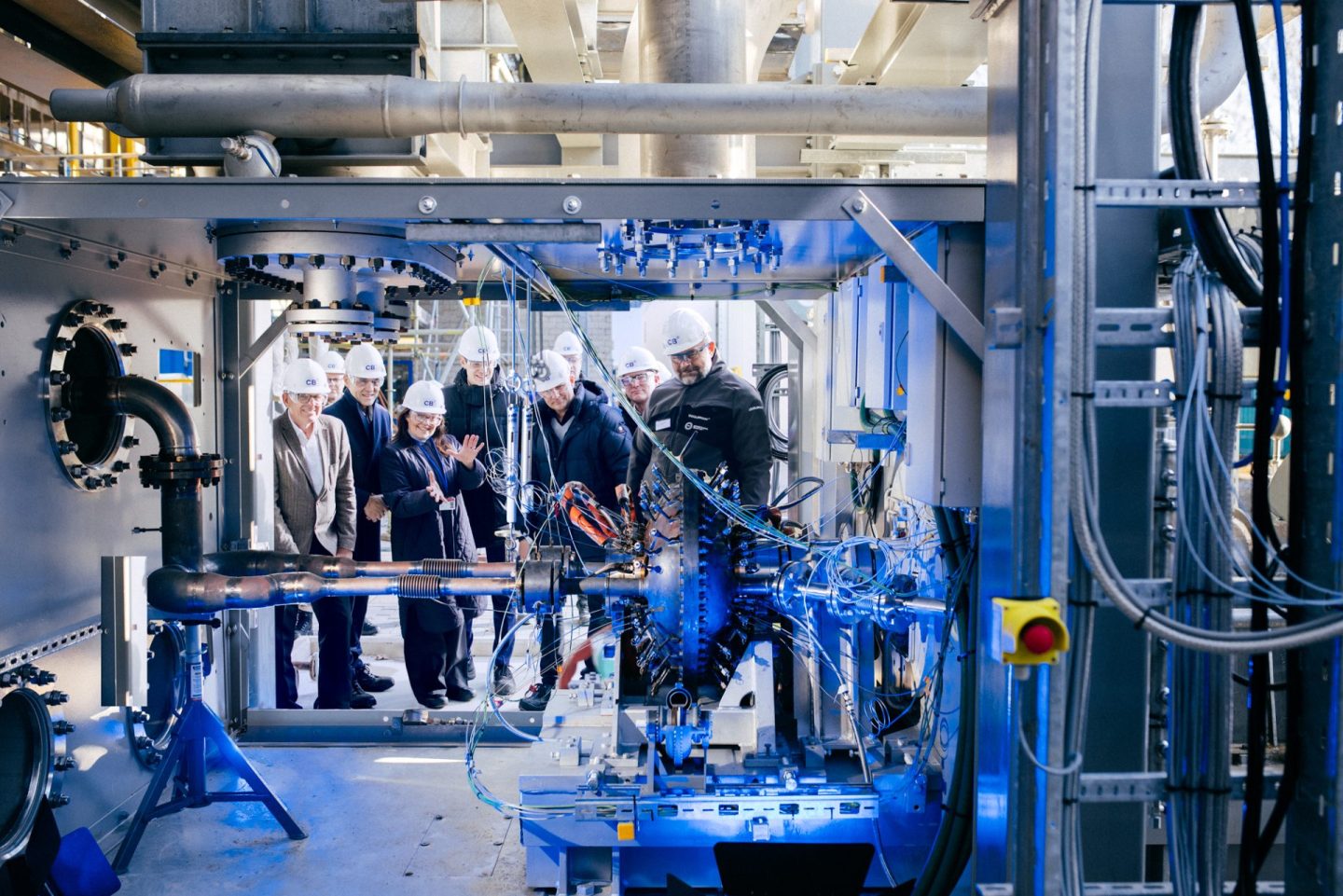
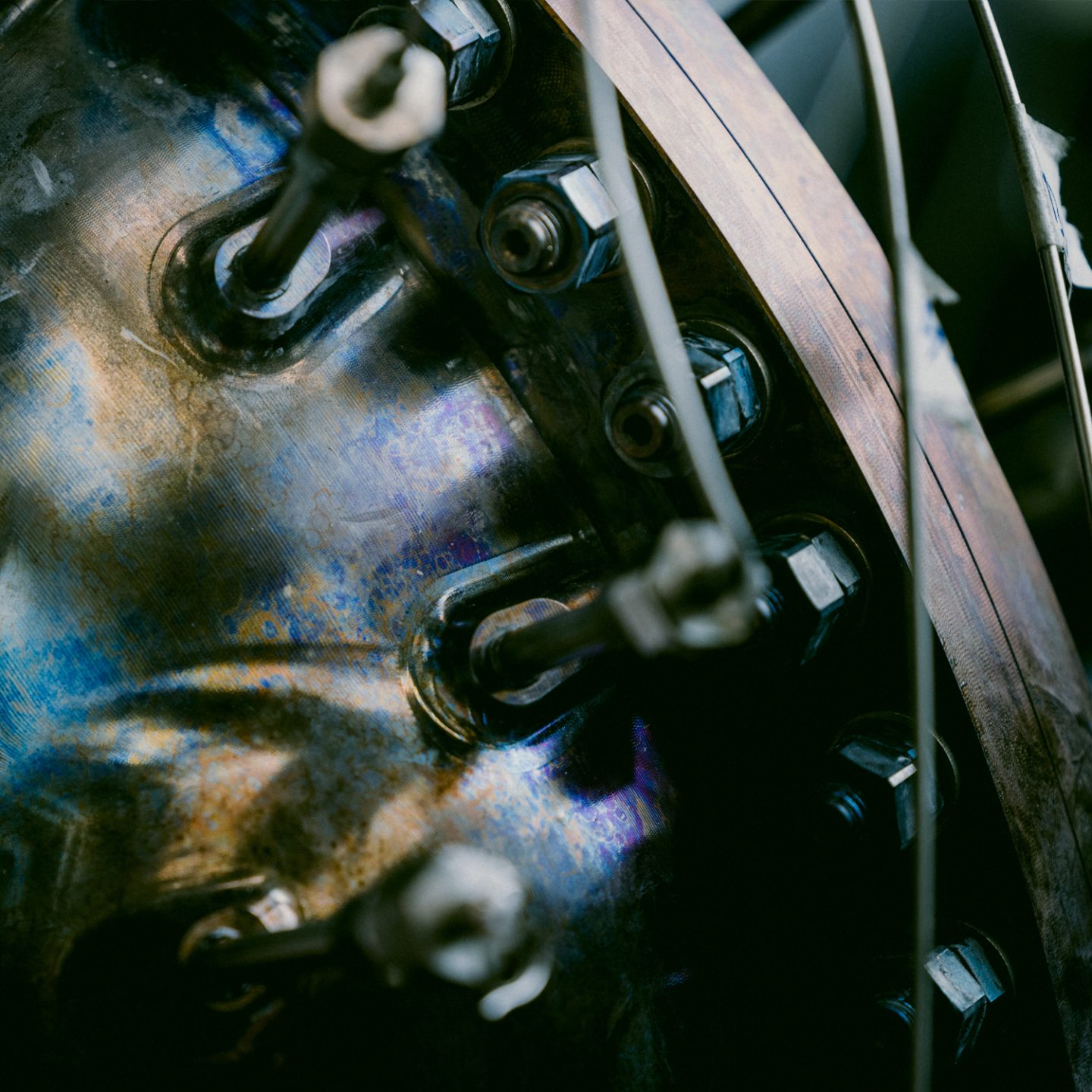
Results of the now completed RDH pilot program
- Validated modelling and design parameters for industrial process heating applications.
- Demonstrated RDH applicability as a reliable source of industrial process heat.
- Tests conducted with inert gases (air, steam and methane)
Industrial heating pilot outcomes
- In 2023, the successfully completed tests demonstrated RDH’s capabilities for industrial use in high-temperature process heating.
- The testing exceeded the temperature of 1000°C, which is above the range of conventional resistive heaters by several hundred degrees. (Read the full press release about the successful pilot for industrial electrification and decarbonization of high-temperature industrial heating.)
- The tests validated Coolbrook’s technical pathway up to 1700°C, covering more than 95% of the temperature range required to cover the EUR 1 trillion industrial heating market.
RDR – RotoDynamic Reactor – electrification of steam cracking in production of petrochemicals
RotoDynamic ReactorTM (RDRTM), using electrification powered by renewable energy, is a technology capable of eliminating 100% of the CO2 emissions created in the steam cracking process, the first and most polluting step in the production of petrochemicals. Furthermore, our RDR technology can increase the yield of high value chemicals, such as ethylene, propylene and butadiene, significantly compared to any other steam cracking technology.
Targets of the RDR steam cracking pilot
- Optimize the cracking process inside the reactor and validate modelling results.
- Test yields and conversion with different feeds, understand the effect of RDR’s process conditions on coking.
Electric steam cracking pilot progress:
- In 2023, successful cracking of naphtha and demonstration of electric steam cracking of naphtha.
- In 2024, test program was expanded to cover additional feedstocks, and to fine-tune and demonstrate the robustness of the technology.
- These tests have validated the potential of RotoDynamic ReactorTM (RDR) Technology to replace traditional fossil fuel-based cracker furnaces with electric RDR units in the petrochemical industry.
- In 2025, the test program will be expanded to cover recycled and sustainable feedstocks
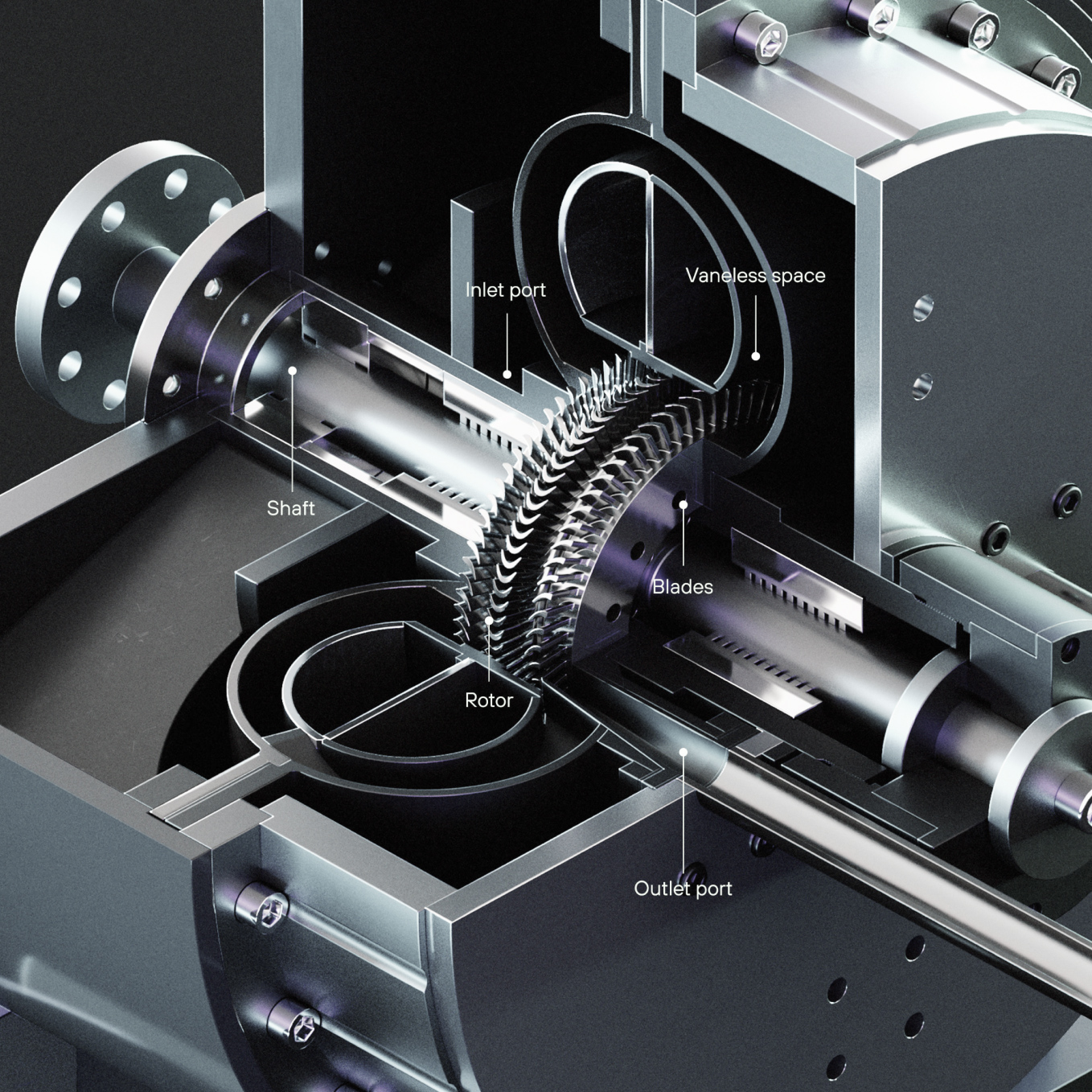
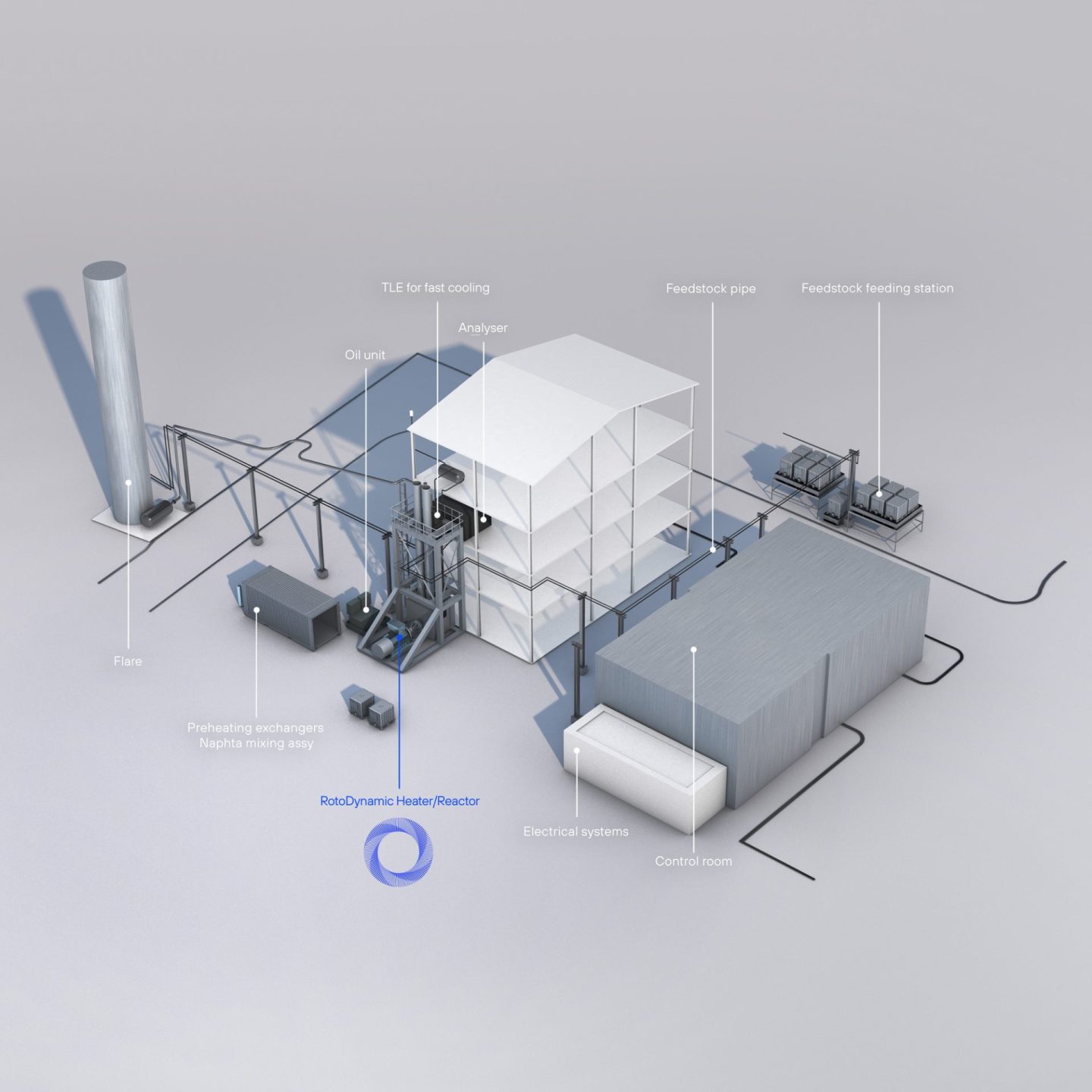
RotoDynamic Technology pilot layout
The pilot unit covers a number of buildings on the Brightlands Chemelot Campus in Geleen, the Netherlands.
Located at the Brightlands Chemelot Campus in Geleen, Netherlands
The Brightlands Chemelot Campus boosts innovation and business growth by giving tenants access to talent knowledge and infrastructure and entrepreneurship.
With over 3,300 of the world’s leading experts in engineering, modelling, operations and maintenance, the Chemelot Campus is the best possible place to test and develop our RotoDynamic technology and collaborate with our partner network.
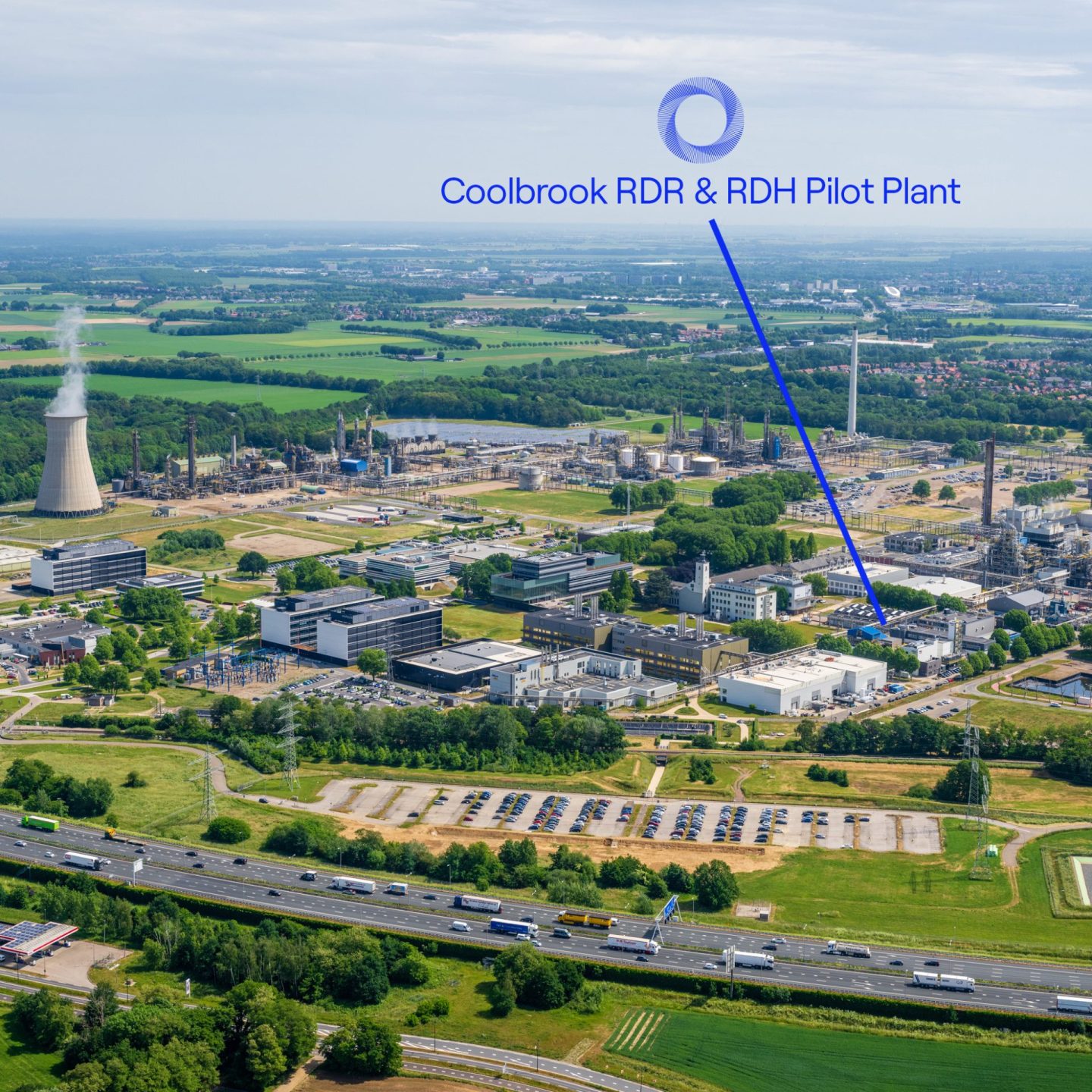
OUR Rotodynamic TECHNOLOGY CAN CUT OVER 30% OF THE WORLD’S INDUSTRIAL CO2 EMISSIONS ANNUALLY
500
Mt
estimated reduction potential in chemicals & petrochemicals industries
600
Mt
estimated reduction potential in iron & steel industries
1000
Mt
estimated reduction potential in cement industries
300
Mt
estimated reduction potential in other industries
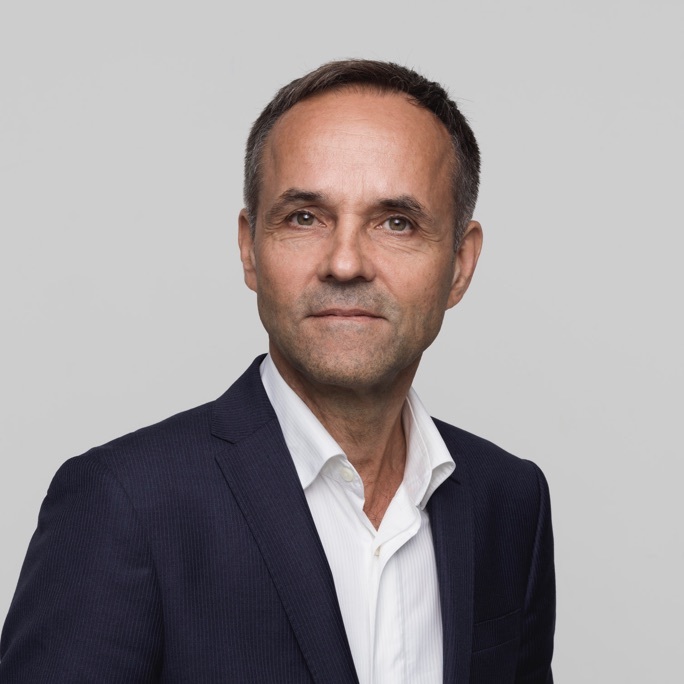
Coolbrook has set out to build a committed and comprehensive ecosystem around RDR and RDH technology to commercialize it as soon as possible. Together with our partners in industry, academia, the public sector and key decision-makers, we can roll out this revolutionary technology and achieve significant emission reductions in the most energy and CO2 intensive industrial processes, which until now have been considered impossible to electrify.
Ilpo Kuokkanen
Founder, Member of the Board of Directors, Coolbrook