Leading decarbonization solution for the most polluting industrial processes
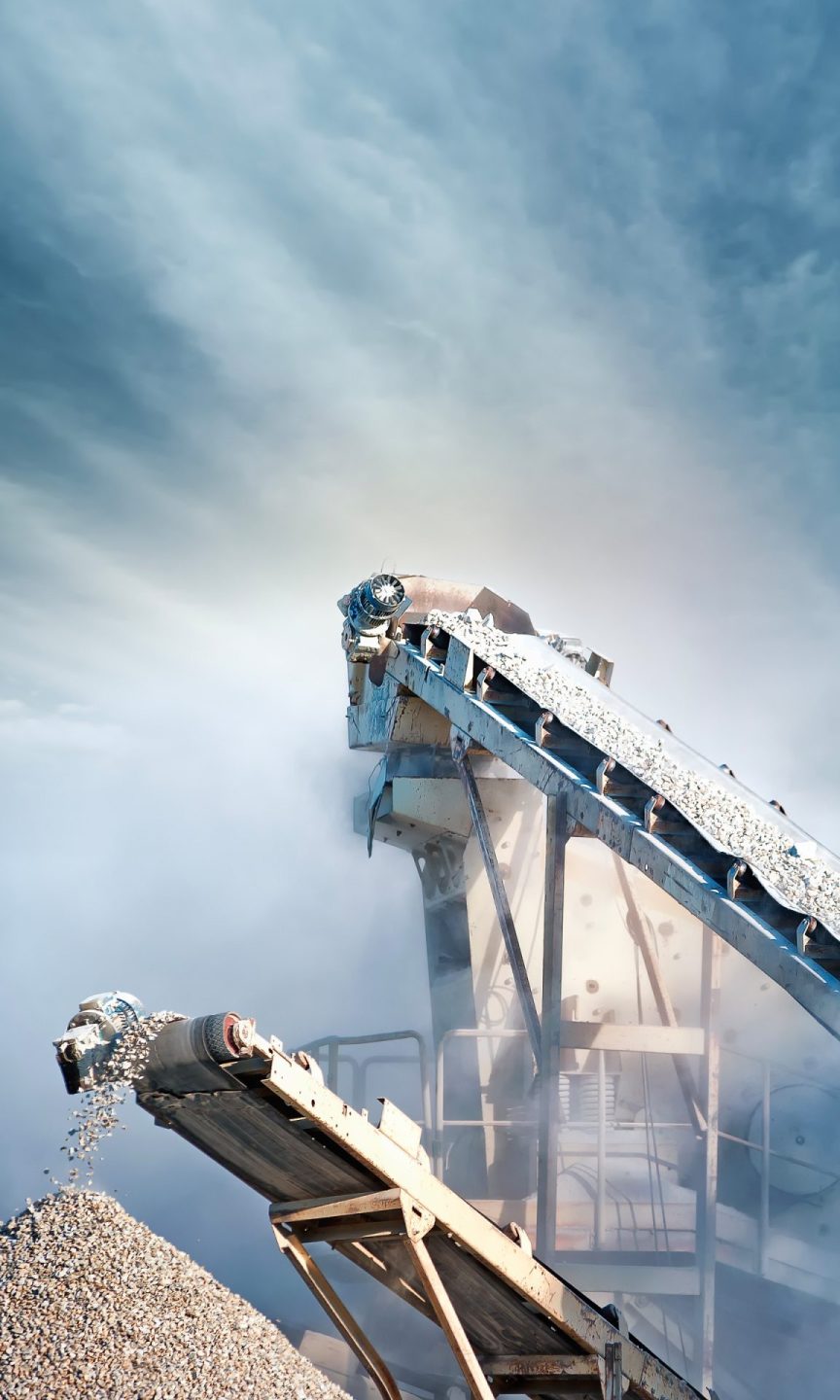
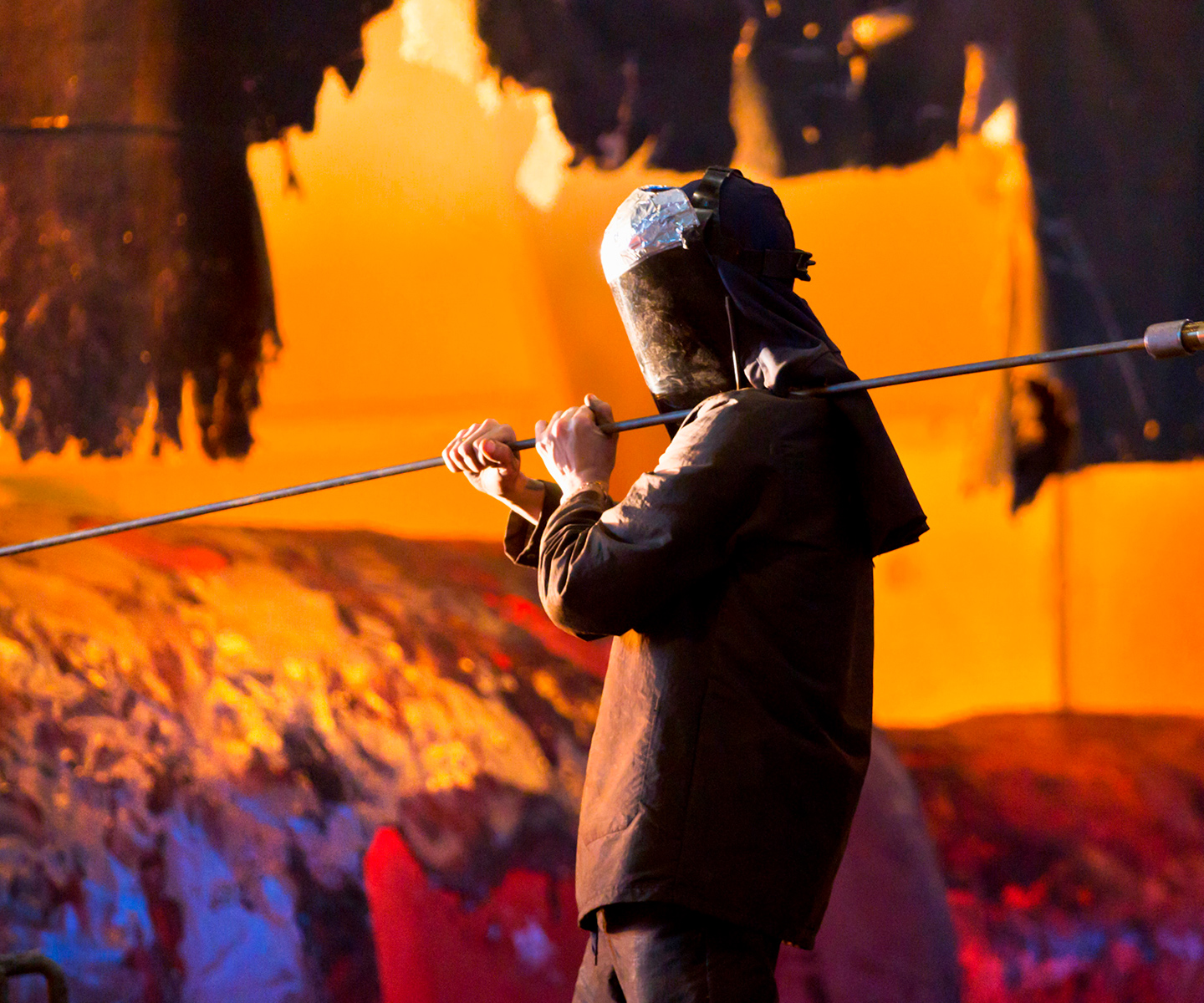
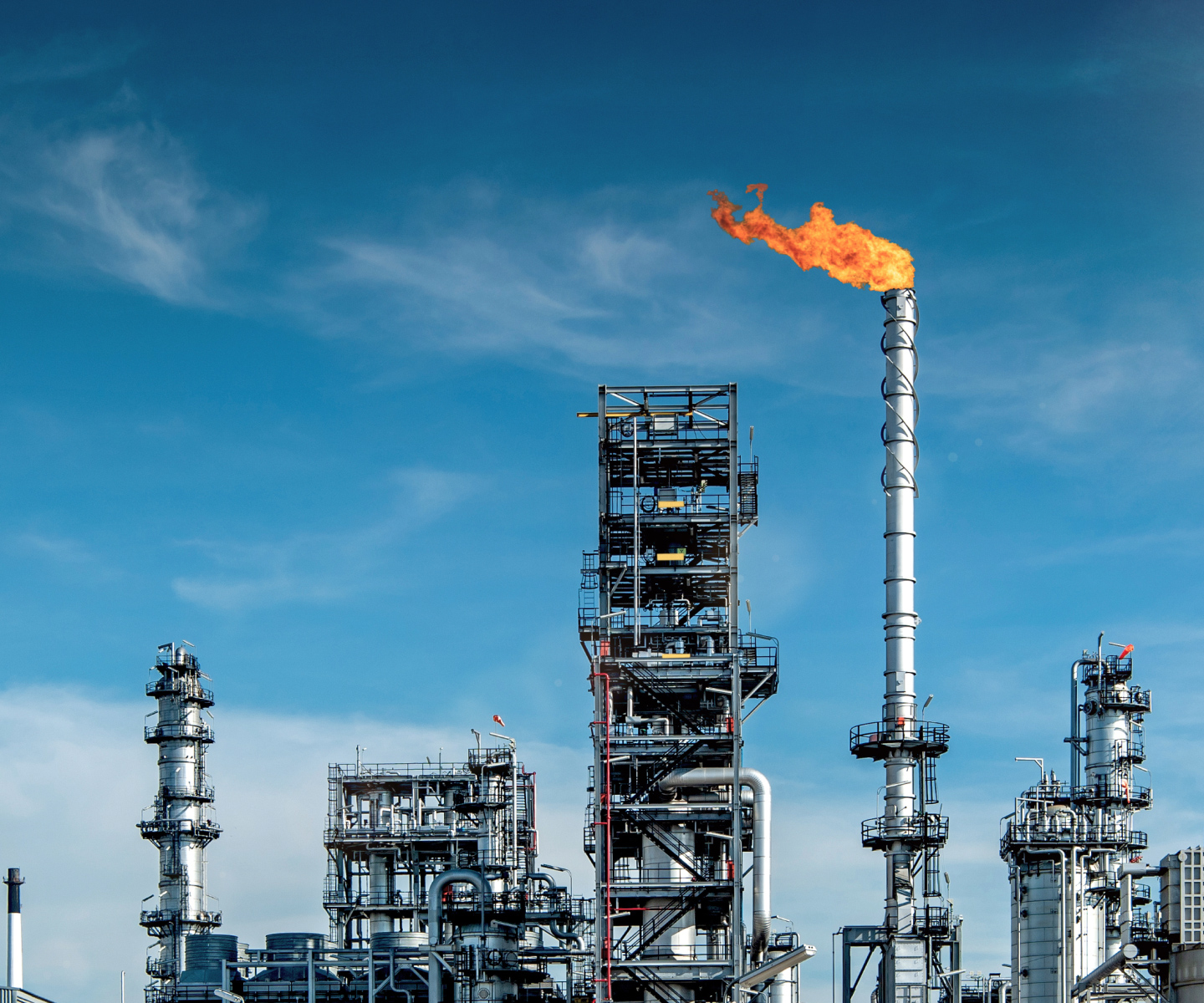
Decarbonization
Clean industrial electrification: A leap in decarbonization technology
Our game-changing RotoDynamic HeaterTM (RDH) and RotoDynamic ReactorTM (RDR) are the only solutions for electrifying and decarbonizing the traditionally hard-to-abate, most CO2-heavy high-temperature industrial processes, including the production of steel, iron, cement, and chemicals and petrochemicals.
Chemicals and petrochemicals, iron and steel, and cement industry account for over 50% of industrial energy use and for 2/3 of industrial CO2 emissions. Coolbrook’s decarbonization technology has the potential to cut industrial CO2 emissions with up to 30%, %, making it a key decarbonization solution for these industries.
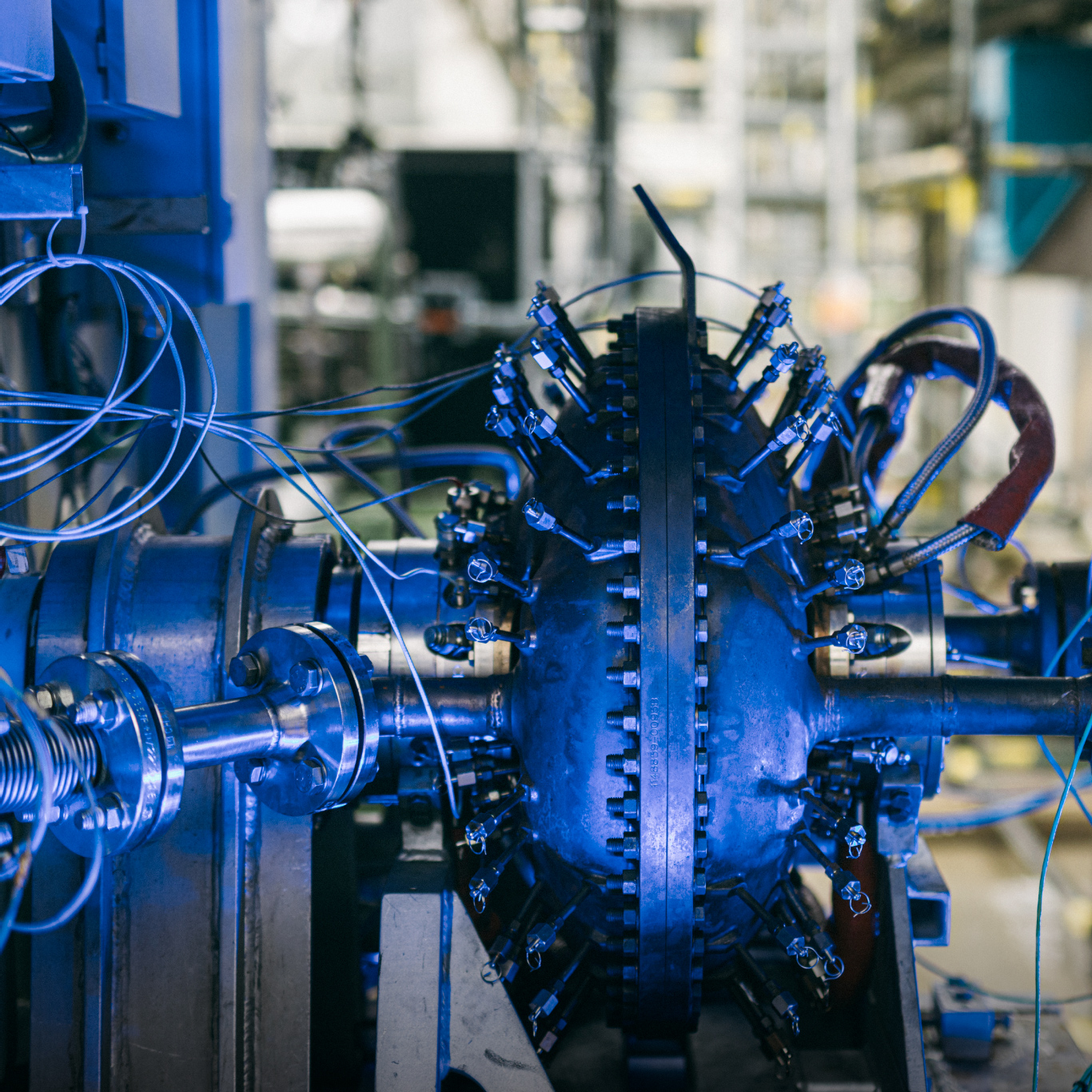
The only electrification technology capable of reducing total industrial CO2 emissions by over 2 Gt or 30%
RotoDynamic Technology is the only electric technology capable of reducing total industrial CO2 emissions by up to 2.4 Gt or 30% – accounting for an annual reduction of 7% in total global CO2 emissions.
We have teamed up with the world’s leading electrification technology partners and industrial customers to roll-out the decarbonization technology at scale by the mid 2020’s.
Hard-to-abate is now possible-to-abate
Decarbonization technology for heavy industry
It’s long been thought that industrial processes like the production of steel, iron, cement and petrochemicals, and other chemicals are difficult – if not impossible – to decarbonise. Our RotoDynamic decarbonization technology is the only electric solution in the world capable of cutting up to 30% – or 2.4 billion tons – of global industrial CO2 emissions annually.
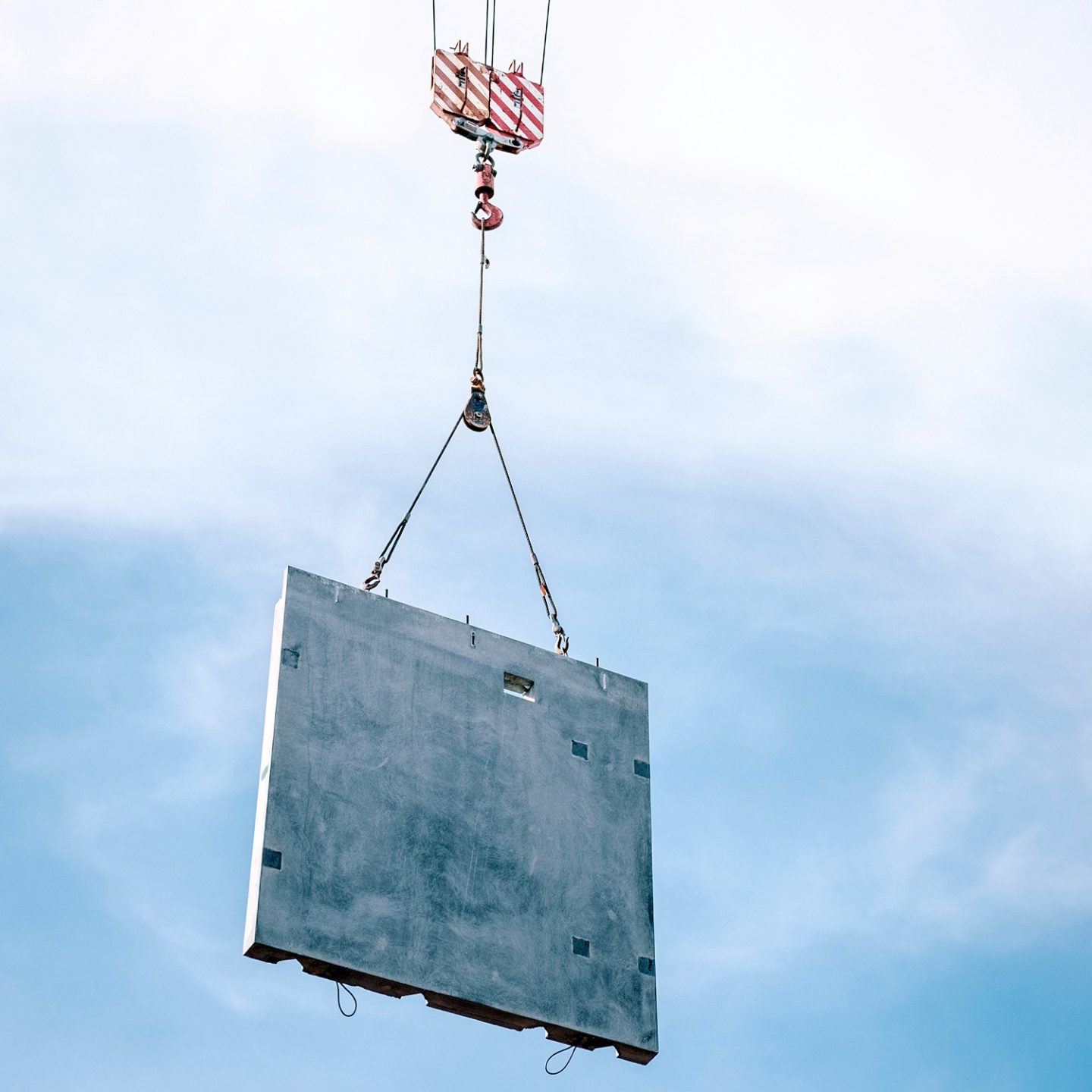
Cement industry
Our technology can cut 1,000 million tons of CO2 in cement production per year globally.
RotoDynamic Technology can be used for example in pre-heating for clinker production and replacing existing fossil-fired kilns with heating by RotoDynamic Heater.
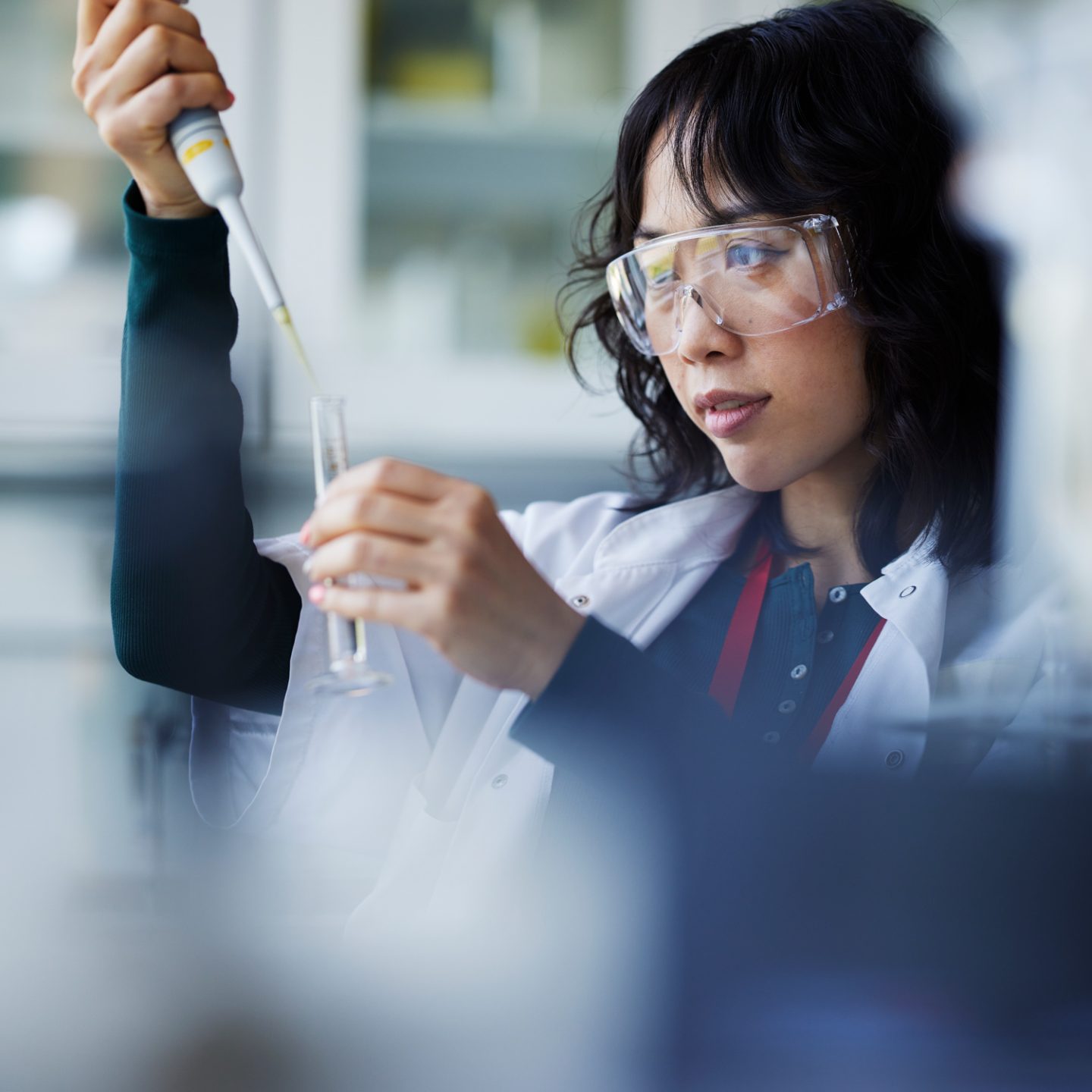
Petrochemical industry
RotoDynamic Reactor cuts 100% of CO2 emissions from steam cracking through electrification.
The technology is also suitable for H2 and methanol production. Together, RotoDynamic Heater and RotoDynamic Reactor technologies can cut 500 Mt of CO2 emissions globally in petrochemicals industry.

Steel and iron industry
In iron and steel industries, RotoDynamic Technology can cut 600 Mt of global CO2 emissions annually.
Use cases for the RotoDynamic Heater range from pre-heating of air to blast furnace, provisioning of heat for H2 based reduction process to heating for hot rolling and casting, coking, sintering.
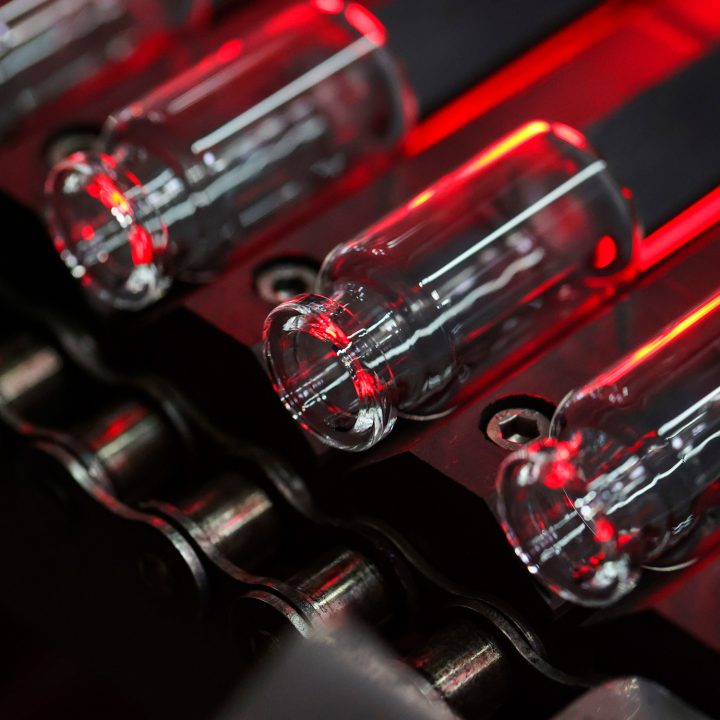
Other industries
Our technology can cut 300 Mt of CO2 in other industries, with use cases in e.g. melting of glass, heating for aluminium oxide production, end of life treatment of waste and residues, and more.
OUR RDR AND RDH TECHNOLOGY CAN CUT OVER 30% OF THE WORLD’S INDUSTRIAL CO2 EMISSIONS ANNUALLY
500
Mt
estimated reduction potential in chemicals & petrochemicals industries
600
Mt
estimated reduction potential in iron & steel industries
1000
Mt
estimated reduction potential in cement industries
300
Mt
estimated reduction potential in other industries