Industrial Process Heating: Replacing Fossil Fuels with RotoDynamic Heater
Meet RotoDynamic Heater™, the world’s only electric technology capable of using clean electrification to reach the extremely high temperature heat needed in the world’s most polluting industrial processes, like the production of iron and steel, cement, and chemicals. Our technology is the solution to decarbonize industrial heating processes, with potential to heat up to 1700 °C.
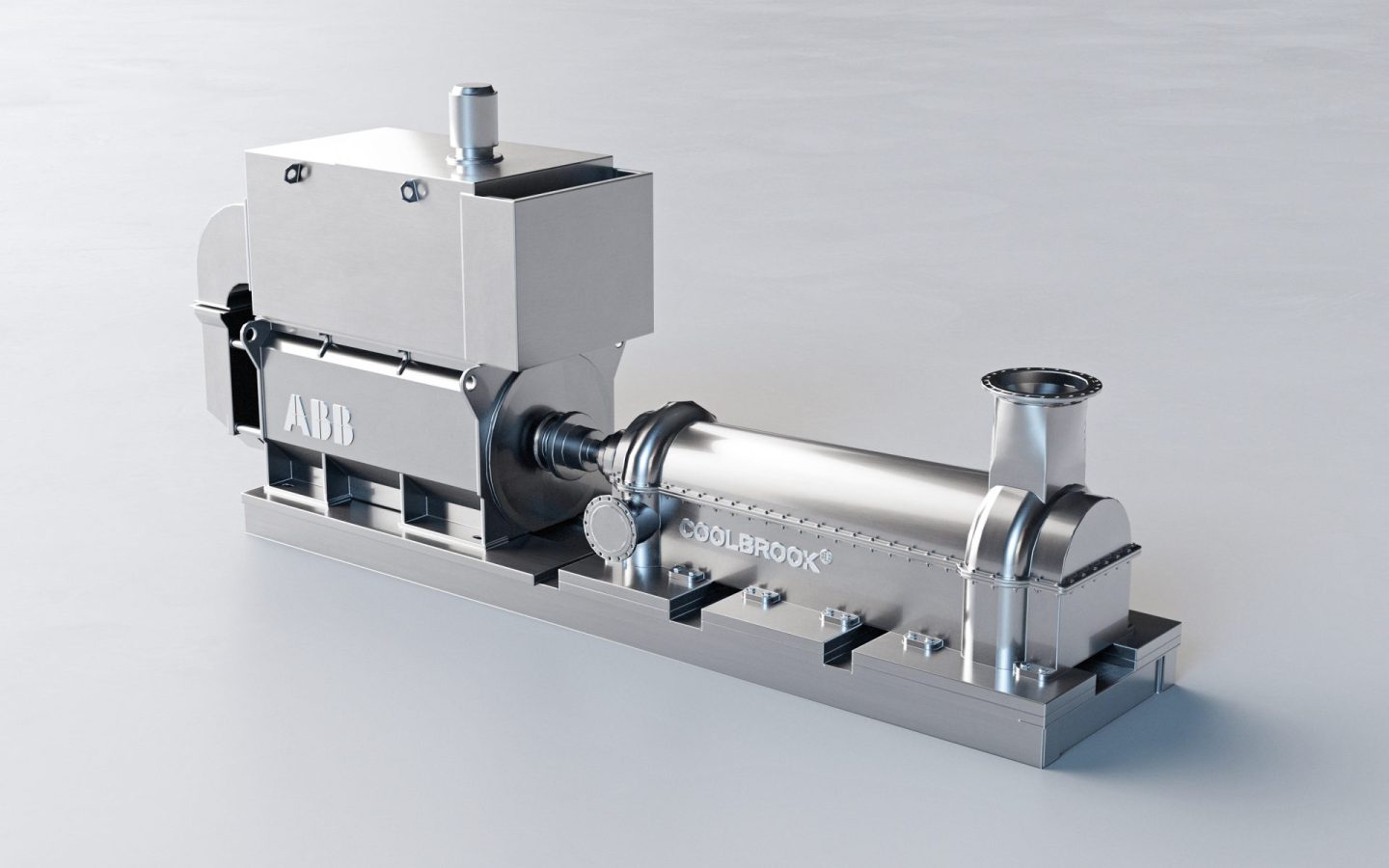
The Solution
Welcome to the electric era in industrial process heating
Heavy industry makes up 25% of global CO2 emissions – a number that has only risen in recent years. Most of those emissions come from the burning of fossil fuels during industrial process heating.
Our RotoDynamic Heater™ (RDH), ), a revolutionary technology for heat electrification, can reduce global CO2 emissions with up to 30% by replacing the fossil fuels used in the most pollution-heavy part of industrial processes with electricity from clean, renewable energy. That means our technology has the potential to cut 7% of global CO2 emissions annually.
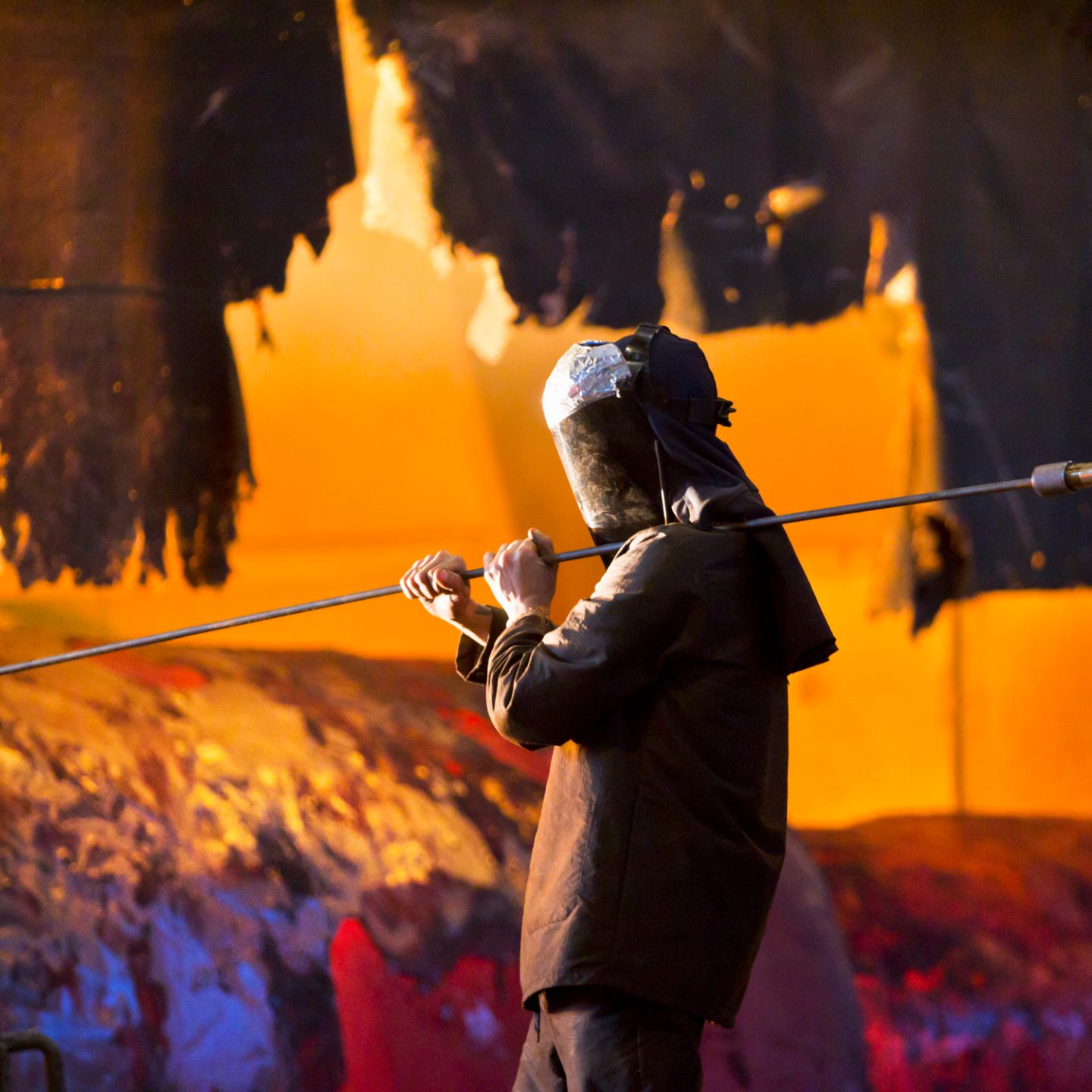
Conventional fossil-fired furnaces and kilns compared to electrification with RDH
In conventional industrial processes the process heat is produced typically through burning of fossil fuels such as coal, natural gas or oil.
RotoDynamic Heater (RDH) is the only heat electrification technology to decarbonize industrial heating processes up to 1700°C without burning fossil fuels. In RDH, air, nitrogen and process gases are heated to high temperatures and the heated gas is used outside the heater to replace the burning of fossil fuels in process heating.
It’s the only electric technology that can replace fossil-fired furnaces and kilns with electrification of heat in industrial processes.
Advantages
Key advantages of RotoDynamic Heater
With unprecedented benefits like the ability to replace fossil-fuels with clean electrification, RDH is the technology of choice for the heavy industrial production of steel, iron, cement and chemicals.
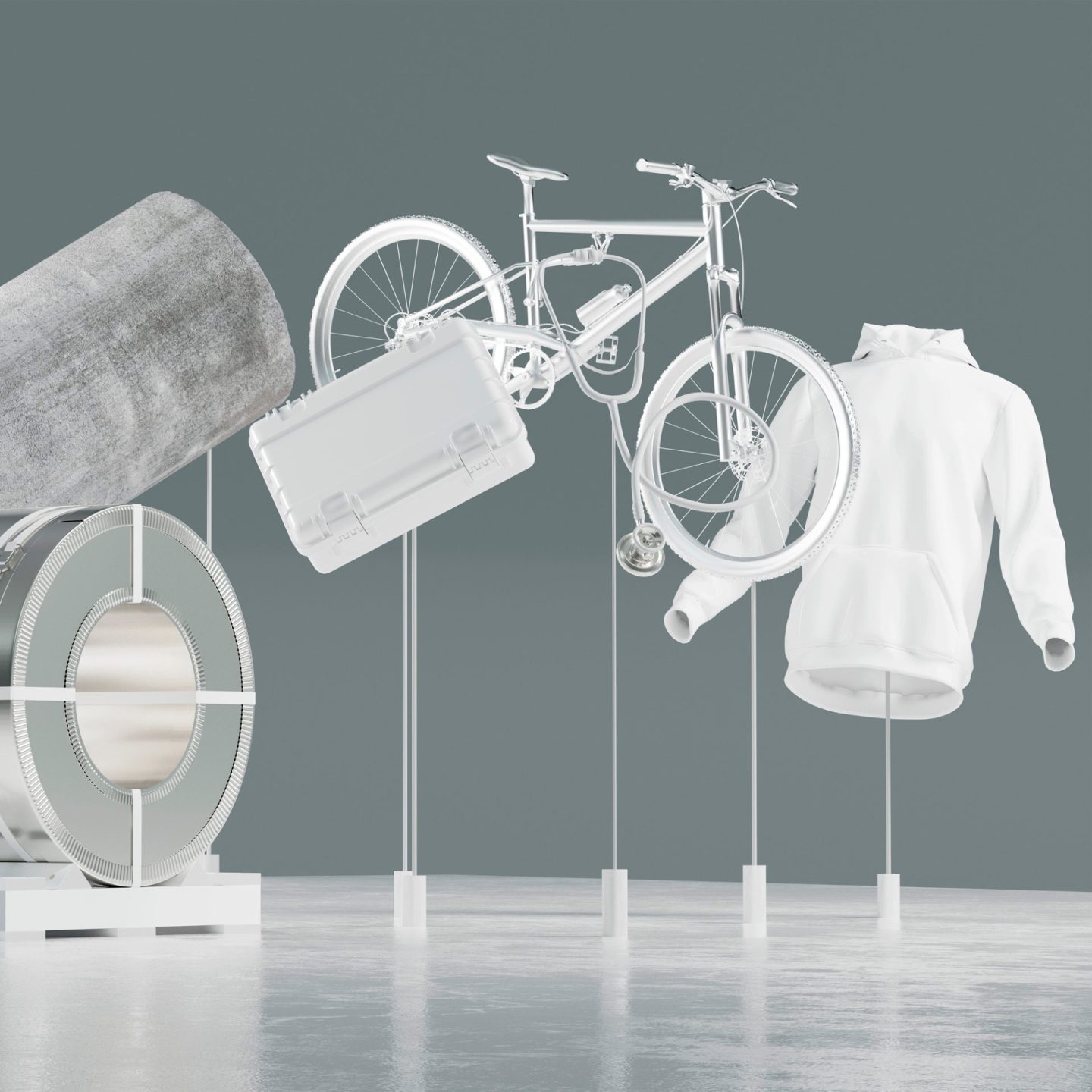
Benefits of RotoDynamic Heater
Application: Electrically driven heater to replace fossil fuel burning in high temperature processes
Tech Features: Possibility to heat gases up to ~1,700 ℃ compared to ~600 ℃ in competing electric alternatives
Benefits:
- Zero CO2, NOx and SOx emissions
- High energy efficiency (in excess of 90%)
- Compact equipment size and possibility to retrofit to existing industrial facilities
- Competitive CAPEX and OPEX
CO2 emission reduction potential 2+ Gt/a globally
Outcome: The products and materials produced with Coolbrook technology carry a substantially lighter CO2 footprint.
Timeline to production
Ready for commercial launch at scale in 2025
This game-changing electrification technology already exists today and a large and growing number of global industrial partners have already expressed great interest in using it to cut CO2 emissions and meet crucial climate targets. Coolbrook’s RotoDynamic technology is currently being piloted, and tests on RotoDynamic Heater have been completed, and testing of the RotoDynamic Reactor is ongoing. The technology can be retrofitted to existing production plants and is expected to be ready for commercial scale use in 2025.
In 2023, the successfully completed first test phase demonstrated RDH technology’s capabilities for industrial use in high-temperature process heating, enabling the technology to move forward to industrial scale projects at customer sites. The pilot testing has reached the level of 1000 °C, which already exceeds the temperature range of conventional resistive heaters by several hundred degrees.
The tests have also validated Coolbrook’s technical pathway up to 1700°C, covering more than 95% of the temperature range required to cover the EUR 1 trillion industrial heating market.
Coolbrook expects to deploy the technology in industrial scale projects at customer sites, aimed to be operational in 2024, while full commercial deployment is expected to start around 2025.
2021 – 2023
- Demonstrate RotoDynamic technology and engage customers in petrochemicals and other key industrial sectors
- Partnering with industrial actors, EPC partners and universities for successful piloting
- Ramp-up of organization
2023 – 2025
- Commercial scale units installed at customer sites:
- RDR connected to ethylene plant
- RDH in selected applications (e.g. steel industry and cement industry)
- Engage technology suppliers to include RDR and RDH in their offering
- Network of partners to secure successful commercial launch
- Strengthen organization and validate key assumptions for commercial launch
2025 →
- Commercial deliveries to customers
- RDR and RDH part of technology offering of key suppliers and EPC companies
- World class organization and capabilities to deliver value for all stakeholders
- Continued value-adding partnerships within network of globally leading industry players and decarbonization actors in different sectors
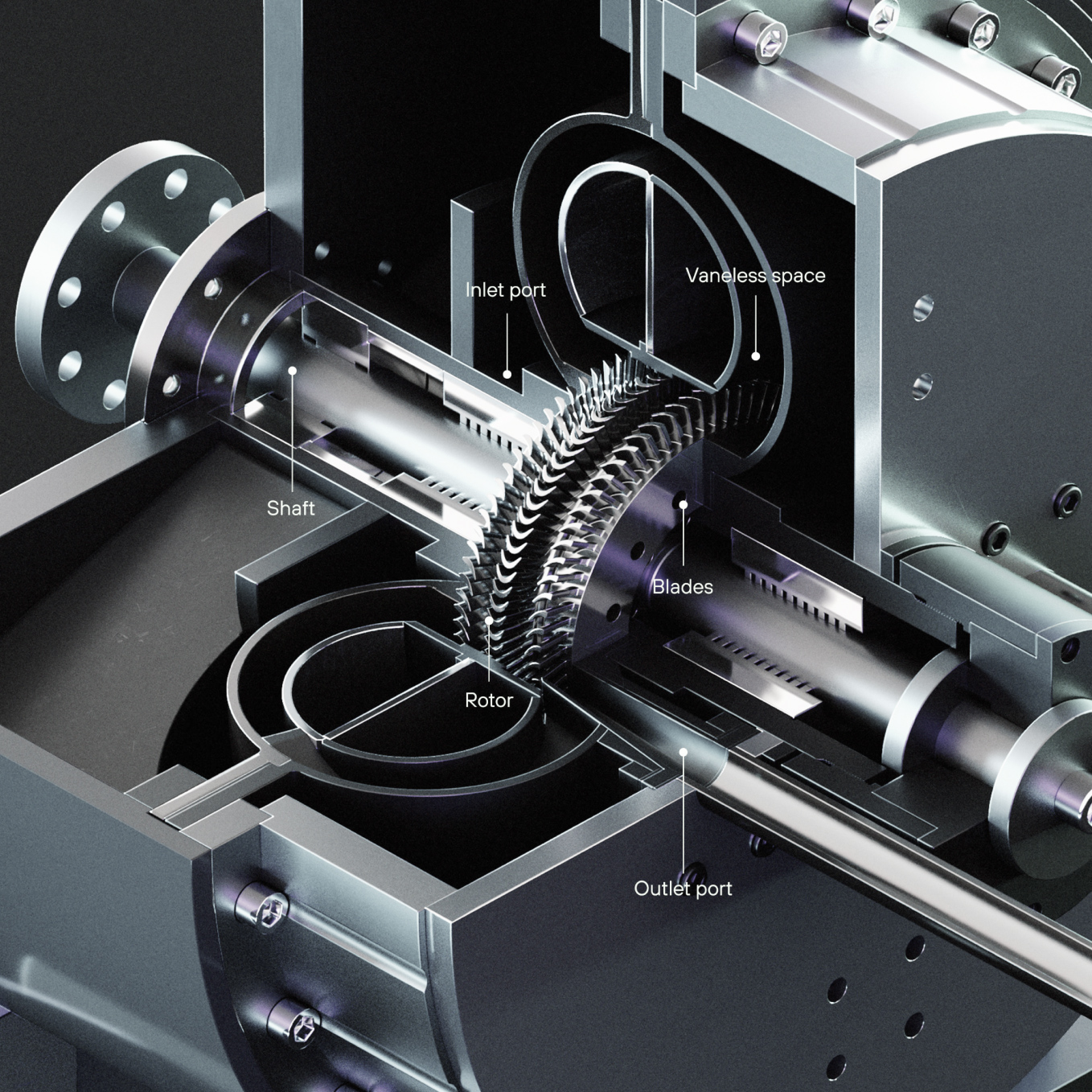
Electrifying High-Temperature Processes with RotoDynamic Heater
RotoDynamic Heater brings together space science, turbomachinery and chemical engineering. With aerodynamic action achieved through a rotating blade flow, RDH can replace conventional fossil-fired furnaces and kilns in industrial heating processes by directly imparting the shaft’s mechanical energy to the heated gas to provide process heat for the production of steel, cement, hydrogen and other chemicals. Electric motor drives the rotors and air, nitrogen or process gases are heated to extremely high temperatures.
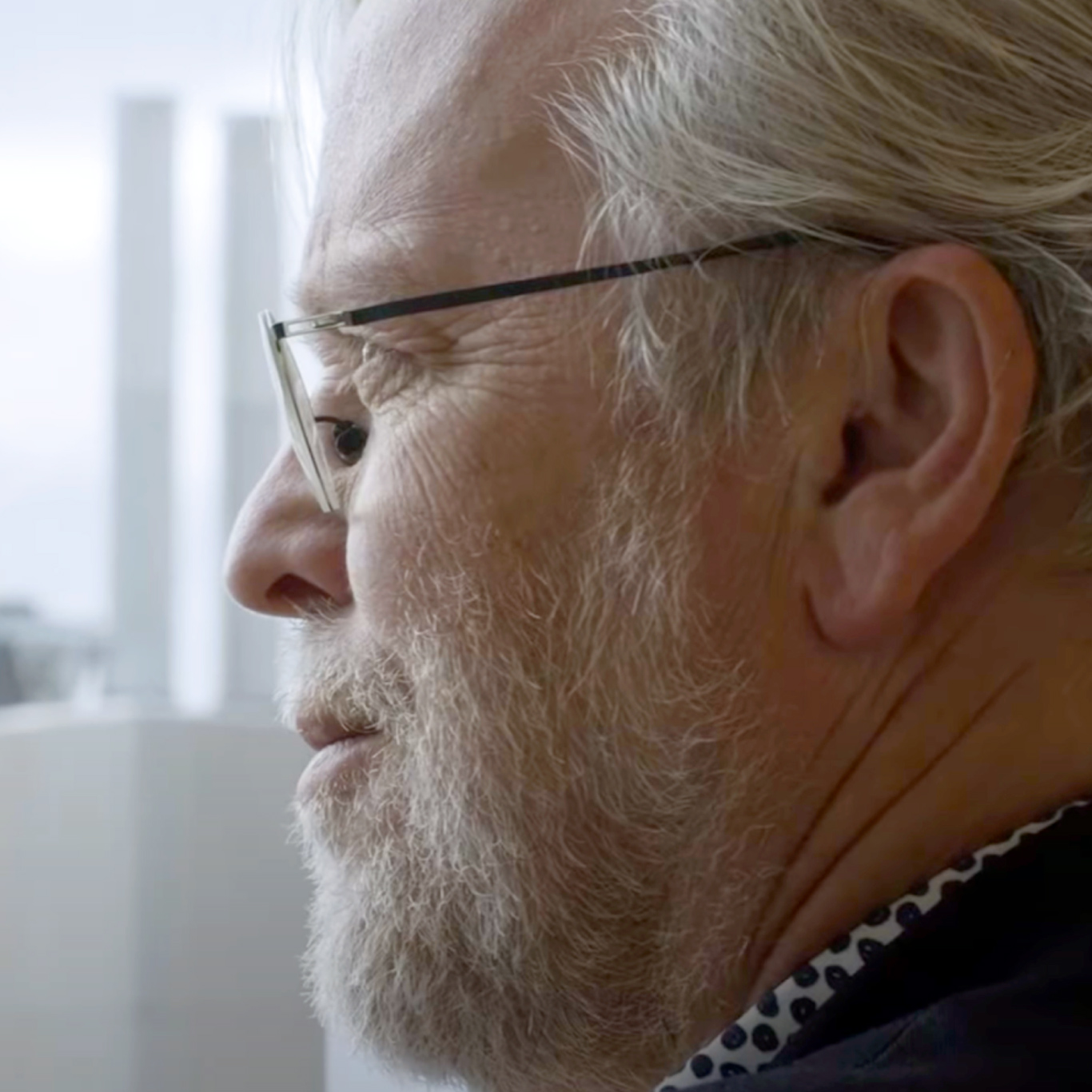
Coolbrook’s RotoDynamic technology is one of few viable solutions for greenhouse gas emissions, replacing the burning of fossil fuel by renewable electricity as the energy source.
Dr. Ir. Bert Kip
Former CEO, Brightlands Chemelot Campus