Aluminum industry decarbonization
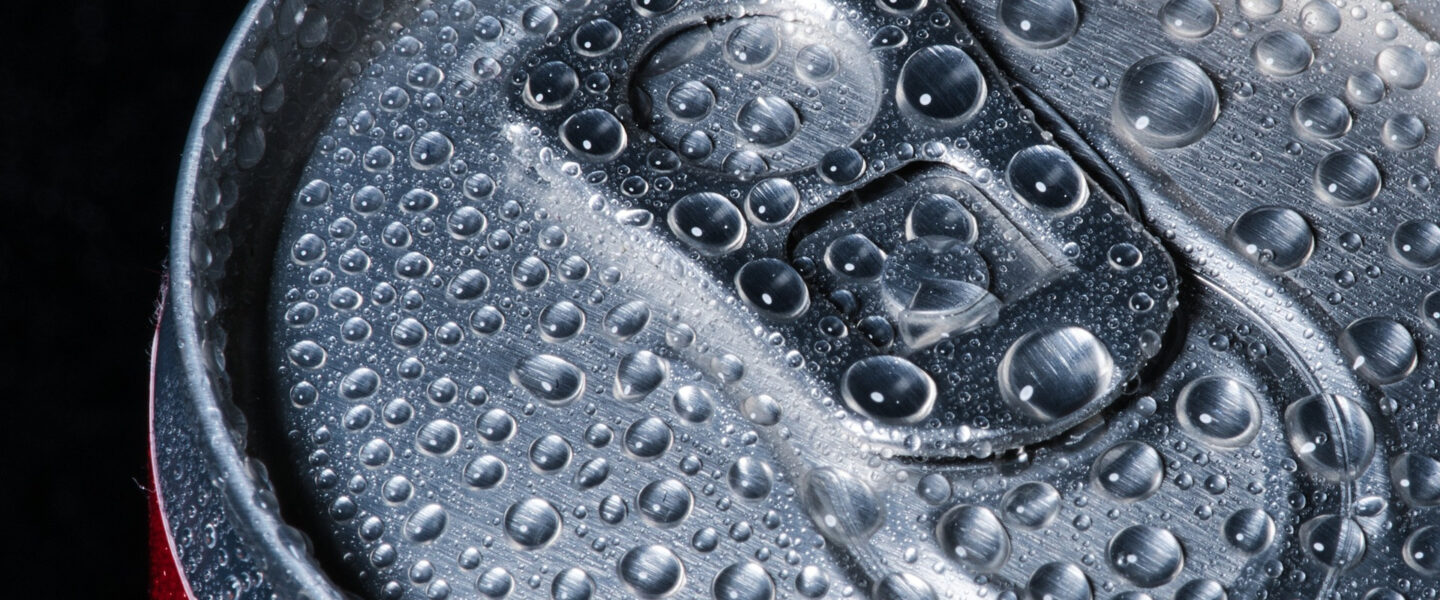
Electrification and decarbonization of aluminum industry
The aluminum industry is responsible for approximately 2% of global CO2 emissions, making it a significant contributor to industrial greenhouse gases. This is largely due to the energy-intensive nature of aluminum production, particularly in processes like alumina calcination and aluminum melting, which have traditionally relied on fossil fuels. Decarbonizing this sector is critical to reducing industrial emissions and achieving global climate goals.
Electrification technologies provide a the most efficient pathway to cutting emissions in aluminum production. By replacing fossil-fuel-powered systems with electric-based solutions, the industry can make significant strides toward sustainability and carbon neutrality.
Coolbrook’s RotoDynamic HeaterTM (RDH) offers a unique solution to electrify industrial heating processes up to 1700°C without burning fossil fuels. Our innovative technology can help the aluminum sector significantly reduce CO2 emissions, enhance energy efficiency, and accelerate progress toward a low-carbon future.
Roadmap and the process
Path to decarbonizing aluminum processes
2025-26
First Applications
Primary and secondary aluminum:
- Electrification of holding and/or casting furnace
- Electrification of reheating furnace
- Electrification of heat treatment furnaces
Secondary aluminum:
- Electrification of de-coating kiln
2027-28
Full electrification of high temp. heat
Primary and secondary aluminum:
- Electrification of off-gas incinerator
Primary aluminum:
- Electrification of alumina calcination process
Secondary aluminum:
- Partial electrification of melting furnace
2030+
Full decarbonization
Secondary aluminum:
- Full electrification of melting furnace
Discover
RotoDynamic Heater in aluminum industry
RotoDynamic Heater uses electricity to heat gases like air, nitrogen, and steam, reaching high process temperatures without burning fossil fuels. In aluminum production, RDH can replace traditional fossil fuel heating, leading to significant benefits in the aluminum industry.
Key benefits of the technology:
- Scalability to high temperatures (up to 1700 ˚C degrees) and to size categories (50+ MW equipment size)
- Elimination of fossil fuel derived CO2, NOx and SOx emissions by replacing fossil fuels with electrification
- High energy efficiency of 90 – 95% for the conversion of electricity to heat
- Compact equipment size and possibility to retrofit into existing industrial facilities
- Improved process energy efficiency
- Improved process control, quality and yield
- Competitive CAPEX and OPEX
Contact us
Example use cases for decarbonizing aluminum process
The RotoDynamic Heater can be fitted to new or existing industrial processes with multiple use cases in the aluminum production chain to replace the burning of fossil fuels in the generation of process heat.
Alumina refining
1. Electrification of alumina calcination process
Use case and Coolbrook solution in brief
Replacing fossil fuel burners in the alumina calcination kiln with high temperature heat generated by the RDH:
- Heating medium: Air or exhaust gas
- Temperature out: 1,000 – 1,300˚C
Customer benefits
- Elimination of CO2 emissions by replacing the fossil fuel-based heating duty with renewable electricity
- Cost savings from reduced carbon emission costs as existing fossil fuel solution (natural gas, LPG, diesel, etc.) are replaced
- Potential to utilize low-priced renewable energy, further decreasing OPEX
- Utilization of exhaust gas heat energy resulting in improved energy efficiency and reduced operating cost
Melting and casting
2. Electrification of melting furnace
Use case and Coolbrook solution in brief
Partial of full electrification of the aluminum melting furnace by replacing fossil fuel burners with heat generated by the RDH:
- Heating medium: CO2, N2 or exhaust gas
- Temperature out: Up to 1,500˚C
Customer benefits
- Significant reduction or full elimination of CO2 emissions by replacing the fossil fuel-based heating duty with RDH
- Ability to accurately control the temperature in the process to optimize operating parameters and improve energy efficiency
- Cost savings from reduced carbon emission costs as existing fossil fuel solution (natural gas, LPG, diesel, etc.) are replaced
- Potential to utilize low-priced renewable energy, further decreasing OPEX
- Utilization of exhaust gas heat energy resulting in improved energy efficiency and reduced operating costs
3. Electrification of holding and/or casting furnace
Use case and Coolbrook solution in brief
Full electrification of holding / casting furnaces by replacing fossil fuel-generated heat with RDH-generated heat:
- Heating medium: CO2, N2 or exhaust gas
- Temperature out: Up to 1,200˚C
Customer benefits
- Full elimination of CO2 emissions by replacing the fossil fuel-based heating duty with RDH
- Ability to accurately control the temperature in the process to optimize operating parameters and improve energy efficiency
- Cost savings from reduced carbon emission costs as existing fossil fuel solution (natural gas, LPG, diesel, etc.) are replaced
- Potential to utilize low-priced renewable energy, further decreasing OPEX
- Utilization of exhaust gas heat energy resulting in improved energy efficiency and reduced operating costs