Coolbrook makes petrochemical industry more sustainable with innovative pilot
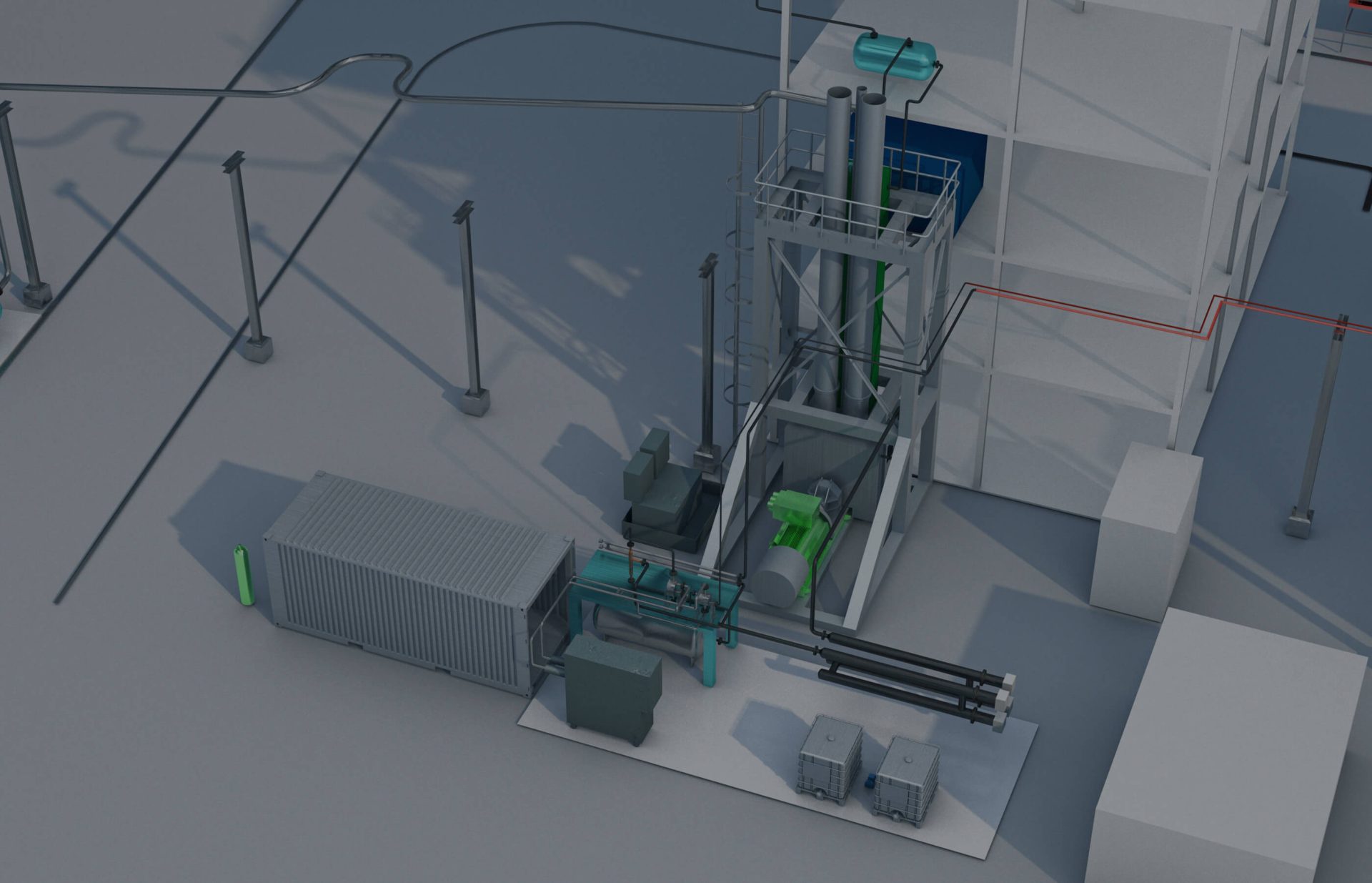
Contact
For more information, please contact:
Sander van der Kaaij
Sander.vanderKaaij@hkstrategies.com
+31 6 27 34 00 91
Coolbrook is receiving a grant of 5.5 million euros from the Dutch Ministry of Economic Affairs and Climate for a large-scale pilot project with an electrically powered naphtha cracker.
- The Finnish-Dutch company Coolbrook is receiving a grant of 5.5 million euros from the Ministry of Economic Affairs and Climate for a large-scale pilot project with an electrically powered naphtha cracker. This grant is a significant part of a total investment of over 12.5 million euros in this pilot. The other 7 million euros comes from private investors in Finland.
- After years of research, the RDR technology is now ready to be tested on a large scale at the Brightlands Chemelot Campus in Geleen. Building the pilot will take until April 2022 and doing all tests will take 1,5 years.
- The use of this electric naphtha cracker makes a significant contribution towards CO2 reductions, a sustainable production process of plastics and the petrochemical industry in the Netherlands and can completely replace the traditional, energy – and fossil fuel – intensive naphtha crackers.
Geleen, July 27, 2021 – The Finnish-Dutch company Coolbrook has received a grant of 5.5 million euros from the Ministry of Economic Affairs and Climate for further development of their electrically powered naphtha cracker on the Brightlands Chemelot Campus in Geleen. Coolbrook has been working for a long time on the development of a sustainable naphtha cracker, which supplies the raw materials for plastics such as polyethylene and polypropylene through a petrochemical process. The energy which is needed for this process is now generated with fossil energy sources. Coolbrook’s innovative Rotor Dynamic Reactor (RDR) technology radically changes this and eliminates the CO2 emissions of this process with use of renewable energy.
With the introduction and development of RDR technology, Coolbrook is demonstrating its commitment to making a serious contribution to the sustainability of the petrochemical industry in the Netherlands and in Europe. The recent “Fit for 55” legislation announced by the European Commission and the more stringent goals of the Dutch Climate Agreement only increase the urgency of this goal. Coolbrook therefore sees the Dutch government’s subsidy of the pilot project in Geleen with the RDR reactor as an important endorsement.
The basis for the RDR technology was laid by Coolbrook engineers in cooperation with the universities of Oxford, Cambridge, and Ghent as well as with Neste Engineering, Mitsubishi Heavy Industries, and Schmidtsche Schack. Originally a Finnish company, Coolbrook has been operating in Geleen, the Netherlands, since the beginning of 2020. After years of research, RDR technology is now ready to be tested on a large-scalepilot at the Brightlands Chemelot Campus. This is the gateway to large-scale industrial application, and thus sustainability, of the petrochemical industry in the Netherlands and Europe.
Ilpo Kuokkanen, Founder and Executive Chairman of Coolbrook states: “I am grateful to the Dutch government for embracing the added value of this innovative technology and enabling further development through a substantial grant. If the EU, national governments and the large oil companies want to make a real contribution to making the petrochemical industry more sustainable, within two years our RDR technology will be able to put an end to the now highly intensive and polluting industrial processes.”
The introduction of the RDR reactor represents a fundamental change in the cracking of naphtha. A traditional cracker heats naphtha through the walls of the furnace coils. For this reason, it is necessary for the entire furnace to be heated, which is very energy intensive. The RDR technology as developed by Coolbrook heats naphtha exclusively through the movements of a rotor, which accelerates the naphtha in the reactor above the speed of sound. The shock wave which is then generated causes the conversion of the kinetic energy into heat which makes the final cracking possible. In addition to the fact that this innovative technology provides up to 20% more Ethylene output than a traditional cracker, the contribution to the energy transition and to making traditional industry and plastic production more sustainable is even more significant. Implementation of the RDR technology leads to a complete elimination of CO2 emissions, 30% reduction of energy consumption and therefore 60% more profit.
Bert Kip, CEO of Brightlands Chemelot Campus: “Coolbrook’s unique technology makes a tremendous contribution to the future of electric cracking, and thus to the campus as the preferred location for sustainable innovation.”
Eric Appelman, CTO at Brightlands Chemelot Campus adds: “Coolbrook has an absolutely unique way to transfer mechanical energy into thermal energy, making it possible to reach the temperatures required for the largest chemical process in the world, steam cracking. The big advantage is that this can be done very well with electricity, which should be renewable. Other benefits are a more valuable product mix and a much better ability to respond to fluctuating energy supply. We are extremely proud that this disruptive technology and this great team will settle on Brightlands Chemelot Campus to take this innovation to semi-industrial scale”.
Currently, Coolbrook is already in negotiations with several major oil companies that want to make use of the RDR technology. Further details are expected to be announced by Coolbrook in the near future.
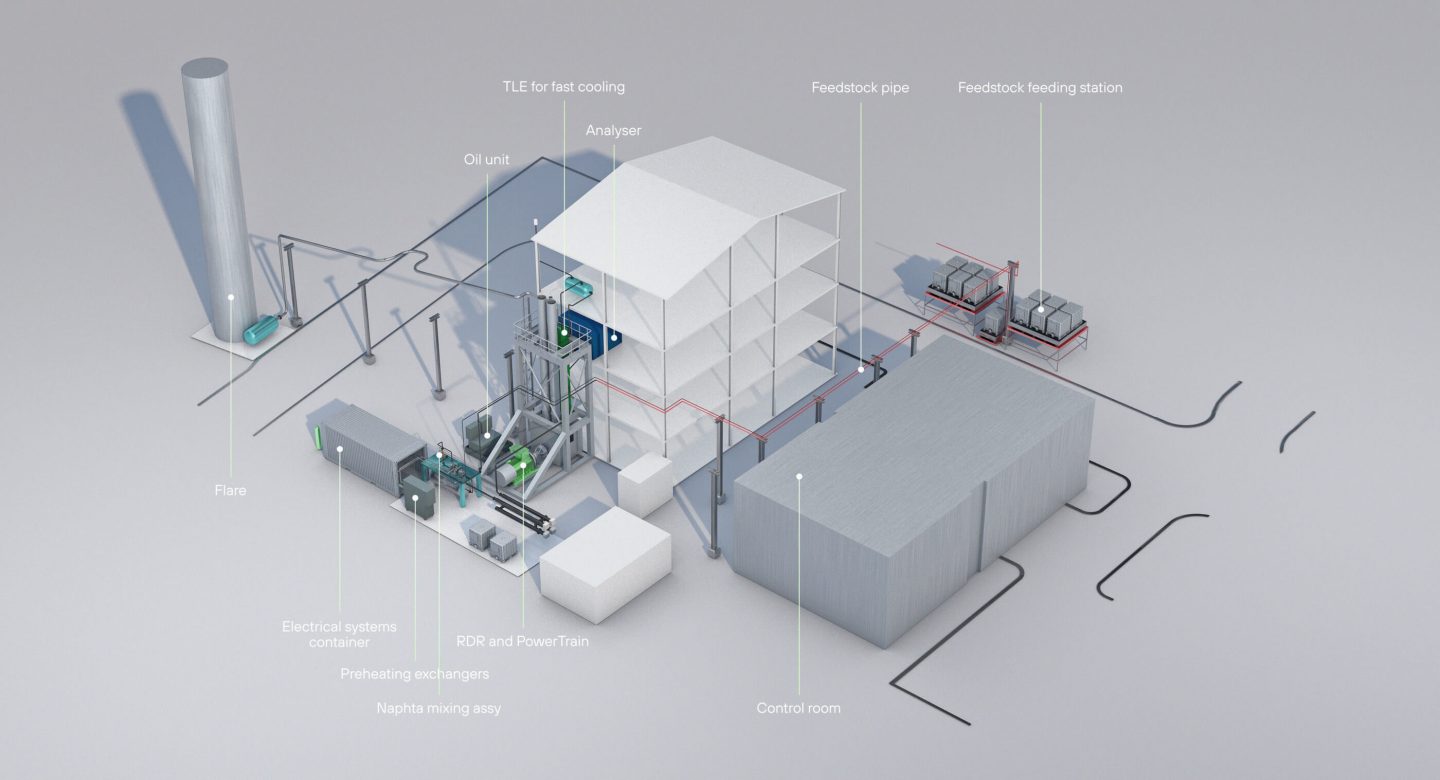
About Coolbrook
Coolbrook Ltd. is a Finnish engineering company on a mission to create a cleaner, more sustainable and profitable way to produce Olefins, the main component in the petrochemical industry and the production of plastics, chemical products, packaging and more. Coolbrook’s Roto Dynamic Reactor (RDR) is a revolutionary technology that combines space science, turbomachinery and chemical engineering to replace the current inefficient and polluting steam cracking methods used to make Olefins with a radically cleaner and more effective alternative. Backed by a growing number of governments, petrochemical producers and environmental regulators, Coolbrook’s RDR technology is set to become the new global standard in Olefins production. http://coolbrook.com/