Coolbrook’s RotoDynamic Technology carries out successful first real-world demonstration
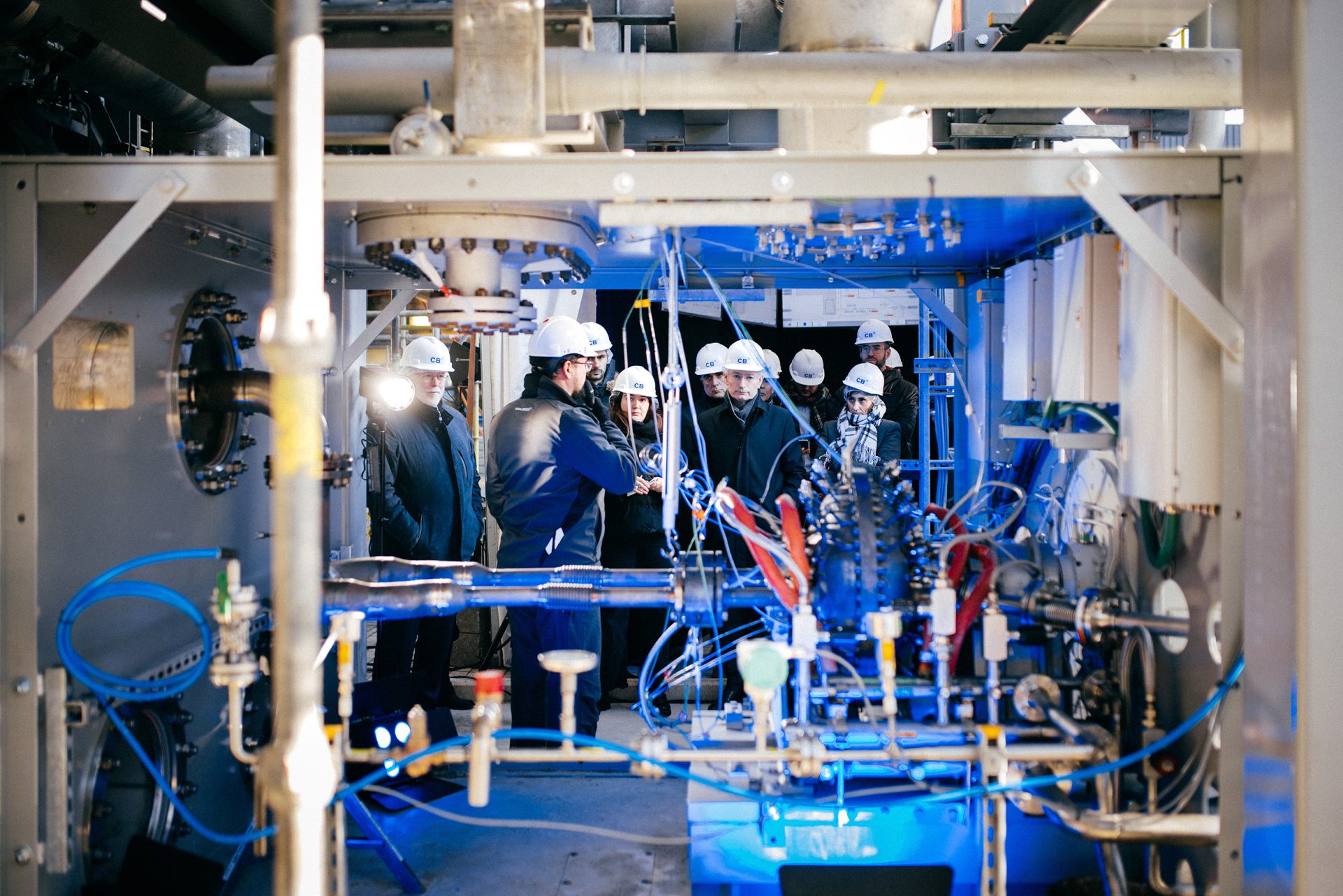
Contacts
For further information, please contact:
Coolbrook
Jenni Schumacher, SVP, Communications
jenni.schumacher@coolbrook.com
tel. +358 50 554 6810
Large scale pilot plant proves electrification can decarbonise industrial production with the potential to cut more than 2 billion tons of annual CO2 emissions
Transformational technology and engineering company Coolbrook has conducted the first live pilot of its RotoDynamic Technology to electrify high-temperature industrial processes. Hosted at the Brightlands Chemelot Campus in Gelleen, Netherlands on Dec. 12, 2022, the demonstration marked the technology’s debut activation in an industrially relevant environment setting the scene for a new clean industrial era.
The large-scale pilot plant will demonstrate the performance of the RotoDynamic Technology for steam cracking in petrochemicals (RotoDynamic Reactor, RDR) as well as high-temperature process heating across various industry sectors (RotoDynamic Heater, RDH). The plant is designed to generate process temperatures of around 1000 degrees with 100% renewable electric power, marking a major milestone towards CO2-free manufacturing in heavy industries. Such temperatures are necessary to replace fossil fuel burning with electrification in industries that have been considered difficult to decarbonise such as petrochemicals and chemicals, cement, and steel manufacturing. Once implemented at scale, the RotoDynamic Technology has the potential to reach temperatures of 1700 degrees and cut over 2 billion tons of annual CO2 emissions when applied to heavy industry.
“It was an honour to be able to show our technology in action after a decade of development,” said Ilpo Kuokkanen, Executive Chairman of Coolbrook. “We made history by proving that electrification can deliver the temperatures that industrial manufacturers need to achieve CO2-free production. Sharing this moment with our commercial and academic partners was a pivotal moment in our goal of full commercial production by 2024.”
Coolbrook was joined by representatives from its partners Shell, ABB, Braskem and CEMEX, and its academic partners Budimir Rosic from the University of Oxford and Liping Xu from the University of Cambridge.
“We were delighted to see Coolbrook’s RotoDynamic technology, which is central to clean industrial production especially in hard-to-abate sectors, achieve this milestone,” said Colin Ward, Senior Vice President, Chemicals and Refining, ABB. “We are committed to helping reduce our customers’ annual CO2 emissions by 100 million megatons by 2030, and this partnership and successful pilot successfully showcases a future driven by electrification.”
“This pilot was a fantastic preview of what we can expect when we incorporate Coolbrook’s equipment at our plants, and watching it run in person has proved that we are on the path to decarbonising our cement production. Seeing the electrification technology we have invested in progress from theory to reality supports our Future in Action program, aimed to build a more sustainable, circular future, with the primary objective of becoming a net-zero CO2 company,” said Roberto Ponguta, VP, Operations from CEMEX. “We are looking forward to continuing our successful cooperation and deploying the Coolbrook Technology at our production sites.”
The next milestone for Coolbrook’s RotoDynamic technology is to deploy the technology in commercial demonstration projects at customer sites aimed to be operational in 2024. Coolbrook has announced partnerships with Shell, Braskem, CEMEX, Ultratech and ArcelorMittal to accelerate and deploy the technology in industrial facilities. Full commercial deployment of the technology is expected to start by 2025.