Application of RotoDynamic Technology in Decarbonizing Steel Industry
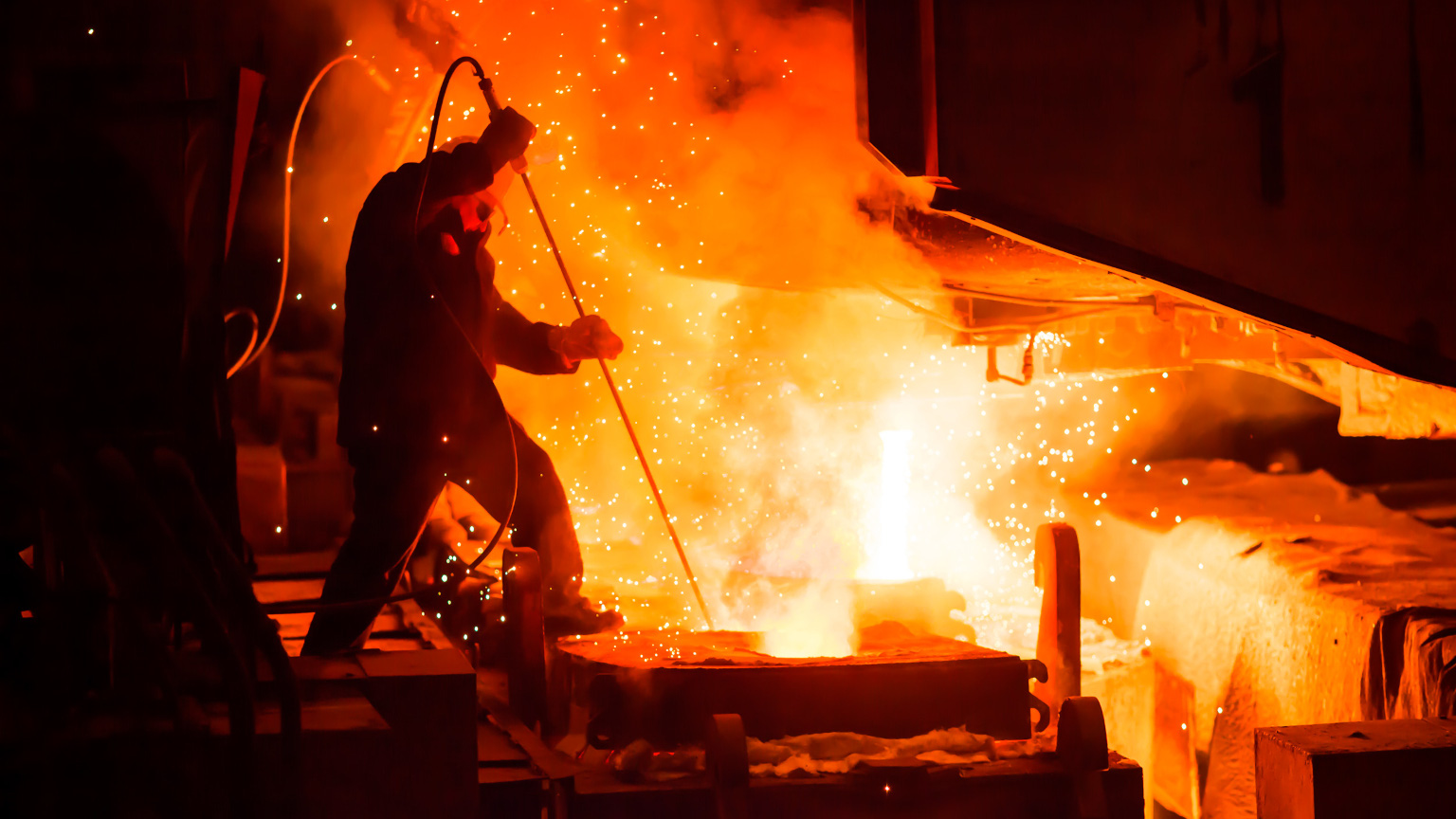
Written by
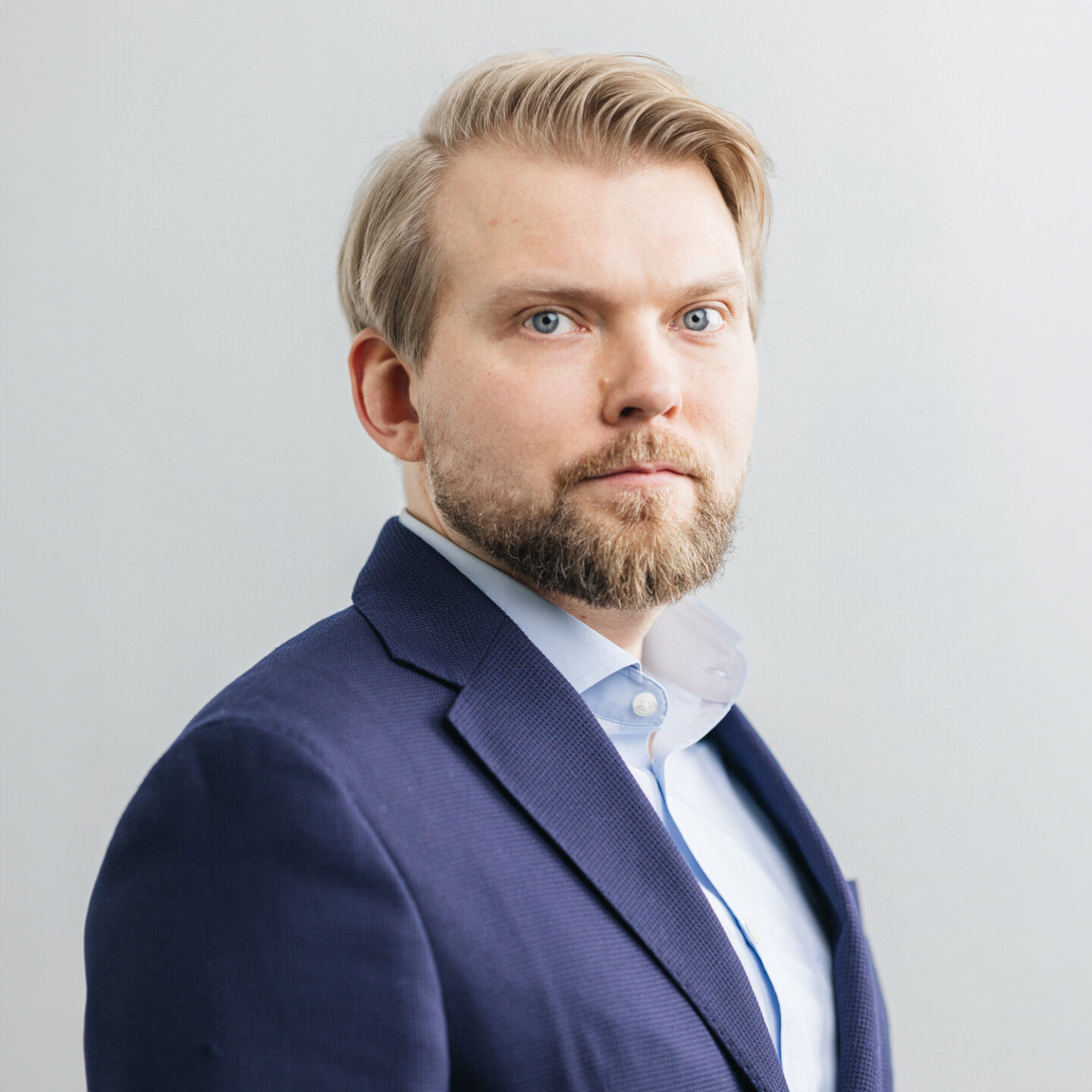
Lauri Peltola
CCO, Coolbrook
The steel sector is the foremost contributor to global industrial emissions, releasing an average of 3.7 billion metric tons of CO2 annually and accounting for 7% of all human-made emissions. Approximately 85% of the industry’s overall energy consumption is derived from burning fossil fuels. With the growing global demand for iron and steel, it is essential to decarbonize the manufacturing processes to meet net-zero emissions targets by 2050.
Decarbonization of the steel sector requires a shift in how heat is generated, and the optimal approach involves direct electrification. The electrification of industrial processes with increasingly available renewable energy represents a €1 trillion economic opportunity, paving the way for the conversion of nearly all fossil fuel-dependent processes to electricity, resulting in significant emission reductions.
Enter the game-changing RotoDynamic Heater™ (RDH™)—Coolbrook’s bespoke, electrified industrial heating technology, powered by renewable energy, with the potential to cut global industrial emissions by a third (two giga-tons) and place steel manufacturers at the forefront of the clean, new industrial era.
Based on turbomachinery with 100 years of operating experience, the RotoDynamic Heater™ functions akin to a gas turbine in reverse; employing electric motors to spin blades and produce heat directly within gas with 95% energy efficiency. The technology is on track to generate temperatures up to 1,700°C within milliseconds while being only a few meters in size due to not requiring bulky resistive heating components. Providing high energy density, easy scalability, and precise temperature control, this decarbonization technology can deliver anywhere from 5 to 100s of mega-watts in capacity without burning fossil fuels. It can also be operated with various gasses, including air, nitrogen, CO2, methane, and other process gasses, ensuring high availability.
Simple in implementation, the RotoDynamic Heater™ can be seamlessly retrofitted into existing manufacturing plants with different setups without complicating the existing structure, facilitating widespread adoption and complementing other decarbonizing technologies and decarbonization solutions. Its high energy intensity and compact size allow installation directly at locations where heat is needed, thus enabling efficient integration in brownfield sites.
The RotoDynamic Heater™ is the culmination of two decades of research and development undertaken by Coolbrook, in collaboration with esteemed academic institutions like Oxford, Cambridge, and Ghent Universities.
How the RotoDynamic Heater™ facilitates more efficient and decarbonized steel production
Steel is manufactured through two main methods: primary and secondary steelmaking. Primary steelmaking involves converting iron ore into metallic iron in blast or direct reduction furnaces, followed by the conversion of metallic iron into steel through further reduction of its carbon content in basic oxygen or electric arc furnaces. Secondary steelmaking involves smelting recycled iron in electric arc furnaces and then further processing it with carbon and other alloys. These processes, along with supporting processes such as casting, hot and cold rolling, annealing, coke production, and lime production require temperatures reaching up to 1,600°C.
Some primary steel manufacturing plants use green hydrogen gas instead of natural gas to reduce iron ore into metallic iron in direct reduction furnaces to decarbonize their processes, but this still requires temperatures up to 1,100°C and constant heating.
The RotoDynamic Heater™ has use cases across these steelmaking processes, especially by functioning as a type of electric kiln. Specifically, the RotoDynamic Heater™ can support in:
- Preheating combustion air for blast furnaces in primary steelmaking, reducing energy usage and reliance on fossil fuels, and providing an opportunity to eliminate hot stoves
- Preheating injection gas in to blast furnace tuyeres and shafts to significantly reduce coke consumption and decarbonize blast furnace operations
- Preheating scrap metal for electric arc furnaces, reducing energy needs, improving process stability, and enhancing steel recycling efficiency
- Supplying high temperatures and consistent heating of reduction gas (hydrogen, natural gas) at DRI plants
- Preheating refractory materials, including in ladles and tundishes
- Providing high-temperature heat for heat treatment furnaces (annealing, tempering) to fully decarbonize heat treatment processing
- Providing heat for cold and hot rolling to improve energy efficiency and reduce reliance on fossil fuels
- Replacing fossil fuel burners in reheating furnaces, transforming traditional furnaces to electric furnaces
- Providing heat for surface treatment lines (galvanizing, coating) to reduce carbon emissions and improve energy efficiency
- Heating coal as part of coke production, reducing reliance on fossil fuels
- Reusing hot flue gas streams, improving energy efficiency by 10-30% and reducing costs
- Capturing waste heat streams, significantly improving the overall energy efficiency of the process
- Increasing steel yield due to improved energy and process efficiencies
Overall, the RotoDynamic Heater™ empowers steel manufacturers to lower fossil fuel consumption and cost of decarbonization per ton of steel while improving process efficiencies and yield, optimizing return on investment and advancing towards a net-zero future.
The Future of RotoDynamic™ Technology in the steel sector
Early adopters of decarbonization technology such as the RotoDynamic Heater™ will not only contribute towards the betterment of the planet and future-proof their operations ahead of the full phase-out of fossil fuels, but also unlock long-term profit gains through reduced waste, improved efficiencies, and greater product yields while attracting more sustainability-centered investments.
Coolbrook collaborates with prominent industrial partners to evaluate the technology and strategize its integration into steel production. Large-scale implementation is planned to commence at customer facilities in 2024, with full commercial deployment anticipated by 2025. Among Coolbrook’s industrial partners in these sectors are ArcelorMittal and JSW.
By working closely with a diverse network of industry collaborators, including key technology firms and industrial manufacturers globally, Coolbrook remains committed to spearheading widespread decarbonization efforts across iron and steel, cement, petrochemical, and other industrial sectors; heralding a clean, new industrial era.
You can read more about the application of RotoDynamic Technology on our Iron and Steel Industry page