RotoDynamic Technology in Decarbonizing Petrochemical Industry
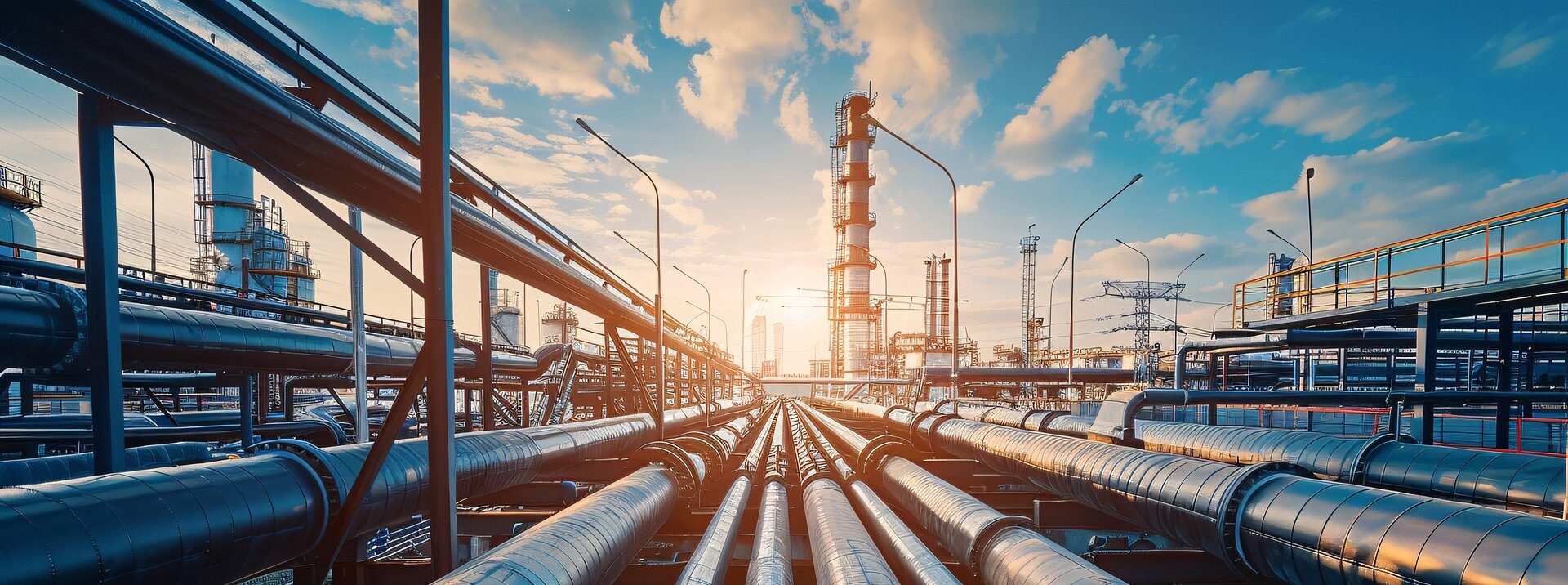
Written by
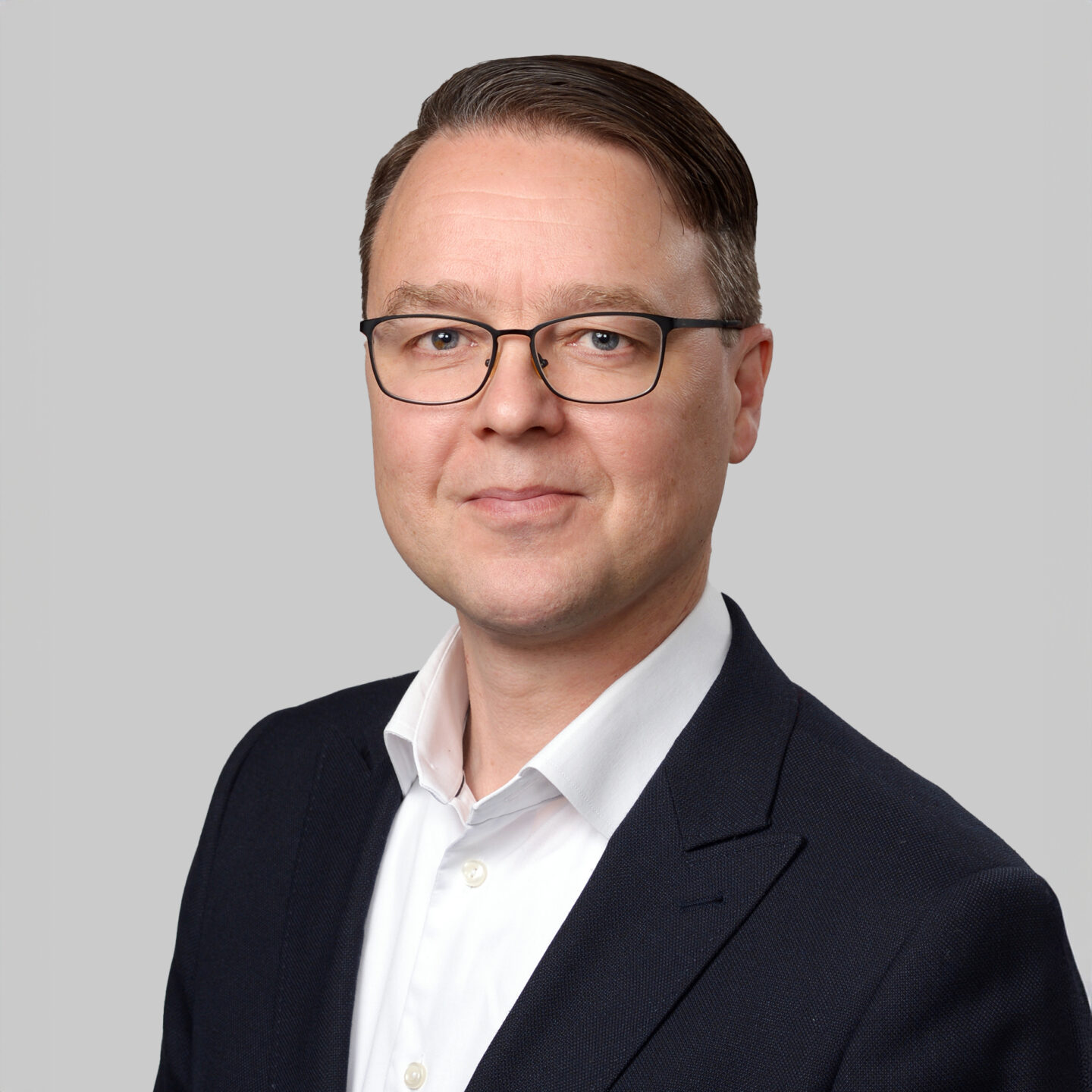
Tuomas Ouni
Head of Process Development, Coolbrook
Coolbrook’s RotoDynamic Technology is revolutionizing high-temperature industries by replacing fossil fuels with renewable electricity. The RotoDynamic Reactor™ (RDR™) and Heater™ (RDH™) provide ultra-efficient heat, cutting CO₂ emissions while boosting productivity across petrochemical, and many other industries. With applications that can significantly decarbonize industrial processes, this technology is paving the way for sustainable production and a cleaner future in petrochemicals.
Olefins are one of the two most common classes of petrochemicals. Annually, olefin production emits 300 million tons of CO2, primarily stemming from the utilization of fossil fuel-powered steam cracking furnaces.
As global demand for petrochemicals increases, its production processes must undergo direct decarbonization and refinement to achieve net zero emissions by 2050. Industrial decarbonization necessitates a shift in heat generation, with direct electrification being the most effective method. Electrifying industrial heating using renewable energy—which continues to become more available— presents a €1 trillion economic opportunity. This transition enables the conversion of nearly all fossil fuel-based processes to electricity, leading to substantial emission reductions.
Coolbrook’s revolutionary RotoDynamic Reactor™ (RDR™) and RotoDynamic Heater™ (RDH™) play a key role in this transition by allowing industrial manufacturers to decarbonize their operations quickly using renewable electricity. With over 40 applications in heavy industries, the RDR™ and RDH™ can potentially reduce global industrial emissions by a third. It works similarly to a gas turbine in reverse, utilizing electric motors to spin blades and generate heat directly within gas with 95% energy efficiency.
RotoDynamic Technology can reach temperatures up to 1,700°C in milliseconds, offering dozens of mega-watts of capacity without relying on fossil fuels. Its compact design, free from bulky resistive heating components, allows for easy retrofitting into existing manufacturing plants, supporting widespread adoption and integration with other decarbonizing technologies, even in brownfield sites. The RotoDynamic technology results from two decades of research and development by Coolbrook in partnership with prestigious academic institutions such as Oxford, Cambridge, and Ghent Universities.
How the RotoDynamic Reactor™ facilitates more efficient petrochemical production
Steam cracking furnaces use temperatures up to 950°C with steam to break down hydrocarbon feedstocks into smaller molecules like ethylene and propylene through the thermal cracking process.
The RotoDynamic Reactor™ has use cases across the olefin manufacturing processes. Specifically, the RotoDynamic Reactor™ can support in:
- Heating feedstock directly, increasing efficiency, and replacing fossil fuel furnaces used for steam cracking in olefin production plants (RDR™)
- Generating 20% extra ethylene yield due to its fast operation lowering the residence time and cutting flaring-associated product losses from rapid startups and shutdowns (RDR™)
- Reducing maintenance costs and requirements due to being much less prone to wear, tear, and coking than conventional steam cracking furnaces
- Compatibility with olefin plants using renewable or recycled feedstock
- Lowering capital expenditure due to being smaller in size than steam cracking furnaces
Additionally, the RotoDynamic Heater™ (RDH™) can support in preheating various feed materials indirectly and providing high temperature heat across use cases at petrochemical plants
Ultimately, the RotoDynamic Technology enables olefin manufacturers to significantly cut CO2 emissions and energy usage while improving product yield and process efficiencies throughout olefin manufacturing plants.
The Future of RotoDynamic™ Technology in petrochemical industry
Adopting decarbonization technologies like the RotoDynamic Heater™ and RotoDynamic Reactor™ offers early movers a unique opportunity. These technologies promote environmental sustainability, prepare businesses for a future without fossil fuels, and deliver long-term financial benefits through reduced emissions, enhanced efficiency, higher product yields, and increased appeal to sustainability-focused investors.
Coolbrook is actively working with leading industrial companies to test and plan the integration of its technologies into the manufacturing of olefins and other key petrochemical materials. Large-scale adoption of the RDR is scheduled to begin in 2027, with full commercial deployment expected by 2028. Prominent partners in this initiative include Linde Engineering, Braskem, and Sabic.
Through strategic collaborations with a diverse range of industry leaders, including major technology firms and global manufacturers, Coolbrook is spearheading extensive decarbonization efforts in petrochemical industry, paving the way for a clean, new industrial era.