Cement industry decarbonization
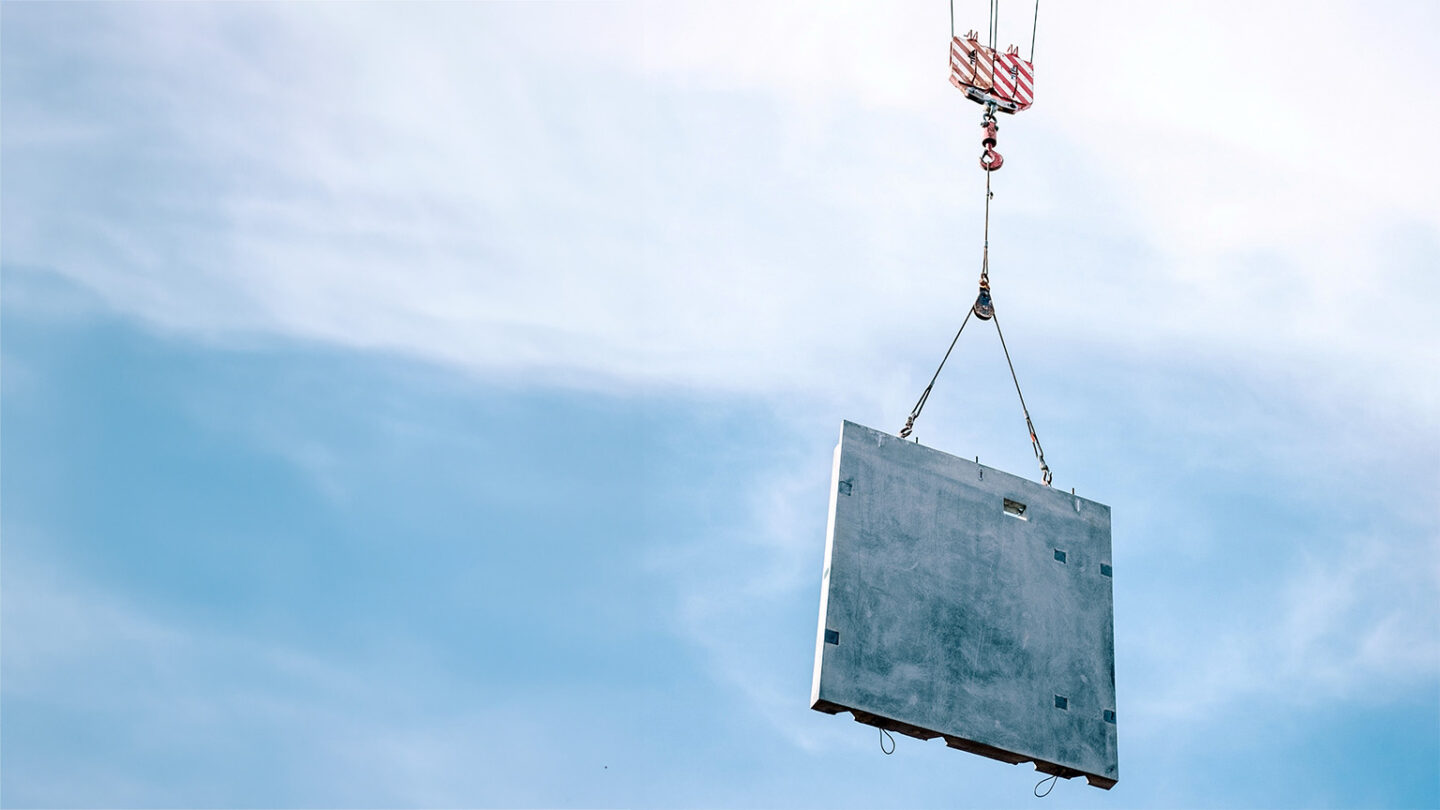
The Solution
Electrification and decarbonization of cement industry
The cement industry is one of the key contributing sectors to the industrial emissions – in fact, approximately a third of industrial CO2 emissions come from the cement industry. The industry has long been considered hard to abate, while cement companies strive to achieve their net zero targets and climate commitments.
Electrification is one way to eliminate the cement industry CO2 emissions that derive from burning fossil fuels in high-temperature processes in the cement industry.
Coolbrook’s RotoDynamic HeaterTM (RDH) is the only heat electrification technology capable to decarbonize industrial heating processes up to 1700°C without burning fossil fuels. The technology can cut 1,000 million tonnes of fossil fuel derived CO2 in cement production per year globally through electric-powered heaters, by eliminating the need to burn fossil fuels for generation of process heat.
Optimal use cases for early adoption of RotoDynamic Heater
- Clay calcination:
fossil free production by using RDH to heat the kaolinite, replacing current fossil fuel and enabling removal of all carbon emissions
- Cement kiln precalciner:
partially replacing fuels fired in a cement kiln precalciner
- White cement:
decarbonize and increase production: Using RDH to heat up the combustion air fed to the kiln to decrease the need of fossil fuels (~50%) and increase production capacity by up to 25%
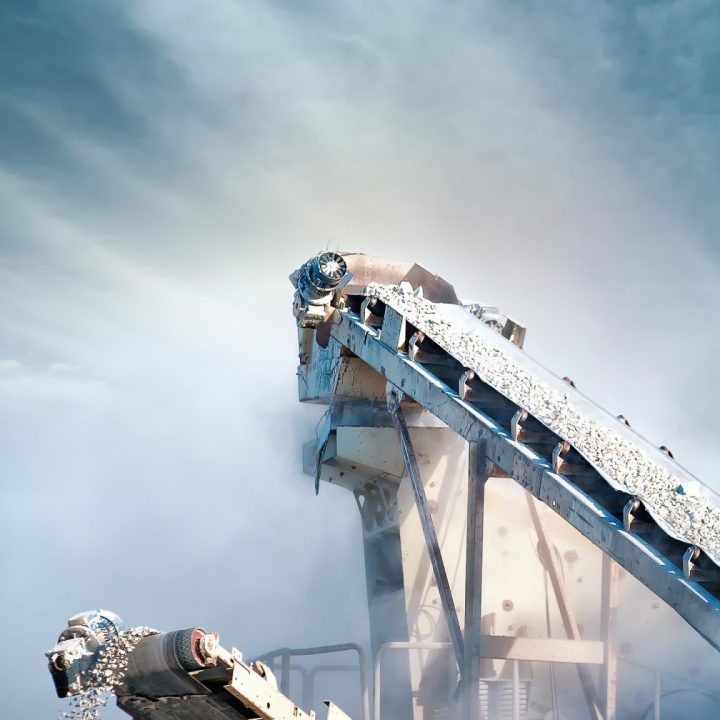
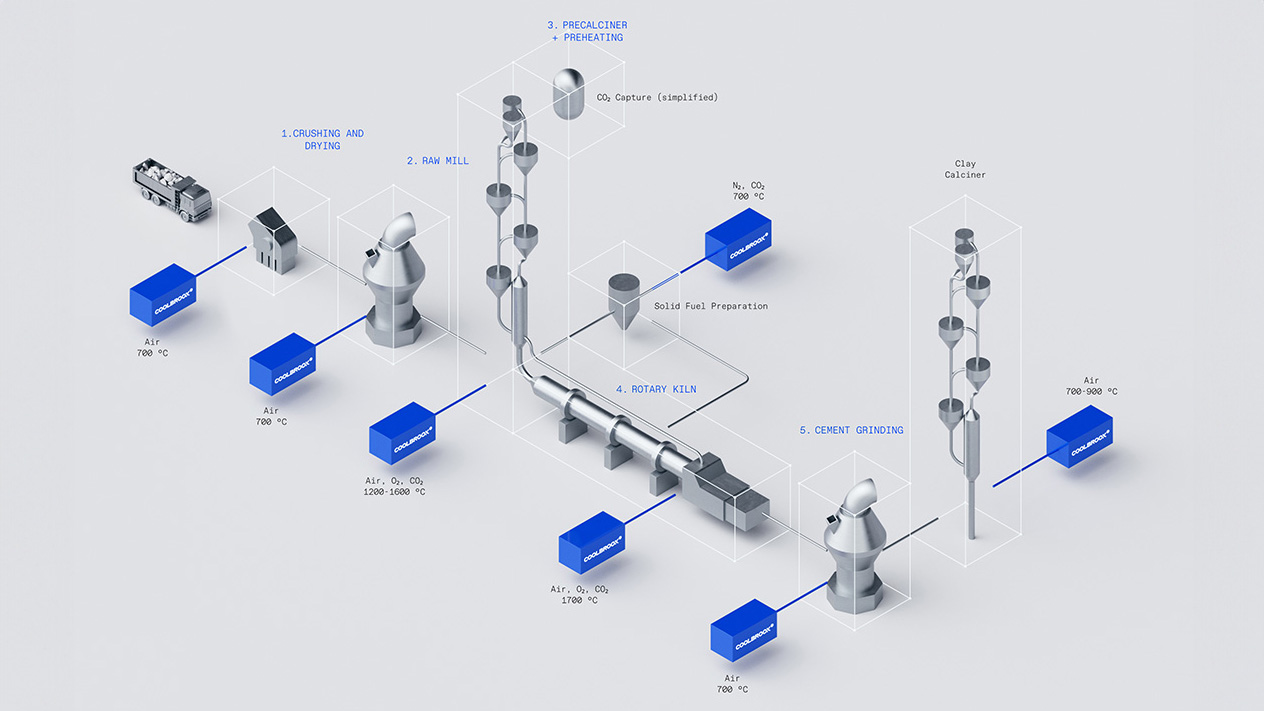
Discover
RotoDynamic Heater in cement industry
RotoDynamic Heater heats gas, such as air, nitrogen, steam, carbon dioxide, and process gases, with electricity to required high process temperatures, and the heated gas is used outside the heater to replace the burning of fossil fuels in process heating.
There are multiple use cases in cement production where the RotoDynamic Heater is an optimal solution for process heating and replacing the burning of fossil fuels. It can be used for example in pre-calcining for clinker production partially replacing existing fossil-firing with the RDH. Thanks to its compact equipment size, it can be fitted to both new and existing industrial facilities.
Key benefits of the technology:
- Scalability to high temperatures (up to 1700 ˚C degrees) and to size categories (50+ MW equipment size)
- Elimination of fossil fuel derived CO2, NOx and SOx emissions by replacing fossil fuels with electrification
- High energy efficiency of 92 – 95% for the conversion of electricity to heat
- Compact equipment size and possibility to retrofit into existing industrial facilities
- Competitive CAPEX and OPEX
Contact us
The process
Decarbonizing cement process
The RotoDynamic Heater can be fitted to new or existing industrial processes with multiple use cases in the cement production chain to replace the burning of fossil fuels in the generation of process heat.
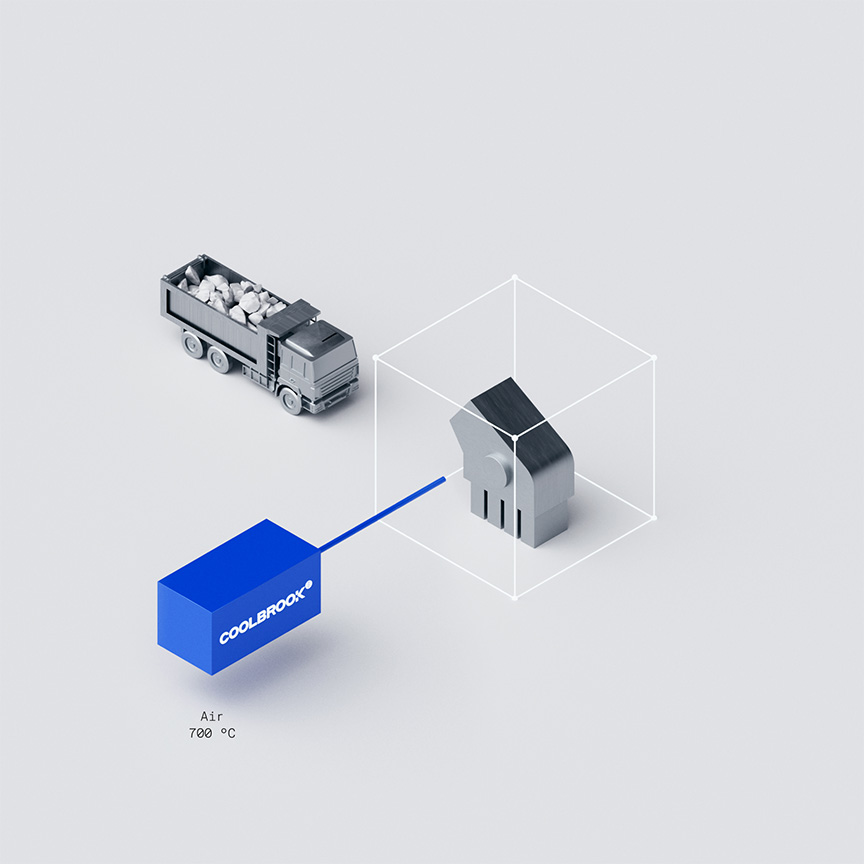
1. Raw material drying in a dryer-crusher
RDH provides heat into the cement factory raw materials crusher-dryer system, replacing fully or partially fossil fuels with electricity.
- Coolbrook solution: RotoDynamic Heater to 700˚C
- Temperature in: 150-200˚C
- Temperature out: 700˚C
Customer benefits:
- Significant reduction in CO2 emissions or fully CO2 emission free process by replacing fossil fuels with renewable electricity
- Cost savings from reduced carbon emission costs as existing fossil fuel solution (natural gas, LPG, diesel, etc.) are replaced
- Potential to utilize low-priced renewable energy, further decreasing OPEX
- Potential utilization of exhaust gas heat energy resulting in improved energy efficiency and reduced operating costs
2. Supplemental raw material drying in a raw mill
RDH replaces fossil fuel fired hot gas generators and provides supplemental heat into a cement factory raw mill to boost drying capacity.
- Coolbrook solution: RotoDynamic Heater to 700˚C
- Temperature in: ambient
- Temperature out: 700˚C
Customer benefits:
- Increase production by boosting the drying capacity without downgrading kiln thermal energy efficiency
- Significant reduction in CO2 emissions or fully CO2 emission free process by replacing fossil fuels with renewable electricity
- Cost savings from reduced carbon emission costs as existing fossil fuel solutions (natural gas, LPG, diesel, etc.) are replaced
- Potential to utilize low-priced renewable energy, further decreasing OPEX
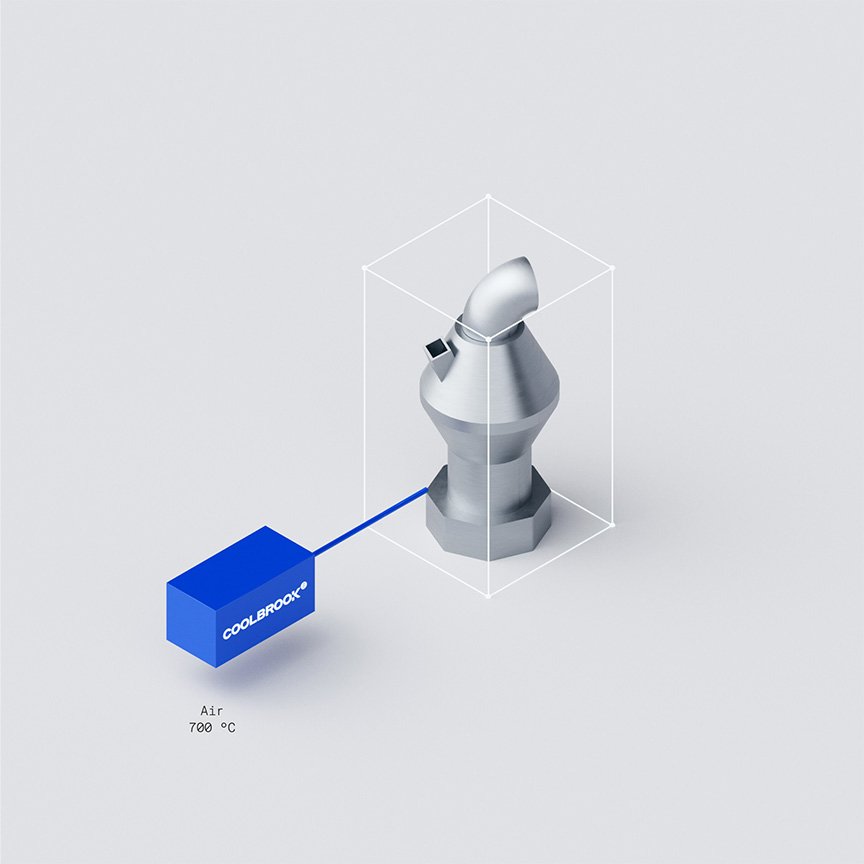
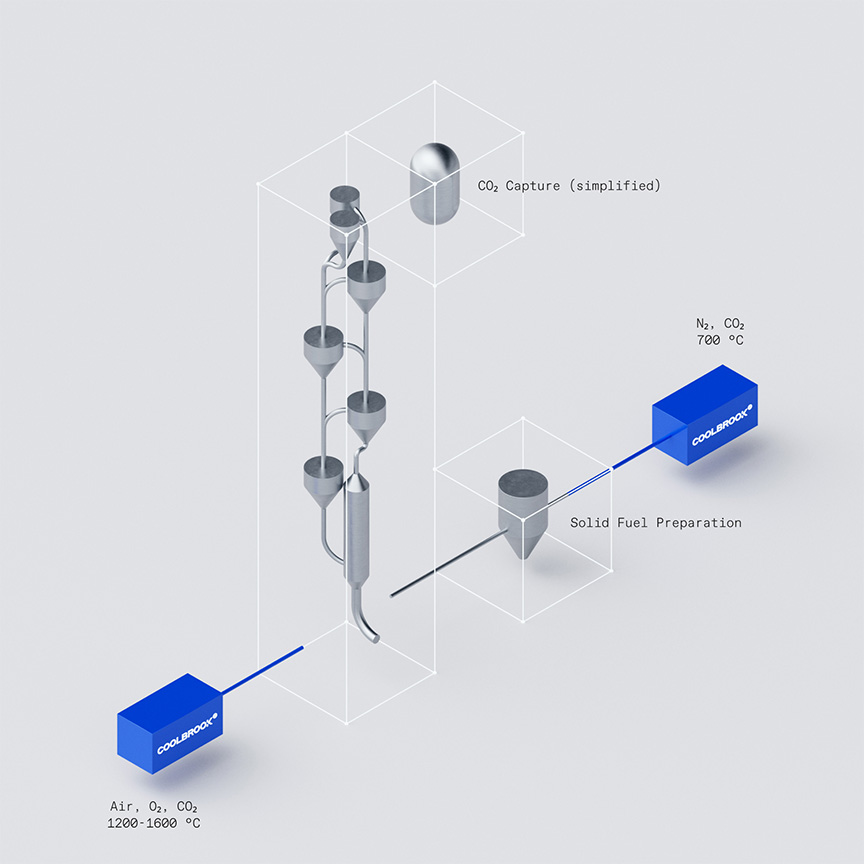
3. Partially replace fuels fired in a cement kiln precalciner
RDH provides heated air into a kiln precalciner to replace fuel fired in the precalciner
- Coolbrook solution: RotoDynamic Heater to 1200˚C, 1400˚C, and 1600˚C
- Temperature in: ambient
- Temperature out: 1200˚C to 1600˚C
Customer benefits:
- Significant reduction in CO2 emissions by replacing fossil fired in the precalciner with electricity produced heat
- Cost savings from reduced carbon emission costs as existing fossil fuel solution (coal, petcoke, natural gas, etc.) are replaced
- Potential to utilize low-priced renewable energy, further decreasing OPEX
- Ability to optimize costs and emissions by selectively replacing fuels fired in the kiln precalciner
4. Inert drying of solid traditional and alternative fuels
Replacing fossil fuel fired hot gas generators with Coolbrook RDH to provide heated inert gases (nitrogen, carbon dioxide) into a cement factory solid fuel preparation system
- Coolbrook solution: RotoDynamic Heater to 700˚C
- Temperature in: ambient
- Temperature out: 700˚C
Customer benefits:
- Decrease operating costs by increasing the fuel energy output and extending the fuel delivery system life by decreasing the moisture content of fuels
- Also, to boost alternative fuel substitution rates by reduction of moisture content of alternative fuels reducing emissions and carbons costs
- Ability to decrease moisture with no danger of fires or explosions
5. Partially replace fuels fired in a cement kiln main burner
RDH provides heated air into the clinker outlet of a cement kiln to replace fuel fired in the main burner
- Coolbrook solution: RotoDynamic Heater to 1500˚C, 1600˚C, and 1700˚C
- Temperature in: ambient
- Temperature out: 1500˚C to 1700˚C
Customer benefits:
- Significant reduction in CO2 emissions by replacing fossil fuel fired in the main burner with electricity produced heat
- Cost savings from reduced carbon emission costs as existing fossil fuel solutions (coal, petcoke, natural gas, etc.) are replaced
- Potential to utilize low-priced renewable energy, further decreasing OPEX
Ability to optimize costs and emissions by selectively replacing fuels fired in the main burner
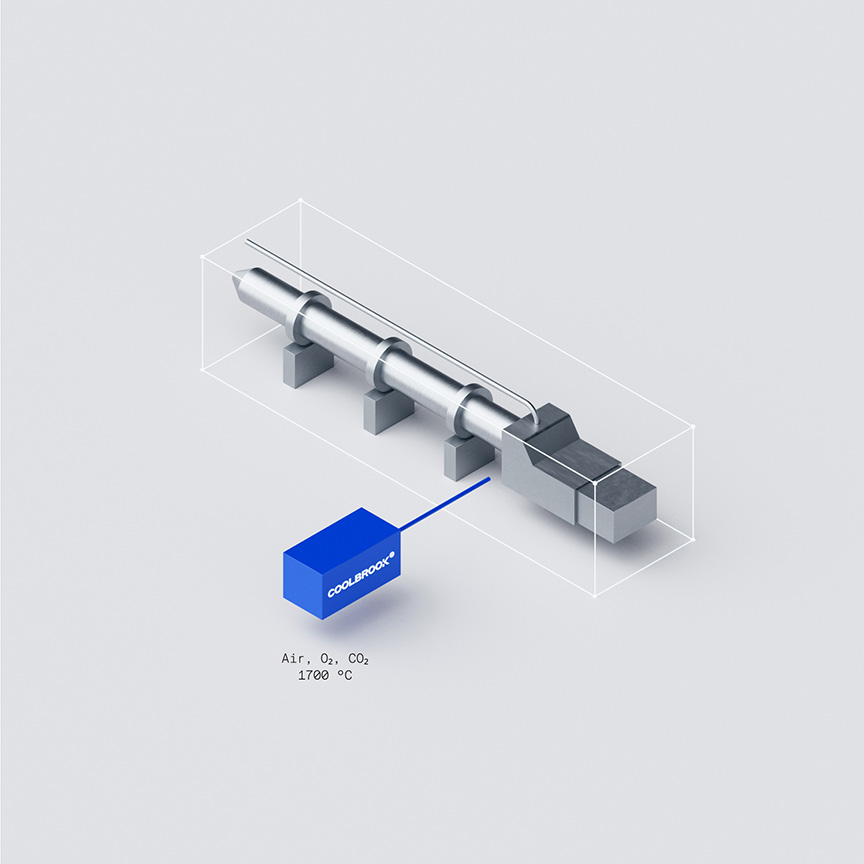
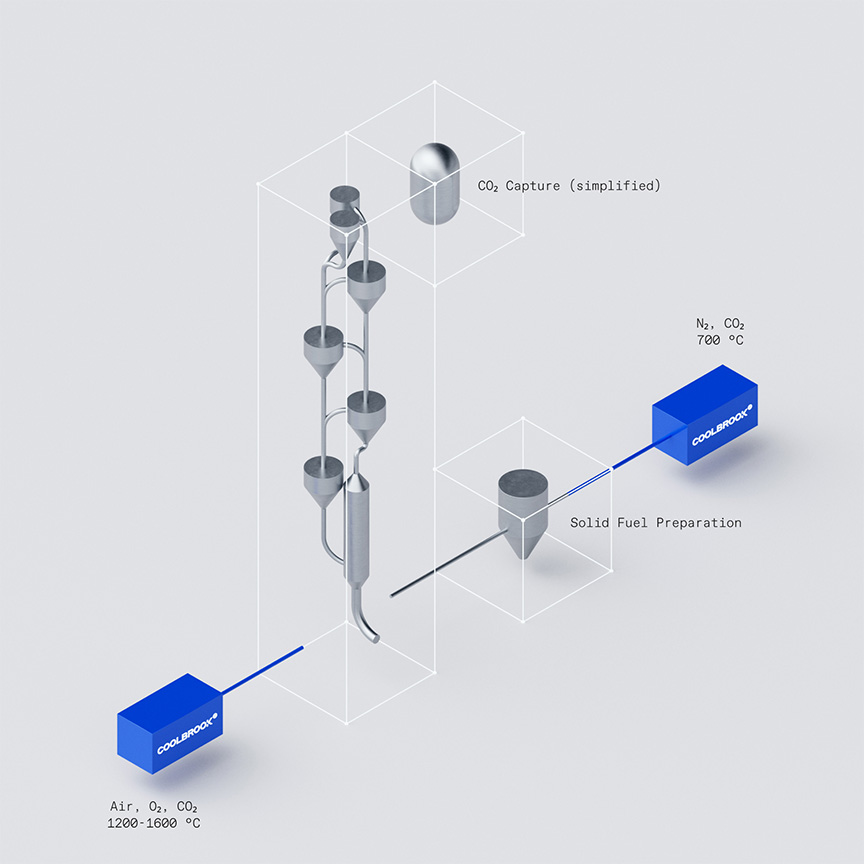
6. Drying in a cement or granulated blast furnace slag mill
RDH replaces fossil-fuel-fired hot gas generators and provides supplemental heat into a cement factory raw mill to boost drying capacity
- Coolbrook solution: RotoDynamic Heater to 700˚C
- Temperature in: ambient
- Temperature out: 700˚C
Customer benefits:
- Significant reduction in CO2 emissions or fully CO2 emission free process by replacing fossil fuels with renewable electricity
- Potentially increase production by boosting the drying capacity
- Cost savings from reduced carbon emission costs as existing fossil fuel solution (natural gas, LPG, diesel, etc.) are replaced
- Potential to utilize cheap renewable energy, further decreasing OPEX
7. Replace fossil fuels fired in a clay calciner
RDH replaces fossil fuels by providing heated air into a clay calciner
- Coolbrook solution: RotoDynamic Heater to 900˚C
- Temperature in: ambient to 200˚C
- Temperature out: 700˚C to 900˚C
Customer benefits:
- Significant reduction in CO2 emissions or fully CO2 emission free process by replacing fossil fuels from clay calciner with renewable electricity
- Cost savings from reduced carbon emission costs as existing fossil fuel solution (natural gas, LPG, diesel, etc.) are replaced
- Potential to utilize cheap renewable energy, further decreasing OPEX
- Enables utilization of exhaust gas heat energy resulting in improved energy efficiency and reduced operating costs
- Ability to optimize costs and emissions by selectively firing alternative fuels
Case study
White cement production with RotoDynamic Heater
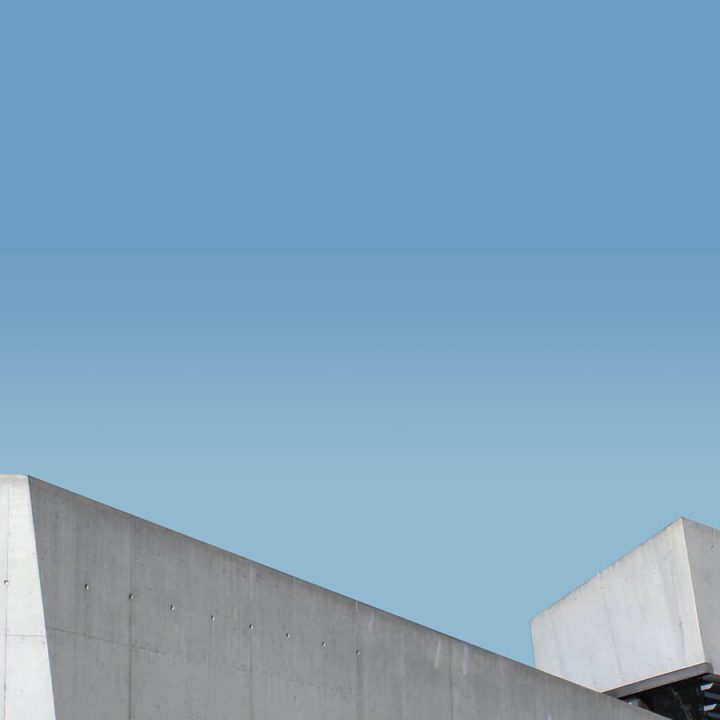
Decarbonize and increase production of white cement: Using RDH to heat up the combustion air fed to the kiln to decrease the required amount of fossil fuels (~50%) and increase production capacity by up to 25%
Benefits:
Decarbonization – Up to ~15% reduced CO2 emissions per ton
Replacing fossil fuels burnt in the kiln and pre-calciner with green electricity can reduce CO² emission by ~15%
AND
Option 1.
Increased production – Up to ~25% higher production capacity
Replacing the fossil fuels with RDH releases capacity in the preheater induced draft fan, enabling ~25% increased production capacity
OR
Option 2.
Trade non-utilized carbon allowances – Significant additional revenue from non-utilized allocations Maintaining the amount of production with significantly lowered CO2 emissions allow the non-utilized carbon allowances to be sold in the market.
Roadmap
Path to decarbonizing cement processes
2024
First applications and electrification of pre-calciner
- Pre-heating of raw materials and solid fuels
- Clay calcination
- White cement
- Replacement of fuel in pre-calciner
- Integration to main process
CO2 reduction -10%–30%
Temperatures 500 ˚C –1000 ˚C
2025
Electrification of main kiln
- Replacement of fuel in main burner
- Possibly combined with booster fuels
CO2 reduction -30%–40%Temperatures 1450+ ˚C
2030
Combination with CO2 capture
- Electric furnace + CCS
- Re-circulation of CO2
- High CO2 content flue gas
CO2 reduction -90%
Hear from Coolbrook cement customers and partners
The electrification of the production process is an important step towards fully decarbonising our cement operations. We are constantly looking for the best technologies and relationships to meet our Net Zero CO2 target. Our cooperation with Coolbrook will support us in achieving this ambition.
Roberto Ponguta
CEMEX Vice-president of Global Operations, Technical and Energy
JSW Group has set ambitious sustainability targets of reducing its specific CO2 emissions, aligning with the Sustainable Development Scenario of the International Energy Agency and India’s Nationally Determined Contributions. Deployment of RDH™ Technology is expected to have a sizeable impact on the decarbonisation of the Group’s manufacturing process. We are happy to onboard Coolbrook as a partner on our journey to reduce CO2 emissions and achieve our climate targets.
PK Murugan, President
JSW Steel Vijayanagar & Salem Works
As a founding member of the GCCA, we are committed to the sectoral aspiration of delivering Net Zero concrete by 2050. Towards this end, we are continuously striving to innovate at every stage of the whole life of concrete. Coolbrook’s RDH technology represents an exciting technological pathway that we believe has the potential to exponentially accelerate our progress towards full decarbonisation. Every megawatt of clean energy we add to our mix makes a big difference.
K C Jhanwar
Managing Director, UltraTech Cement Limited