Electric cracking: RotoDynamic Reactor cuts 100% of CO2 in steam cracking
Meet RotoDynamic Reactor™, the world’s best technology capable of electrifying one of the world’s most polluting industrial processes – steam cracking in the production of petrochemicals. Our technology is the solution to decarbonize olefin production.
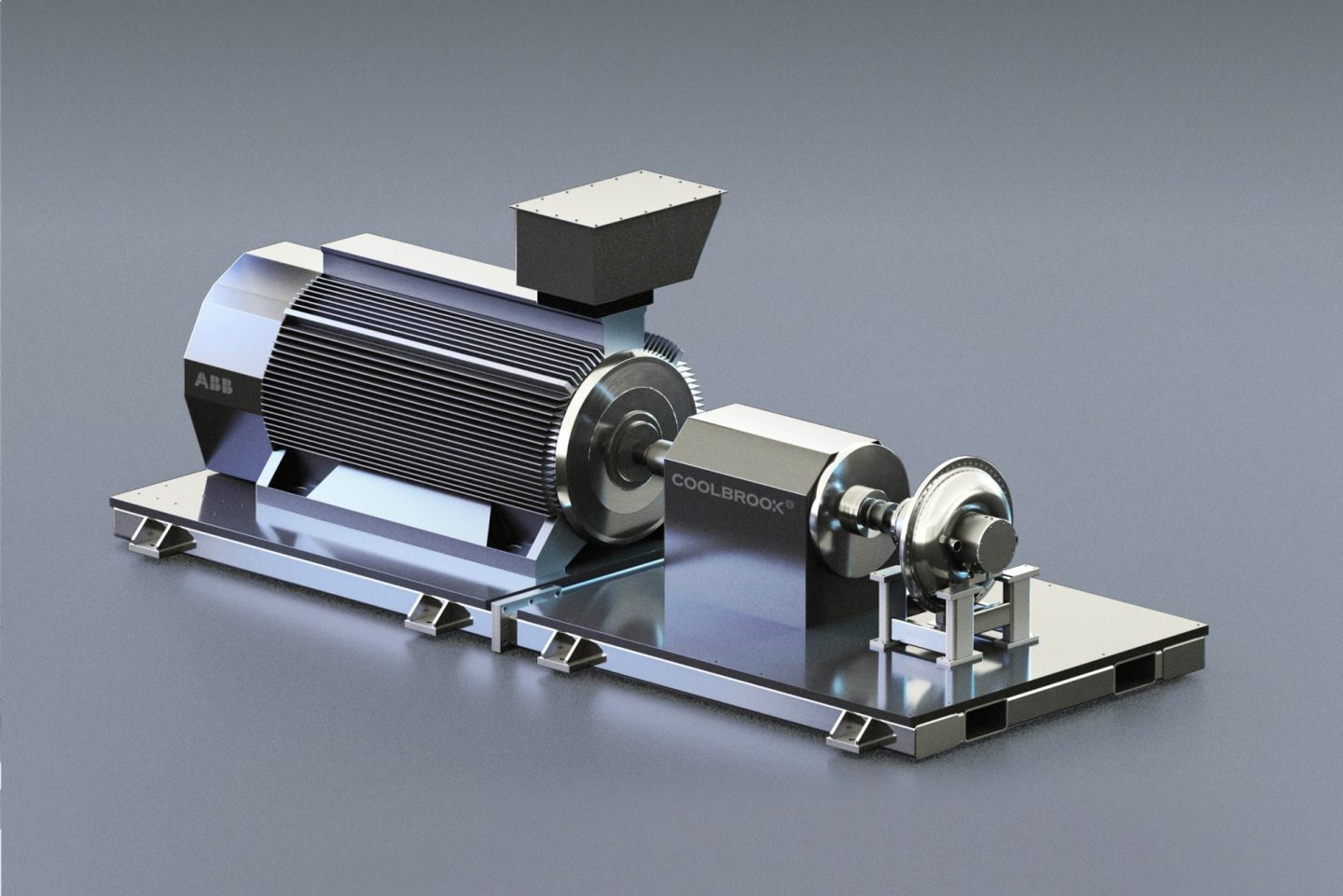
The Solution
Electric cracking is the new era in petrochemical production
Olefins, like ethylene and propylene, are the main raw materials in the chemical industry, used primarily in the production of plastics. Today, olefins are produced with steam cracking, a highly-polluting process that involves the high-temperature pyrolysis of hydrocarbon feedstock, diluted with steam, inside a cracking furnace.
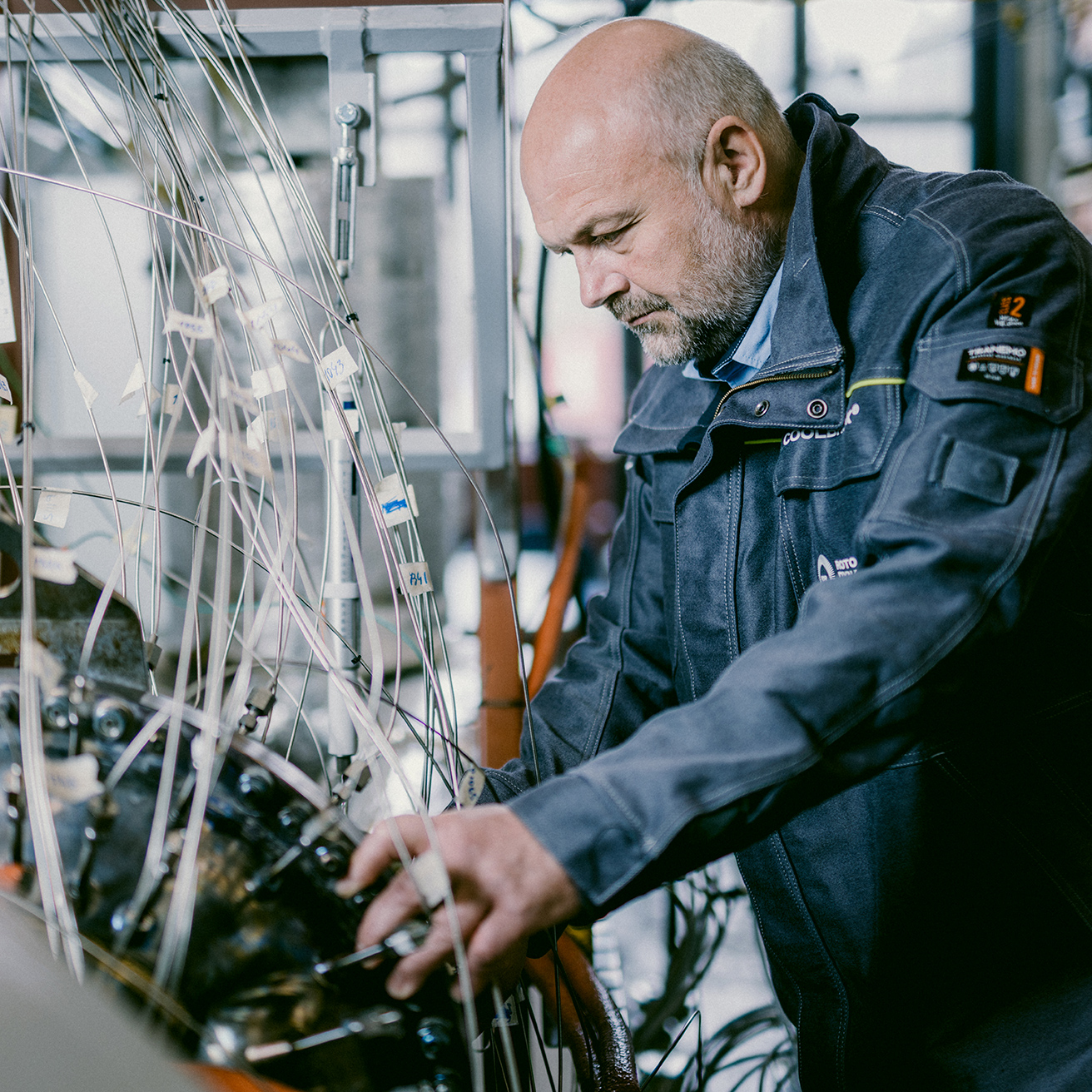
Electric steam cracking enabled by RotoDynamic Reactor
Innovative RotoDynamic Reactor™ (RDR), a pioneering technology in electric cracking, electrifies previously fossil-heavy steam cracking process, reducing process CO2 emissions by 100%.
This translates into global CO2 emission reduction potential of 300 million tons annually.
Moreover, the technology facilitates greater use of recycled and bio-based feedstocks, further lowering the lifecycle CO₂ footprint of plastics.
Comparison
Conventional cracking furnaces compared to the RotoDynamic Reactor cracking furnace
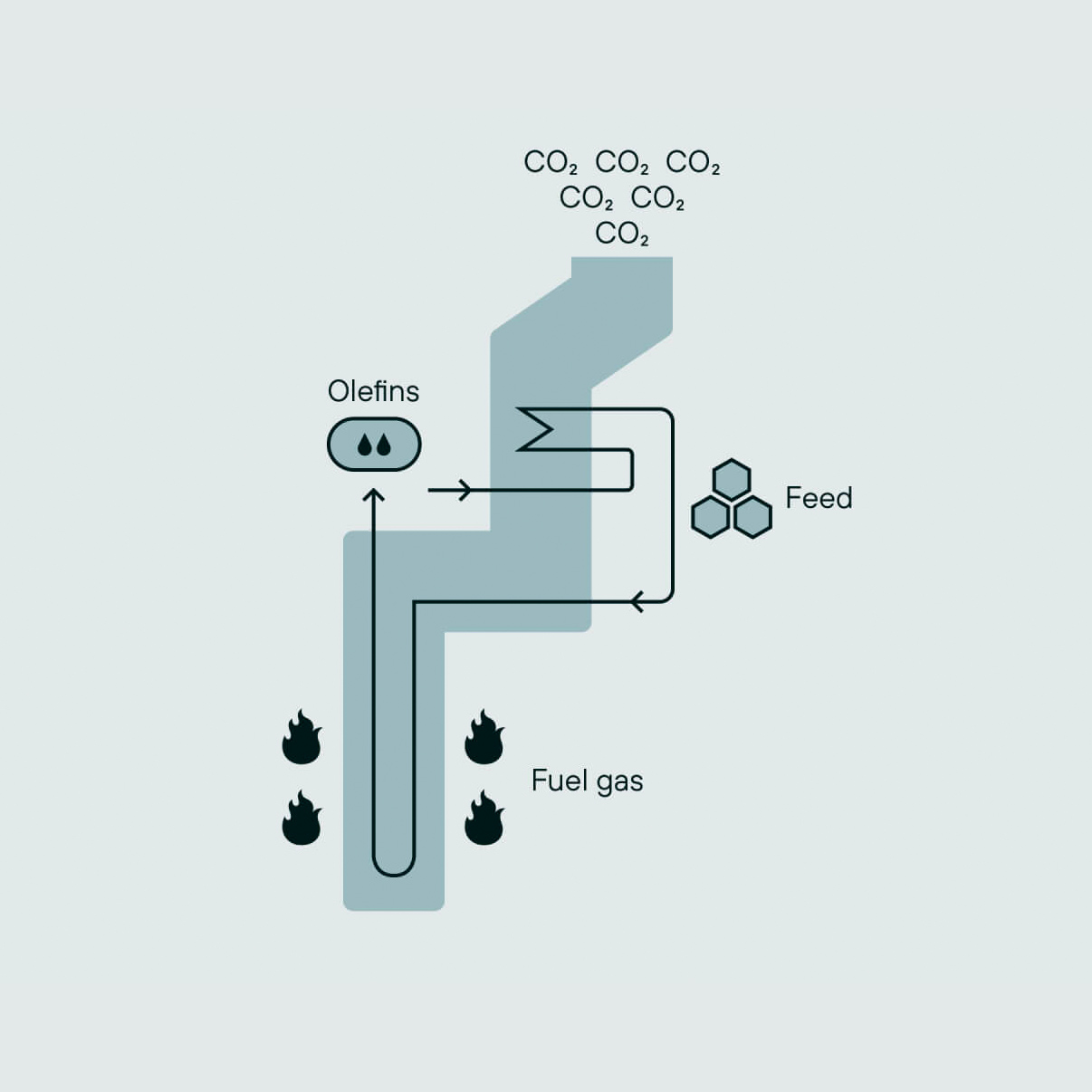
Conventional cracking
Olefins are traditionally produced by steam cracking ethane or naphtha at extremely high temperatures in large cracker furnaces. The reaction mixture is heated externally in tubular coils externally through tube walls using fossil fuels and significant amount of energy. This part of the process that is the main source of CO2 emissions in olefin production.
Electric cracking with RotoDynamic Reactor
Instead of heating the feedstock mixture indirectly, RotoDynamic Reactor’s high-velocity rotor blades create thermal energy to heat the mixture inside the reaction zone – quickly and efficiently. Using RDRTM renewable electricity, enables cutting 100% of process emissions.
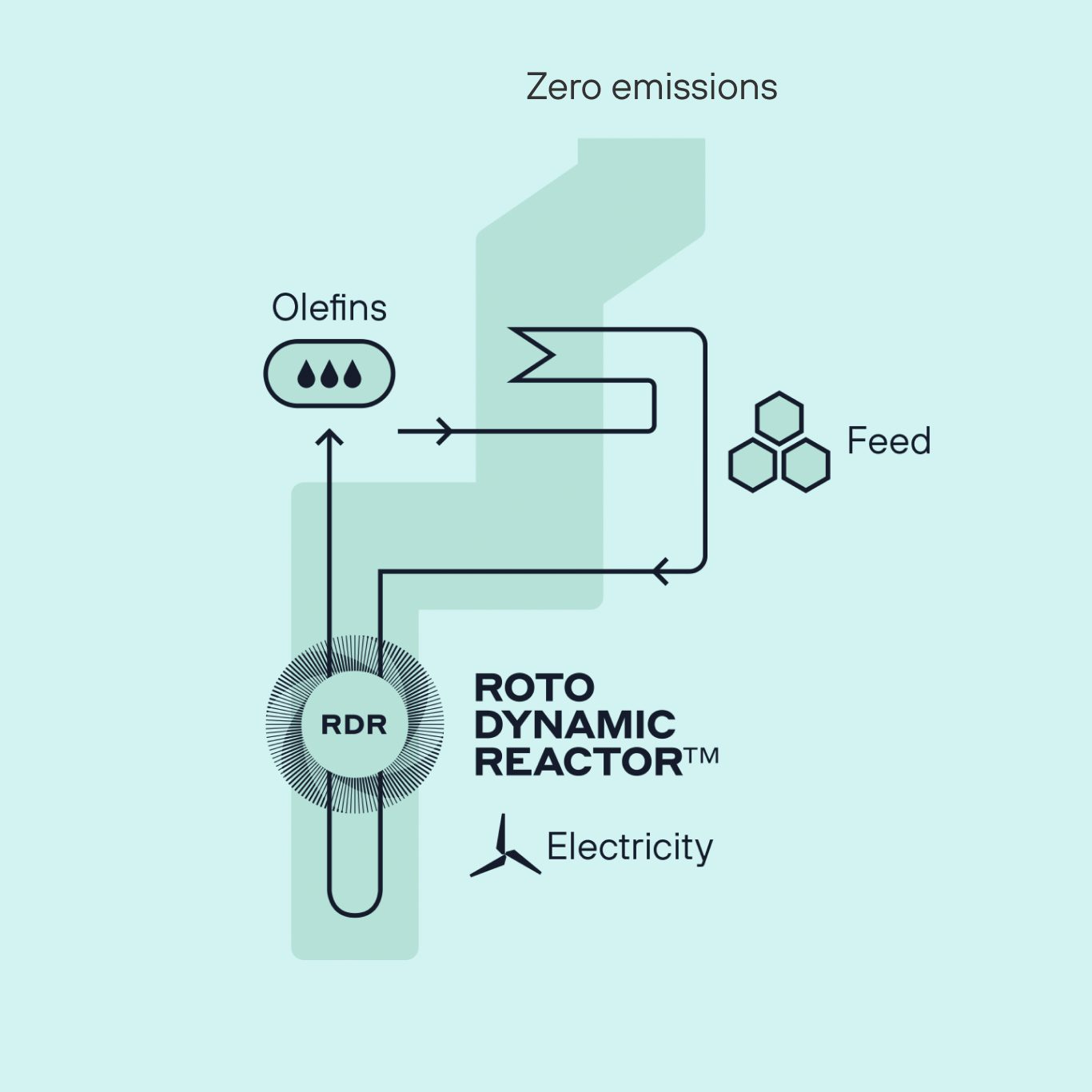
Advantages
Key advantages of RotoDynamic Reactor compared to furnace technology
With revolutionary benefits like zero CO2 emissions, less coking and improved profitability, RDR is an extremely attractive technology for petrochemical producers.
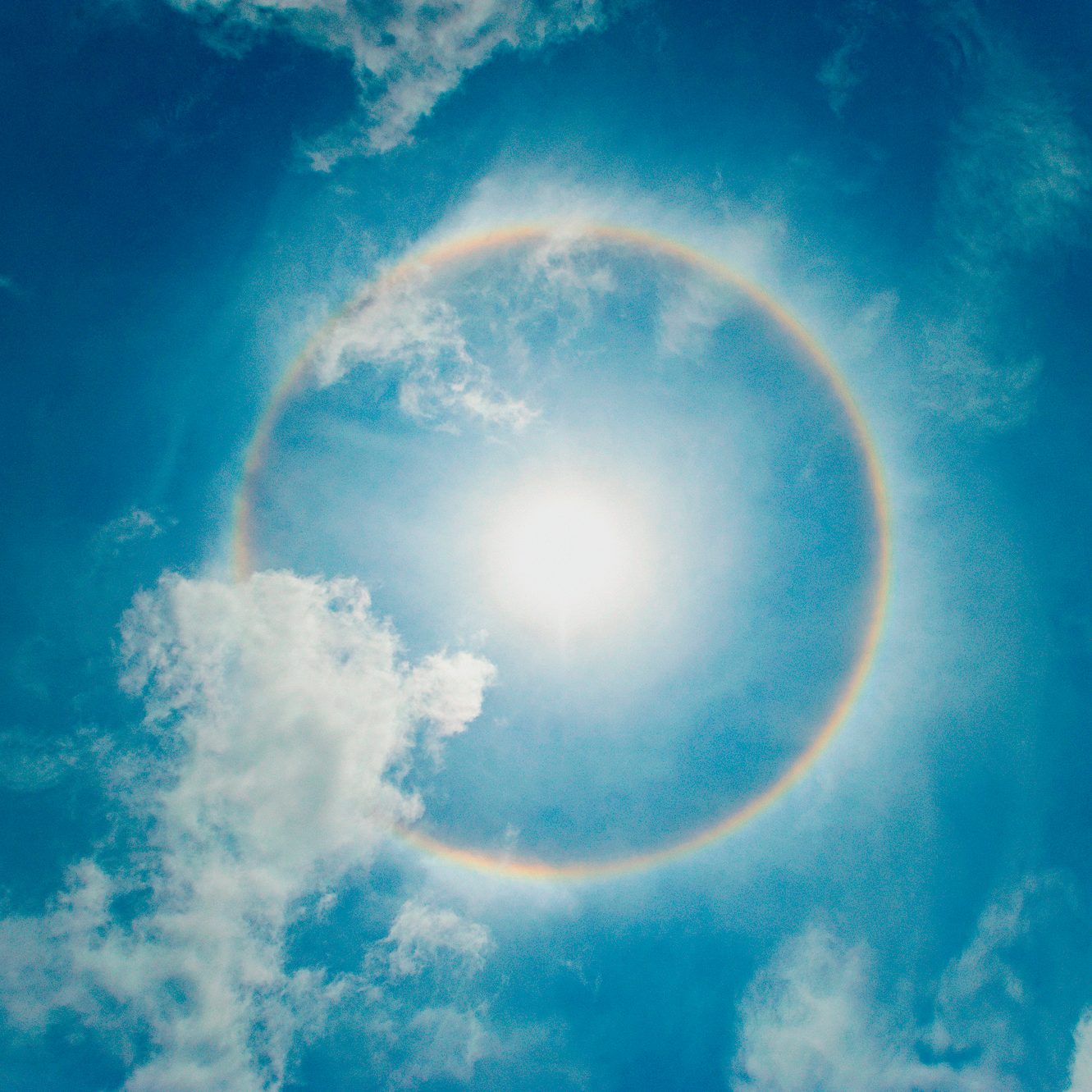
Reduction of emissions
- 100% reduction in process CO2 emissions from steam cracking
- Elimination of NOx and particulate emissions
- Improved energy efficiency
- Use bio-based and renewable feedstock enables further reduction in indirect CO2 emissions
Higher revenue
- Higher ethylene yield
- Higher total olefin yield
- Optimization of product mix value
- Longer run-length and higher uptime
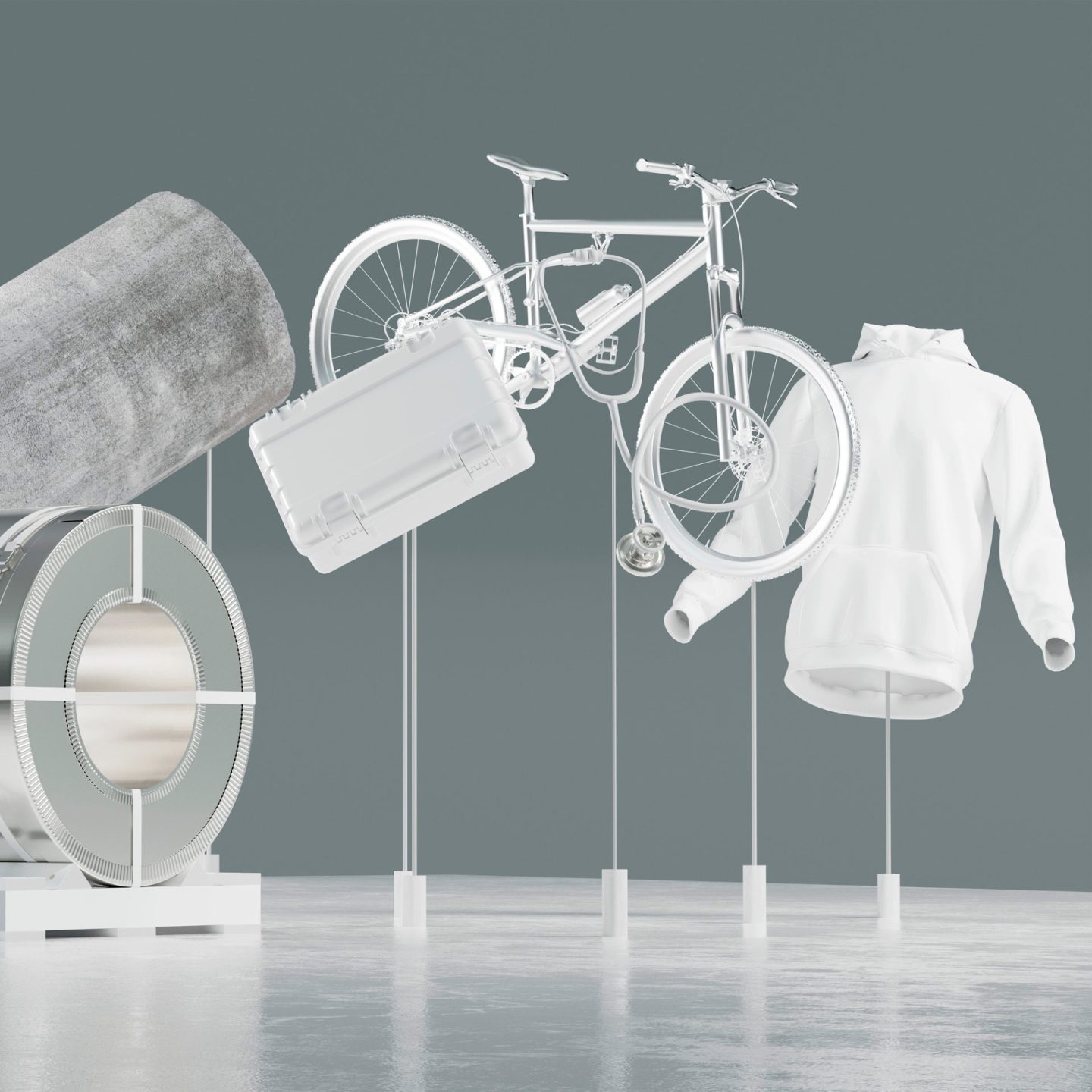
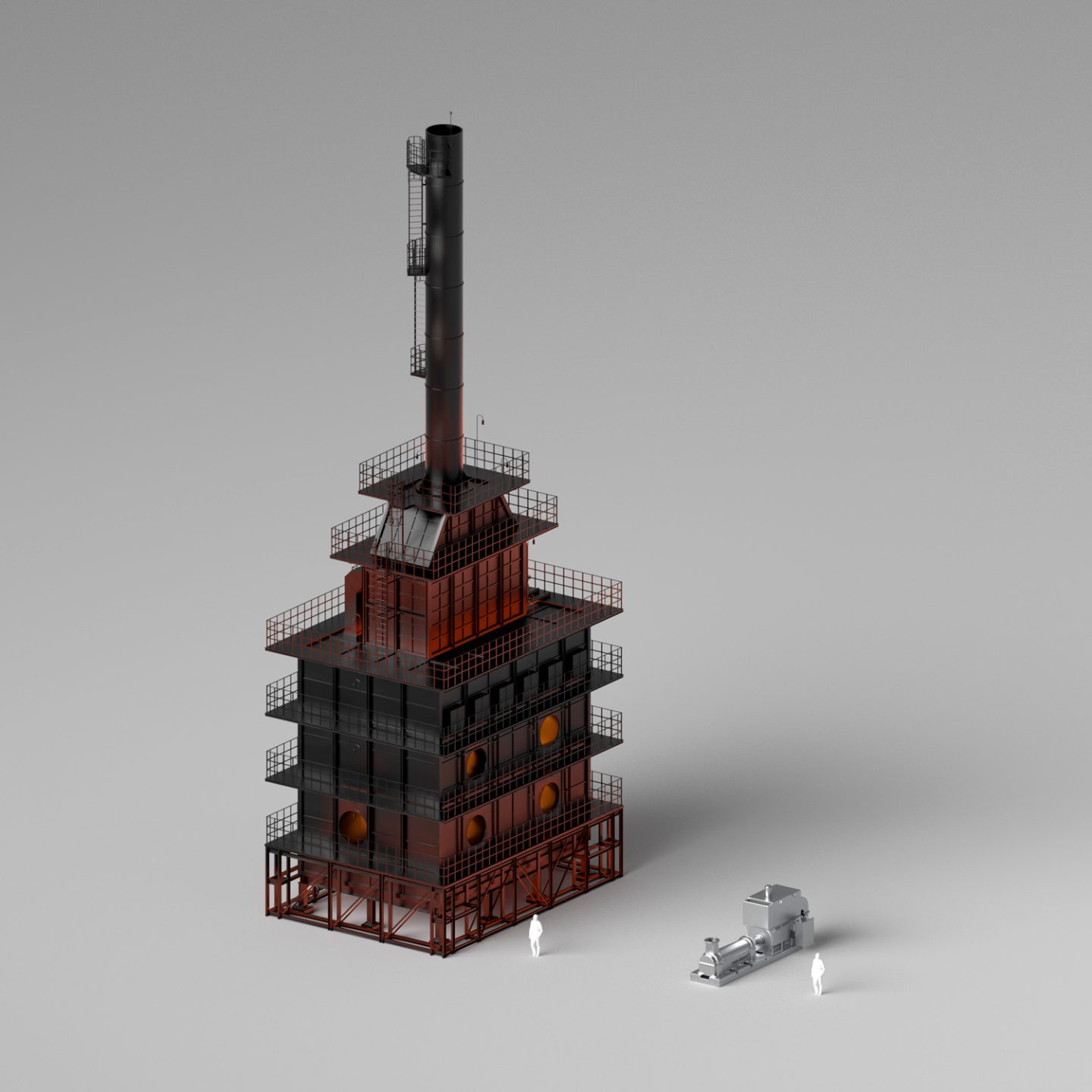
Savings in capital expenditure and operational expenditure
Lower operating expenses (OPEX)
- Easier maintenance
- Advanced controllability
- Less coke formation and less frequent decoking
Lower capital expenditures (CAPEX)
- Modular design, compact size and short construction time on site
Reduced coking enables improved productivity
Production at plants equipped with RDR runs smoothly compared to production at plants using conventional furnaces that require frequent decoking. RDR’s low coke production rate ensures uninterrupted olefin production.
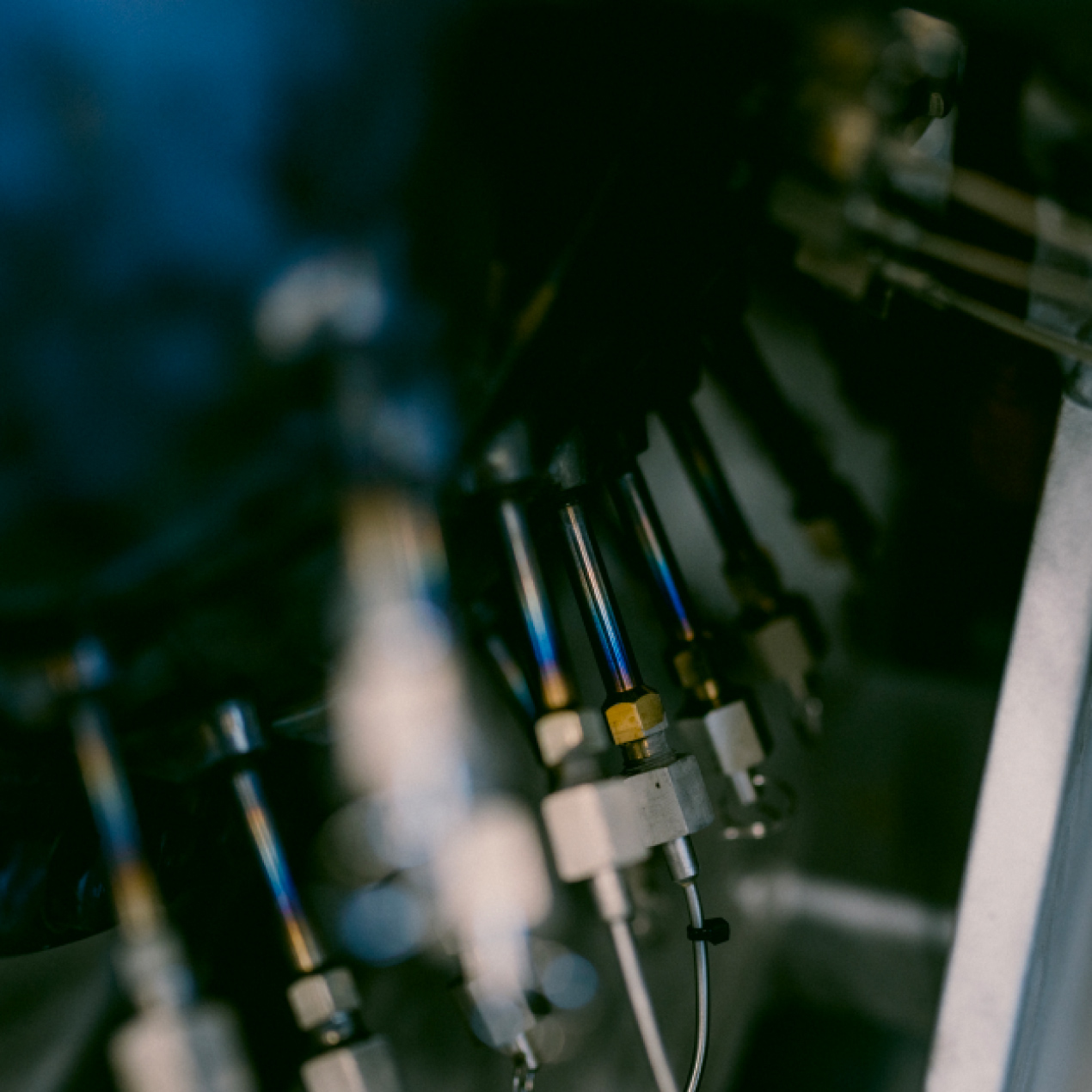
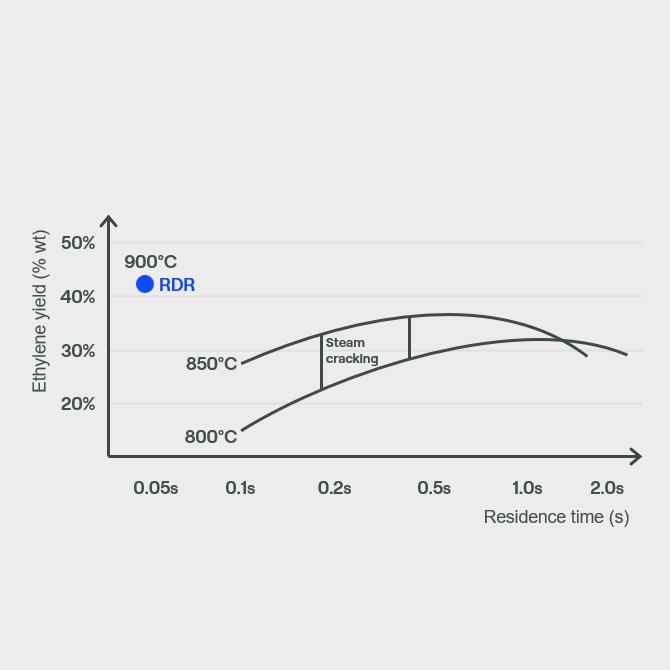
A fundamental revolution in ethylene yield and operability
Because RDR creates higher temperatures with a shorter residence time, it is able to achieve 20% higher ethylene yields. For petrochemical producers, that translates into increased annual profits of over 200M $ per 1 million metric tonnes ethylene plant. Lower metal surface temperatures mean that RDR is less prone to coking than conventional furnaces, resulting in lower operational costs and increased uptime.
The 20% higher ethylene yield also means fewer CO2 emissions per ethylene ton. Taking RDR into use also decreases capital expenditure when building a new ethylene plant.
Optimal temperature and residence time.
RotoDynamic Reactor has short residence at high temperature resulting in high yield with less energy and CO2 emissions.
Ready for commercial launch at scale in 2025
This game-changing electric cracking technology already exists today and a large and growing number of global industrial players have already expressed great interest in using it to cut CO2 emissions and meet crucial climate targets. Our RotoDynamic technology is currently being piloted, main focus being on RotoDynamic Reator since the beginning of 2024.
Coolbrook’s RotoDynamic technology has been piloted at the large-scale pilot facility since 2022, with the first phases of tests successfully completed in 2023.
In 2023, Coolbrook demonstrated electric steam cracking of naptha in its large-scale pilot plant in Brightlands Chemelot Campus, the Netherlands. The tests validated the potential of Coolbrook’s RotoDynamic Reactor Technology to replace traditional fossil fuel-based cracker furnaces with electric RDR units in the petrochemical industry.
The successful testing of RDR Technology also provides a solid basis for Coolbrook’s engineering, manufacturing, and supply of industrial scale RDR equipment to customers. As the next step, Coolbrook aims to deploy the RDR Technology at industrial scale and integrated to customer projects.
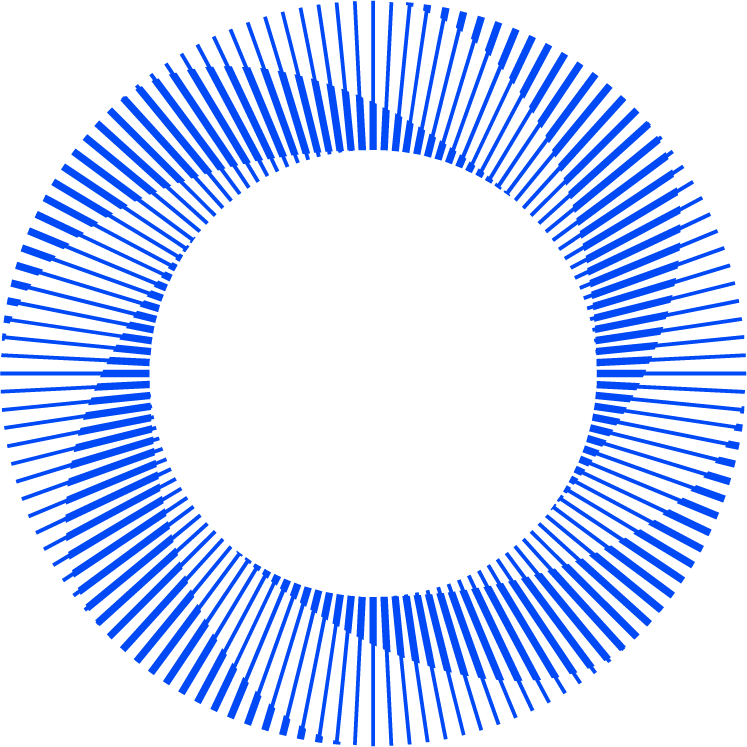
2011 – 2020
- Small scale pilot and proof of concept for technology
- Fundamental technology development with world leading universities
- Establishment of strong patent portfolio
2021 – 2023
- Construction and operations of large scale pilot in Geleen, the Netherlands
- Temperatures of 1,000+°C reached (RDH)
- Naphtha successfully cracked (RDR)
- Partner engagement across key industrial and academic sectors
2024 →
- First commercial RDH product launched in the beginning of 2024
- First units delivered in 2025
- Next products (RDR and Next Generation RDH) launched in 2025-2026
- Further expansion of partner network
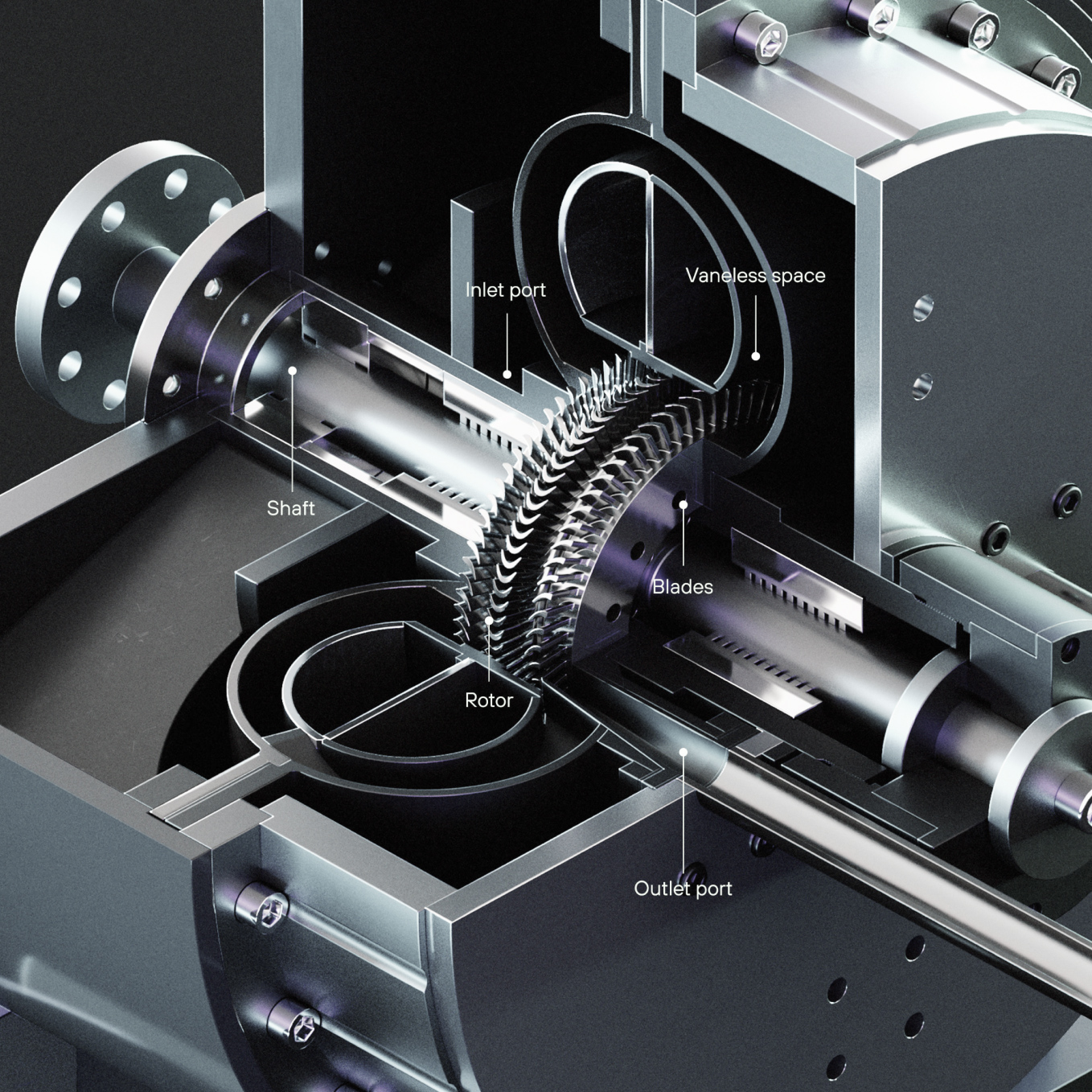
Electrification of steam cracking with RotoDynamic Reactor
RDR brings together space science, turbomachinery and chemical engineering. With aerodynamic action achieved through a rotating blade flow, RDR can replace conventional furnaces by directly imparting the rotor shaft’s mechanical energy to the hydrocarbon fluid needed to produce olefins.
RDR’s electric motor drives the rotors, gas is accelerated to very high velocities and then slowed down in the diffuser, creating a shockwave that converts kinetic energy into thermal energy.
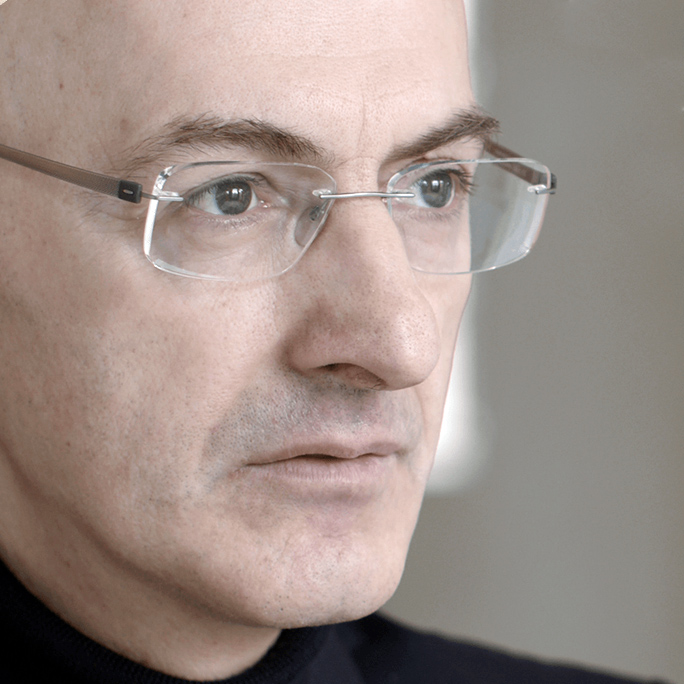
RDR has the potential to really become the new industry standard in olefins production.
Budimir Rosic
Professor, University of Oxford
Ph.D. (Aerospace Engineering)