Petrochemical industry decarbonization
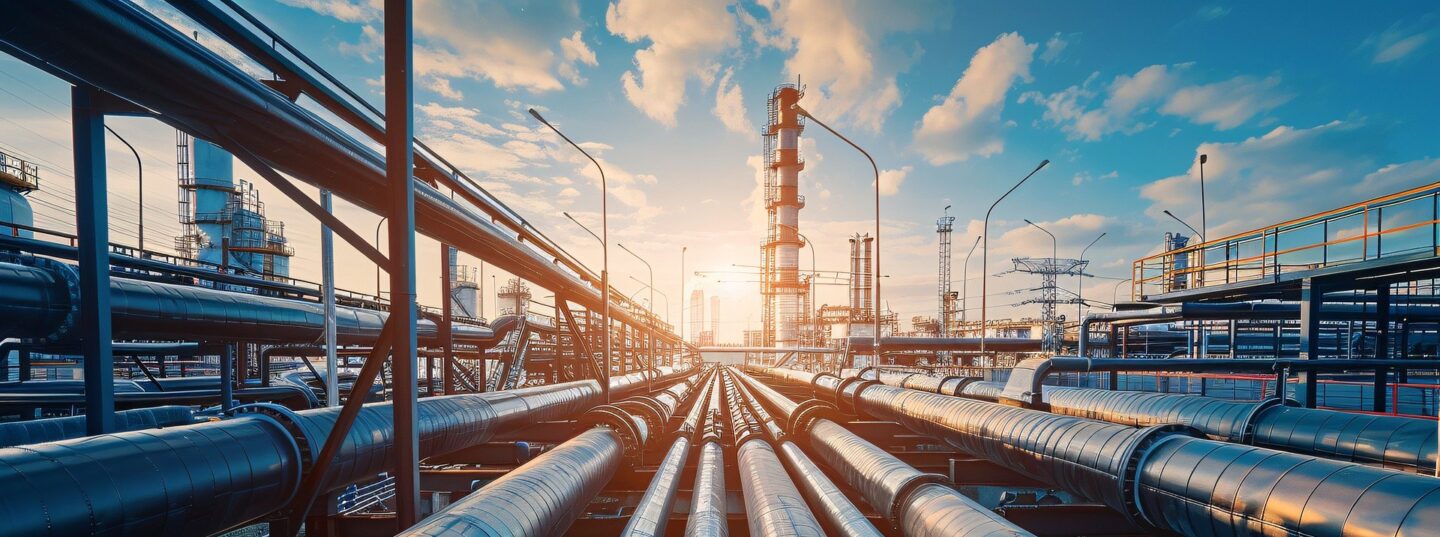
Electrification and decarbonization of petrochemical industry
The petrochemical industry produces around 1.5 billion tonnes of CO2 annually, accounting for 3% of global emissions, mainly due to its reliance on fossil fuels for energy-intensive processes like steam cracking. Decarbonizing this sector has been challenging, but industrial electrification offers a promising solution.
By adopting electric technologies, the industry can significantly cut emissions and support global climate goals. Coolbrook’s RotoDynamic Technology enables the decarbonization of high-temperature processes without burning fossil fuels. The Coolbrook’s RotoDynamic ReactorTM (RDR) can replace steam cracking furnaces, potentially reducing emissions by 300 million tonnes annually, while the RotoDynamic HeaterTM (RDH) can eliminate another 200 million tonnes through electric-powered heat generation.
Discover
RotoDynamic Technology in petrochemical industry
Coolbrook’s RotoDynamic Technology is the ideal solution for specific process heating applications in the petrochemical industry, offering an effective alternative to fossil fuel combustion.
RotoDynamic Reactor uses electricity to generate heat required for steam cracking of hydrocarbons. With high power density delivered by RDR rotors, the heat-up of the hydrocarbon feed is extremely fast, resulting in optimal yields for ethylene, propylene and other high-value products.
RotoDynamic Heater uses electricity to heat gases such as air, nitrogen, steam, carbon dioxide, and process gases to the required high process temperatures. These heated gases are then utilized outside the heater to replace the burning of fossil fuels in process heating applications. The RDH can also be applied in preheating feed materials in petrochemical production, significantly contributing to decarbonization while improving energy efficiency and reducing emissions.
Thanks to their compact design, both technologies can be seamlessly integrated into both new and existing industrial facilities.
Key benefits of the technology in petrochemical industry:
RDR-specific
- Up to 10% more valuable output product mix due to extremely quick heating and short residence time (RDR-specific benefit)
- Minimal coking
RDH-specific
- Scalability to high temperatures (up to 1700 ˚C degrees) and to size categories (50+ MW equipment size)
Both products
- High energy efficiency of 92 – 95% for the conversion of electricity to heat
- Compact equipment size and possibility to retrofit into existing industrial facilities
- Improved process energy efficiency
- Improved process control
- Competitive CAPEX and OPEX
- Medium-voltage system that can be installed at practically any site
Contact us
The process
Core use cases for decarbonizing petrochemical processes
RotoDynamic Reactor and RotoDynamic Heater can be fitted to new or existing industrial processes. High impact use cases in the petrochemicals production chain enable replacing fossil fuels in process heat generation.
RDRTM use case: Electrified steam cracking
Full electrification of steam cracking process
Use case and Coolbrook solution in brief
Replacing the conventional cracking furnaces with RDR where the heat is electrically generated directly in the hydrocarbon:
- Cracking feed capacity: 10-50+ t/hr
- Temperature out: Up to 950˚C
Customer benefits
- Elimination of CO2 emissions and related costs in the steam cracking process
- 20% higher ethylene yields, with significantly more valuable output product mix compared to traditional alternatives
- Limited coking, leading to higher availability of the machine
- OPEX and CAPEX savings compared to traditional solutions
- Significantly smaller footprint compared to conventional furnaces
- NOx and particle free process
RDHTM use case: Electrified heating for furnaces
Electrified heating of feed materials
Use case and Coolbrook solution in brief
Preheating feed materials for petrochemical processes with heat generated electrically by the RotoDynamic Heater:
- Heating medium: N2 / CO2 / Air / Methane
- Temperature out: Up to 1,300-1,500˚C (methane limited to 900-1,000˚C)
Customer benefits
- Full decarbonization of feed material preheating process by replacing fossil fuels with renewable electricity
- Cost savings from reduced carbon emission costs as existing fossil fuel solution (natural gas, LPG, diesel, etc.) are replaced
- Ability to accurately control the temperature in the process to optimize process parameters
- Potential to utilize low-priced renewable energy, further decreasing OPEX
- Utilization of exhaust gas heat energy resulting in improved energy efficiency and reduced operating costs
Roadmap
Roadmap to decarbonize petrochemical industry
2024
Finalizing pilot testing
Technology and improved yields already proven at our pilot site at Brightlands Campus in the Netherlands.
Full pilot testing expected to conclude by the end of 2024, including long-term naphtha runs.
The RDH product is now available for customer orders.
2025
Commercial launch of RDR
First commercial product available for customer orders
First deliveries of RDH technology to our customers begin
2026-27
Customer deliveries
Full-scale deliveries of the RDR technology to customers
Ongoing support and optimization services to ensure successful implementation across facilities.
Introduction to commercial product that is compatible with sustainable feedstocks
Customers and partners
Hear from Coolbrook petrochemical customers and partners
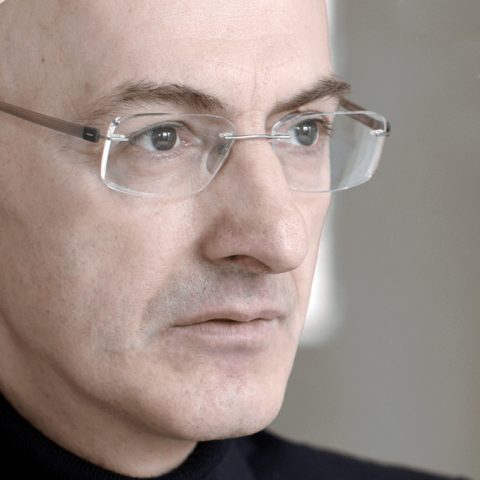
RDR has the potential to really become the new industry standard in olefins production.
Budimir Rosic
Professor, University of Oxford
Ph.D. (Aerospace Engineering)